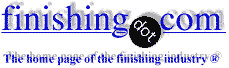
-----
Galvanized surface went dark grey in storage
I work at a continuous galvanizing line. Surface color of our product GI sheets changed to dark grey after keeping in warehouse about two or three months. In our line, we use HCl for pickling and double salt for fluxing and we preheat the sheets before dipping into molten zinc in which we put SHG zinc, zinc-aluminum alloy and lead, and production temperature of molten zinc is about 470 C. And we use chromic acid treatment for GI sheets.
I would like to know why the surface color of our product, GI sheets, has changed to dark grey within a short period of storage time and how we can prevent it.
An important point is that we've never found this problem in previous years. We've faced it in this year. It is very important for us.
Please, somebody kindly advice me.
Thank a lot.
Production Manager - Yangon, Union of Myanmar
December 1, 2010
S |
December 27, 2010 Sir: Galvanizing Consultant - Hot Springs, South Dakota, USA December 27, 2010 Hi Dear, - Dhaka,Bangladesh Please check the Silicon content in the Steel; it must be less than 0.02%. provided the problem is new. Umesh Dalela- Bhuj, Gujrat, India December 26, 2010 |
January 8, 2011
Dear Mr. Cook,
Thank you for your kind response.
We used cold rolled steel sheet in coil for galvanizing(dry flux type).
Composition of steel were C=0.04 ~ 0.05%, Si=0.008 ~ 0.03%,
Mn= 0.12 ~ 0.06%, P=0.007 ~ 0.033%, S=0.006 ~ 0.011% .
And SHG zinc about 100 MT & Lead about 30 MT in the kettle and we used zinc-aluminium alloy instead of pure Aluminium slab, by calculating Aluminum about 0.3% on total zinc usage.
Dear Mr. Hossain,
Thank you for your kind advice and we will follow it surely.
Dear Mr.Dalela,
Thank you for your kind response. The silicon content in our CRC stripes were about 0.008 ~ 0.03%. We used CRC coils from Uttam, Essar and Steel Co Gujrat of India. Uttam CRC have Si=0.008 ~ 0.018% only.
Thanks all of you for your help.
- Yangon, Union of Myanmar.
January 13, 2011
Sir:
A phosphorus above about 0.015% can give excessive reactivity of the steel and molten zinc giving grey, thick zinc coatings. Silicon looks good.
Regards,
Galvanizing Consultant - Hot Springs, South Dakota, USA

Q, A, or Comment on THIS thread -or- Start a NEW Thread