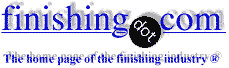
-----
Peeling CuNiCr plating - help with root-cause?
Hi. I am a Supplier Quality Engineer and have a die-cast Al housing which has peeling Cu/Ni/Cr plating (5/20/0.1 µm respectively) - see attached pic.
It's likely been exposed daily to steam and vapour from alkaline foam cleaning agents and acid-based disinfectants (over many months). What are your thoughts on likely root-cause; faulty plating or environmental factors?
Thanks for your support
Jim
Supplier Quality Engineer - Linlithgow, West Lothian, Scotland
October 27, 2010
Jim,
It is difficult to actually put a finger on the cause of the failure as some of your details are a little sketchy. What I would say is that the environment sounds pretty aggressive and heat plus low pH is always going to be difficult to resist.
Aerospace - Yeovil, Somerset, UK
November 1, 2010
JIM,
PEELING PROBLEM,
1) FIND OUT PEELING BETWEEN COPPER TO NICKEL OR NICKEL TO NICKEL OR NICKEL TO CHROME ? Too many reason for peeling.Substarte is not clean good ,passivation during plating cycle,electrical problem,contamination in tank .
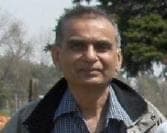
Popatbhai B. Patel
electroplating consultant - Roseville, Michigan
November 10, 2010
From the photograph I find that the edges are quite sharp,
these edges are to be rounded off , or better if you could have an Chamfer of 1.5 mm x 45 degree peeling from these area will be eliminated good luck
ELECTROPLATERS - BELGAUM, KARNATAKA, India
January 18, 2011
I have a problem for nickel chrome plating for ferrous and sus alloy metal. The process from pre-treatment, followed by nickel strike, nickel plating and chrome plating but the product still peeling and reach the raw part. The chemical content is in range, voltage and time also in range. How can I solved this problem.
NUR HADIchemical technician - KULAI, Malaysia
May 10, 2011
May 12, 2011
For plating on Al base,sequence should be as follows.
Degreasing or vapour degreasing
Cathodic cleaning
Acid Dip (Nitric acid & Ammonium Bifluoride)
Zincating
Electroless nickel or cyanide copper
nickel
chrome
Here acid dip composition & zincating will eliminate
your peel off problem.
Electroless nickel instead of cyanide copper will
give better adhesion but cost will go up and productivity may also be low.
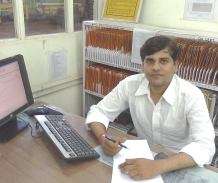
Manoj Kushwaha
plating & painting - Rampur, India
Thanks, Manoj.
I've never heard of cathodic cleaning of aluminum. Are you sure about that part?
Regards,
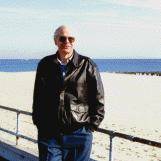
Ted Mooney, P.E.
Striving to live Aloha
(Ted can offer longterm or instant help)
finishing.com - Pine Beach, New Jersey
May 12, 2011
November 28, 2011
Sir,
We are doing cathodic cleaning of AL components & also supplying Al base nickel plated handicraft items for years but not have any customer complaint regarding peel off.
For reference, pl. go through below details which also have cathodic cleaning in process.
Historical Articles
July, 1952 issue of Plating
The Plating of Aluminum Articles as a Production Process*
A.W. Wallbank, B.Sc., F.R.I.C.
Managing Director, Ionic Plating Company, Ltd., Birmingham
RESEARCH AND EMPIRICISM
In many branches of scientific endeavour, the line of progress has been pointed by men who have not had the advantage of an academic training. Throughout the history of any applied science, it is remarkable how frequently important developments have had their birth in the minds and their infant nurture at the hands of men to whom a laboratory would be foreign territory.
The livelihood of a practical man may well depend upon his success or failure and, therefore, when he is faced with a problem he must grope for the answer. He follows many blind alleys, he often interprets his observations quite wrongly, but sooner or later his patience, skill, intuition and even good fortune, may provide the key.
Nowhere is this more true than in electrodeposition. The solution formulations, now justified scientifically, were first established by trial and error. Even such modern developments as organic brighteners date back to the glue and liquorice of the old platers. Admittedly, the rapid-strides of the last twenty years in electrodeposition have resulted from the work of trained technicians, but they would not have known where to start if the practical plater had not pointed the way.
