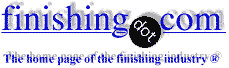
-----
How to do Nadcap Audit despite no Prime Customers?
December 6, 2010
My company has selected (lucky?) me to begin the process of preparing our plating company for Nadcap accreditation. We are being driven by one of our customers (not a Nadcap Prime) to get this certification. We are currently TS/ISO certified, so the AC7004 aspect of our audit appears fairly set.
My question is this; none of our customers are Nadcap primes, so how does this affect the audit process? I believe you are required to have a Nadcap prime part for the audit, so how is this handled if we are not a direct supplier to any Nadcap Primes? Has anyone out there successfully underwent a Nadcap audit who is not a direct supplier to any of the Primes?
Thanks.
Plating Shop Employee - Chicago, Illinois, USA
Mike,
Many of the second tier companies do not supply directly to the Primes, but if the Prime mandates Nadcap it applies throughout the supply chain.
You may wish to check with your customer that is asking for Nadcap which Prime it is for and whether there are any parts you are currently plating for them that is for a Prime. You can then target having these parts available for audit.
Before jumping with both feet into getting an audit from Nadcap it is worth visiting the PRI website and looking at the support they offer for companies intending to go for Nadcap (including eQualified and eQualPrep). This support is well worth looking at. It gives advice about how to prepare for an audit and what to expect from the audit process. It may well save you a lot of heartache later on.
I would also advise that you download the relevant checklists (sounds like AC7108 as a minimum, AC7108/1 if you paint as well) and go and do a gap analysis. I have done this for a couple of companies in the past and have illustrated how far away they were from the expected minimum standard, which made them pull back from jumping into the audit process too quickly.
Aerospace - Yeovil, Somerset, UK
December 8, 2010
December 9, 2010
Thanks for the advice Brian. We actually have a meeting with the customer who is requiring us to get Nadcap certification early next week, so hopefully we can get the information you suggested.
We have been to the e-audit website and I've been working through the checklists and supplier guides. Our current quality system is fairly robust, so I don't foresee to many major operational changes will be needed. It seems as though the Nadcap criteria is a little more detail oriented than ISO/TS, so we'll have to make some documentation/processes changes there.
Thanks again for the advice.
- Chicago, Illinois
Q, A, or Comment on THIS thread -or- Start a NEW Thread