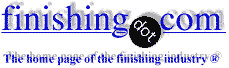
-----
How do I hard chrome plate multiple jobs in the same tank?

Q. Hi,
Ours is an export oriented C45 piston rods manufacturing unit. Diameter range is from 12 mm to 80 mm and length is up to 3.5 metres. Currently we hard chrome plate one piston rod at a time in a tank. We have four such 600 mm X 600 mm square tanks. Plating thickness is around 20-25 microns
We are planning to upgrade our plant as the existing structure is not conducive to mass manufacturing.
Please recommend
a) the shape of the tank
b) the size of the tank to ensure maximum output
c) do you recommend a thin rectangular tank in which 6 to 8 pistons can be plated at a time.
d) please suggest how do piston mass manufacturing units do hard chrome plating in the US, UK, Taiwan, China etc.
Please elaborate in detail so that I get maximum learning from your side.
Plating shop employee - Pune
November 17, 2010
by Clarence H. Peger
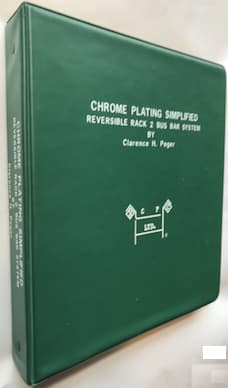
(copies are avail. in select libraries)
Very rarely available from
eBay or Amazon
or AbeBooks
(affil link)
A. That is a huge range of sizes. I have used large tanks that were about 1.5 meters deep and did not like having to drop the voltage/AMPS on the entire tank to start a new rack.
If you went to conforming anodes in your existing tanks, you would probably double or triple your plating speed. That would negate new tanks in most facilities. By using conforming anodes, you could rack 2 or 4 of the same parts and still get the higher speed plating--If your power supply is big enough.
An additional benefit is you can tweak the anodes and hold the dog bone effect on both ends to a minimum. This does require anodes for each length of parts. The diameter is not a problem as long as the largest diameter has a 15 mm spacing part to anode. I used about 4.6 volts which gave me 4 amps per sq inch. You still lose a lot of the energy to the formation of H2 and O2, but you waste a lot less power that normally goes to generation of heat. Caution, this will normally give you MORE than 25 microns per side per hour.
The nice part of conforming anodes is that you can build them yourself. I used molds that were made to the specifications of Clarence Peger, deceased, but his book on the two buss bar system is probably still available if you look hard enough. Lots of great practical information in it after you sort out the self serving BS in it.
In addition, you do not have to worry about trivalent buildup.
For optimum use, I would strongly recommend the use of a ceramic (porous) pot purifier. The last time that I checked, there was pictures and some information available on the net by googling 2 buss bar chrome plating. I bought these from Peger and can not overstate the help that it is to a chrome plater.
I would definitely use a chromic acid reverse etch tank with this. Later at another facility, I did it in the plating tank, but I had small areas to be plated on large parts. Not much area, long plating times and regular use of the porous pot.
Using conforming anodes can easily double your production after the learning curve is done. Note that this is still massively cheaper than rebuilding an entire line.
- Navarre, Florida
Outstanding reply, James. Thanks
Regards,
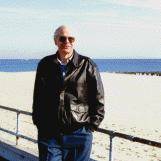
Ted Mooney, P.E.
Striving to live Aloha
(Ted can offer longterm or instant help)
finishing.com - Pine Beach, New Jersey
November 18, 2010
What is the distance I should maintain between the job and the anodes for say 12 mm, 50 mm and 80 mm pistons?
Neel Pandya [returning]- Pune, Maharashtra, India
November 20, 2010
A. For the 80 mm, I would use about 15 mm spacing, Note that at this size, the conforming anode could be round OR square. At 100 mm, I would go with a round one.
This same anode will work very well for the other smaller sizes because of the increased anode to cathode size ratio, quite nicely compensates for the increased distance.
Note that what I have said is for "mesh" anodes and not stick anodes that you have boxed. The outgassing at the anode creates a significant flow thru the mesh which keeps a high chrome ion concentration at the part--very uniformly.
I also hope that you noted that I said that the anode can be tweaked for more uniform deposition of the plate. For your part, this will involve removing some of the anode from the top and a bit more from the bottom. This will have the anode looking more like castellated rather than a nice smooth top and bottom. You remove a bit and then gradually remove a bit more until you get the magic amount. Note that this negates the use of robbers as well as rough ends and excessive grinding.
Jim
- Navarre, Florida
November 22, 2010
Q, A, or Comment on THIS thread -or- Start a NEW Thread