The process that is to be described in this paper is today an anachronism a legacy of the early days of plating, which has persisted in the plating shops of the English Midlands and the North, and which has yet to be equalled in its own particular field by a process of laboratory origin. One of the most remarkable features of this process has been the limited extent of its knowledge. It is widely known on many shop floors, dimly appreciated in a few works laboratories, and, until recently, was quite unknown in research organizations. Even more remarkable has been the queer lack of awareness of the extent of aluminium plating by commercial interests, who from time to time "discover" how to plate this metal. Advertisements appear in the press announcing "Aluminium can be plated at last," or some such slogan, although every hollow-ware counter in the stores of this country has been loaded for the last two decades with chromium plated aluminium goods.
PROBLEMS IN THE PLATING OF ALUMINIUM
There are at least four difficulties which must be overcome before a successful plating process can be operated upon aluminium.
Aluminium surfaces rapidly acquire an oxide layer when exposed to air or water and this layer tends to inhibit good adhesion of an electrodeposited film.
Aluminium is one of the more anodic metals. There is therefore a tendency to form unsatisfactory immersion deposits in the first seconds of exposure to a plating solution of one of the more negative metals. For the same reason it becomes vitally important that any electrodeposit on aluminium shall be continuous or the basis metal exposed at pores will corrode preferentially, and set up severe local attack, which will spread along the interface and cause complete breakdown.
Aluminium has few commercial applications in its pure state. It is usually alloyed with other metals and the range of alloys of aluminium with which a plater would be expected to deal is very great. A plater working on steel or brass rarely has to modify his plating procedure to accommodate differences in carbon content, or in zinc copper ratio. He only encounters difficulty in the comparatively rare cases of the higher alloy steels or the leaded brasses and special bronzes. With aluminium, on the other hand, he is far more likely to meet with high manganese, copper, magnesium or silicon alloys than with the pure metal. The reaction of aluminium is markedly affected by its alloy constituents, and a successful commercial process must therefore accommodate what are in effect widely different metals.
Finally, the "plateability" of aluminium is affected by its physical and metallurgical history. Most platers are already only too well aware of the difficulties inherent in castings whether sand, gravity or pressure-die, and these difficulties apply equally to cast aluminium, while even wrought aluminium alloys vary in their reaction to the cleaning and plating sequence according to their previous work-hardening and heat treatment.
METHODS FOR PLATING ALUMINIUM
Methods for plating aluminium are very prominent in plating literature, and most of them depend either upon deposition of a metallic film by immersion, which film is used as the base for subsequent electroplating, or upon anodizing followed by modification of the anodic film to enable the electrodeposit to adhere to the basis metal. The most popular of the immersion methods is that using sodium zincate and this has been extensively studied by a number of investigators including Bullough and Gardam1, Keller and Zelley2,3 and Bailey4. It was originally patented by Hewitson5 in 1927.
The anodizing method has been described by Close6, and earlier by Fischer7, and several variants have been patented8,9,10.
In the hands of competent platers, any of these methods are capable of giving good results, but they each have serious defects when considered as commercial plating processes. Deposition of a film by immersion relies essentially upon the single electrode potential of the basis metal. If that metal is uniform, an even immersion film will result, but any local variations in the basis metal, so that two closely adjacent areas have different electrode potentials, must inevitably effect seriously and uncontrollably the character and thickness of the immersion film. In commerce, few aluminum articles are sufficiently homogeneous to guarantee satisfactory immersion film. Very many articles are indeed constructed from different aluminum alloys which may have been subjected to different degrees of cold working and heat treatment. Still worse, it is not uncommon for an aluminium article to have steel, brass or solder in some part of its assembly. Again, an- article to be plated must be suspended on a conducting wire or jig and the contact between that wire and the article itself is an area of differing electrode potentials. No plater can be expected always to use aluminium wires of the same material as the article he is plating. Hence, if the success of any of the immersion processes depends essentially upon a thin, uniform and adherent initial film, commercial adoption of these processes will tend to be limited to the plating of simple wrought aluminium components.
