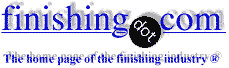
-----
Bubbles in e-coat
Electrocoating bubbles in certain areas only
Q. I wonder why the nc appears only at specific areas instead of at whole surface? Product is running in same line, same process, spec and chemical -- yet sometimes we have this kind of nc.
I suspect it is not coming from our ecoat line, probably the porosity of materials are different for every batch, and that causes the bubbles. Please we need your help on determining the root cause. It is caused by air/water entrapment before coating process?
- johor malaysia
May 13, 2024
Tip: This forum was created to help build camaraderie through sharing tips, opinions, pics & personalities.
The operator & those readers who want that might not engage with anonymous posters.
A. Hi Naza.
More info is required. What is the substrate? If it is cold finished steel the likelihood of porosity is very small; if it's sand castings, the likelihood is much greater.
Photos to mooney@finishing.com for posting here would help: One person's "bubbles" are another person's blisters, another person's pits, another person's fisheyes, another person's lack of coating due to air entrapment. Finally, sand or grittiness under the coating due to inadequate cleaning is sometimes misidentified as bubbles -- some areas of a component may come clean easier than other areas. Do you see a waterbreak-free surface before phosphating?
Pictures revealing exactly where the bubbles occur may help suggest their cause. Thanks.
Luck & Regards,
Ted Mooney, P.E. RET
Striving to live Aloha
(Ted can offer longterm or instant help)
finishing.com - Pine Beach, New Jersey
⇩ Related postings, oldest first ⇩
for Shops, Specifiers, & Engineers
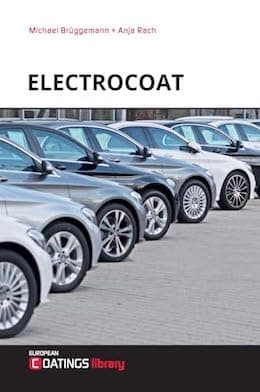
avail from eBay, AbeBooks, or Amazon
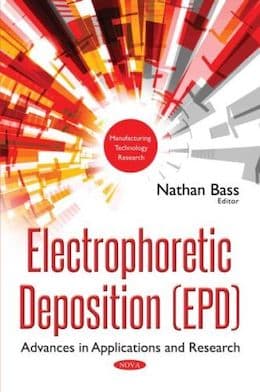
avail from eBay, AbeBooks, or Amazon
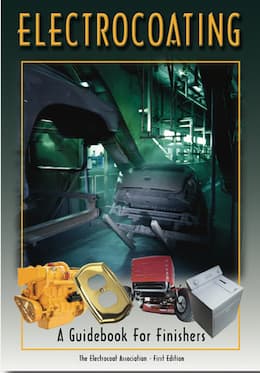
avail from AbeBooks, or Amazon
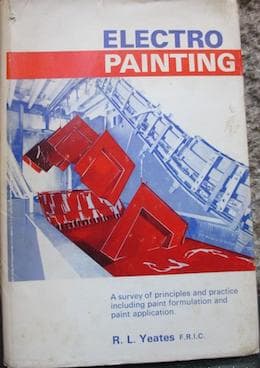
avail from eBay, AbeBooks, or Amazon
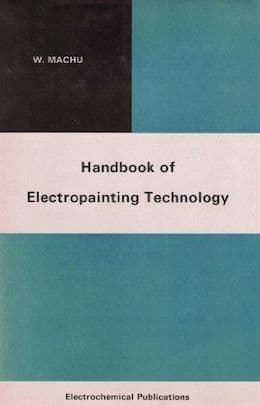
avail from eBay, AbeBooks, or Amazon
(as an Amazon Associate & eBay Partner, we earn from qualifying purchases)
Q. We stamp a part and then stake a nut to the thru hole. The part is then sent out for E-coat. This part is used as a height-adjustment slider in a seat belt. For the last 12 months we have had a 5% fallout of bubbled e-coat between the staked-nut and the slider. We have been making this part for 6 years and up until a year ago this was not a major issue. Our customer has indicated that we are not alone with this and several coating facilities have indicated that their supplier (PPG or Dupont) has changed the formulation of the e-coat. Our coater has said that there is not much they can do; the cleaner used by them will get trapped and then boil out.
Since I am new to this field I would like your input and what can we do to help our processor. The part is stamped using a water soluble oil, it is then staked without oil. By the time the processor gets the parts 7 days have passed and the parts are pretty much dry to the touch.
Quality Director - Dolton, Illinois, USA
November 17, 2010
A. How are you cleaning the cutting fluid off of the part before shipping it? I am greatly bothered by your saying that the part is nearly dry to the touch after 7 days. Shipping wet parts is an invitation for a disaster.
If I read your post correctly, some cleaning fluid is being trapped between the stamping and the friction fit stake. At you end, I would reduce the hole as much as possible to decrease the space between contact spots and the pin.
Since you have cutting fluid trapped between the stake and the part, I would add a cleaning step to the flat and possibly the stake before the staking operation.
The painting vendor can help by putting the parts in a clean rinse tank for a couple of minutes before going into the cleaning tank. This traps water and not cleaning fluid, which should reduce the problem. A couple of trips between the hot rinse tank and a cold rinse tank prior to cleaning tank will help even more. This hot/cold cycle will also help to remove some of the reduced amount of cleaning fluid.
Finally, can the parts be sent thru a warm oven prior to the actual painting to remove as much liquid as possible.
- Navarre, Florida
A. If you already know that the bubbles are coming from some cleaner that is stuck to the part and boiling out in the cure oven, I would look at your rinse stages after the cleaning stages. What is your washer setup? Do you have a dip clean and then a spray clean followed by a dip rinse and spray rinse or is it dip stages in the whole washer? If you have a dip rinse I would look at getting more agitation in your rinse tank after the cleaner or dumping the stage more often. If you have a spray rinse: look for plugged or blown off nozzles and adjust spray nozzle pressure to 12-15 psi. Hope that helps.
Adam Krey- Whitewater, Wisconsin, USA
A. I will give the coater the benefit of the doubt that he cleans the parts properly.
In this case I would look for the rupture voltage.
If your e-coat solution is contaminated, the rupture voltage is low. As your supplier to check your rupture voltage.
Is the solution's conductivity OK or too high?
In any case, I would start with a simple process - purging permeate.
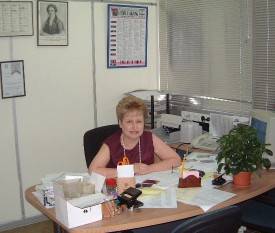

Sara Michaeli
Tel-Aviv-Yafo, Israel
Q, A, or Comment on THIS thread -or- Start a NEW Thread