The anodizing process is also inapplicable to complex assemblies, as the anodizing treatment will inevitably attack preferentially any part of the assembly which is not aluminium or a high-aluminium alloy. It will obviously necessitate the use of aluminium wires and jigs and equally obviously, the cost of production will be equivalent to superimposing a plating process upon an anodizing process. Like the, immersion processes it will be most readily applicable to homogeneous wrought aluminium articles.
HISTORY OF THE ELECTROLYTIC (VOGT) PROCESS
The first workers on the process to be described are believed to have been German, but it was a Norwegian, B. Vogt, who first began to develop it on a small scale at Newcastle-on-Tyne about 1929. Vogt, with the assistance of an able team of practical platers, soon had sufficient confidence in the process to bring it to Birmingham. There, with great courage and resource, he built up a fine business with over 100 employees engaged wholly upon the plating of aluminium. His layout, his use of conveyors, and his adoption of semi-automatic equipment was far ahead of his time, but the outbreak of war and the attack on Norway caused him to leave a trade which could ill spare his loss.
As the men trained by Vogt began to spread throughout the plating trade, the process was adopted by many other companies and became quite widely used, although it has only twice been the subject of technical papers. The first occasion was an unpublished review before the Birmingham branch of the Electrodepositors Technical Society by Vogt himself about 1936; more recently a detailed description of a process of the Vogt type was published in the technical press by Fyfe 11.
DESCRIPTION OF THE VOGT PROCESS
The process is in line with modern views in agreeing that the best foundation for an adherent deposit is a thin, uniform and continuous layer of zinc. It does not, however, rely on immersion for this film but on an applied current. The zinc is thereby deposited evenly over every part of the article being plated, whether its components are cast or wrought, pure or alloyed, soldered or riveted. This zinc film is too thin to withstand a nickel-plating solution and it is therefore reinforced by a thin deposit of brass.
The nickel solution which follows is very low in chloride and is operated under conditions which yield a soft, unstressed- deposit. The adhesion of the nickel is enhanced by stoving, after which the article can be mopped and chromium plated in the normal way.
Cleaning Sequence
Trichlorethylene may be used for very greasy work or as an operation in the polishing shop between mopping and colouring. It is not normally included in the cleaning sequence. This consists of:
(a) First electrolytic clean
(b) Swill
(c) Acid etch
(d) Swill
(e) Second electrolytic clean; followed by plating sequence
(a) First Electrolytic Clean
Composition
Caustic soda [caustic soda beads in bulk on
Amazon [affil link]
.... 4.5 oz/gal (28 g/l)*
Sodium cyanide .... 4.5 oz/gal (28 g/l)
sodium carbonate
⇦ on
eBay or
Amazon]
.... 2.25 oz/gal (14 g/l)
Conditions
Temperature .... 70 F
Voltage .... 7 volts cathodic
Time .... 3-5 min
Anodes .... sheet steel
Tank steel .... unlined
Control
No analysis. The bath is regenerated two or three times and then replaced. The solution surface is skimmed daily.
(c) Acid Etch
Composition
sulfuric acid, R.O.V .... 50 per cent by volume
Nitric acid, conc. .... 50 per cent by volume
Conditions
Temperature .... room temperature
Time .... 2-5 seconds
Exhaust .... Venturi
Tank .... earthenware
Control
None. The solution is replaced when no longer effective
(e) Second Electrolytic Clean
Composition
caustic soda ⇦liquid caustic soda in bulk on
Amazon [affil link]
.... 2.25 oz/gal (l4 g/l)
Sodium cyanide .... 2.25 oz/gal (14 g/l)
Conditions
Temperature .... room temperature
Voltage .... 7 Volts cathodic
Time .... 10-30 sec
Anodes .... sheet steel
Tank .... steel unlined
The success of the cleaning sequence and indeed of the whole process depends largely upon the skill, experience, and care of the operator. The times of immersion are varied by a good operator to suit different types of work, and the presence or absence of soldered joints; his acquired knowledge enables him to judge from the appearance of the work at each stage whether that stage is satisfactory or not. Similarly he can assess by watching his work when a particular solution should be regenerated or replaced.
Preliminary Plating Sequence
The plating sequence is:
(f) Zinc plate
(g) Brass plate
(h) Swill
(i) Swill
(j) Nickel plate
(k) Swill
(f) Zinc Plating
Composition
Zinc chloride .... 0.08 oz/gal (0.5 g/l)
Sodium cyanide .... 0.08 oz/gal (0.5 g/l)
caustic soda ⇦liquid caustic soda in bulk on
Amazon [affil link]
.... 1.7 oz/gal (10.5 g/l)
Conditions
Temperature .... room temperature
Current .... 5 asf
Time .... 20 sec
Anodes .... sheet zinc (taken out between loads)
Tank .... unlined steel
Control
No analysis. The sole method of control is by appearance of work which should be a uniform bronze colour. If the deposit becomes blue-black the zinc deposit is too thick and the solution needs dilution.
(g) Brass Plating
Composition
copper acetate [affil link] .... 2.0 oz/gal (13 g/l)
Zinc chloride .... 2.0 oz/gal (13 g/l)
Sodium cyanide .... 5.0 oz/gal (31 g/l)
sodium carbonate
⇦ on
eBay or
Amazon]
.... 1.5 oz/gal ( 9 g/I)
Sodium bi-sulphite .... 2.0 oz/gal (13 g/l)
Conditions
Temperature .... 80-90 F
Current .... 7-10 asf
Time .... 8 sec
Anodes .... sheet 70/30 brass
Tank .... unlined steel
Control
Analysis for copper, zinc and "free" cyanide. Control by deposit appearance, which should be a yellowish white.
(i) Double Swill
The rinse between brass plating and nickel plating must be very quick and very thorough. The customary acid dips which are interposed between cyanide and nickel solutions cannot be employed on such thin flash deposits.
(j) Nickel Plating
Composition
Nickel sulphate .... 40 oz/gal (250 g/l)
Magnesium suIphate .... 16 oz/gal (100 g/l)
Sodium chloride .... 0.75 oz/gal (4 g/l)
Boric acid .... 4 oz/gal ( 25 g/l)
Conditions
Temperature .... 115 F
Current .... 10-15 asf
pH .... 5.6
Filtration .... continuous pressure filtration through kieselguhr
Agitation .... air
Anodes .... depolarized; bagged
Tank .... steel, rubber-lined with lead-covered steam and air pipes
Anode .... area three times cathode
Rate .... 0.0001 inch in 12 min
Control
pH twice daily. Solution analyzed weekly. When deposit becomes hard and bright the solution is purified by the Liscombe method.
Stoving and Subsequent Plating
After rinsing and draining, the nickel-plated articles are stoved for half an hour at a temperature of 450 F. It is claimed that this treatment "makes a good deposit better and a bad deposit worse", and it is certainly true that if an article is free from blisters after stoving, it can be nickel finished and chromium plated without fear of "lifting" at a later stage. Once stoving has been completed the nickel-plated article can be given any sequence of subsequent deposits or of finishing treatments.
Reclamation of Rejects
With good operators the incidence of rejects is no higher with aluminium than with other basis metals, and such rejects as do occur can be stripped for replating comparatively easily. This can be achieved either by a reverse sulfuric strip in the normal way or by careful immersion in 50 per cent by volume nitric acid.
Applicability to Alloys
One of the great advantages of the process is that the great majority of aluminium alloys can be plated through exactly the same sequence. Some of them darken during the cleaning stage, but the adhesion of the final deposit is not affected. Alloys containing more than 3 per cent magnesium are the only doubtful range, but even these are possible if care is exercised during the cleaning.
FUTURE DEVELOPMENTS
It is hoped that a critical investigation of this process will first eliminate its defects, and then develop from it a far better, simpler and quicker process.
The greatest drawback to the process is its dependence on the training and intelligent observation of the operator. At present his skill is far more vital to the success of the process than the chemical or physical control and, therefore, fully automatic plants for plating aluminium would be a risky undertaking. This reliance on the personal craft of the operator is obviously the first point at which the research attack should be directed.
In the process itself, the cleaning sequence is reasonable and the pre-plating baths are quick and effective, but their formulation is archaic. At the time when this process was first developed brass and zinc solutions of this type would not be uncommon, but they are certainly anachronistic in 1952. Surely systematic investigation will rapidly discover what is the optimum range of the substances in solution and thereby deduce a more rational method of make-up and control.
The nickel solution is very good it is indeed one of the best general-purpose nickel solutions in use today. It might be possible to modify it to increase current density or gain brightness without undue stress, although in the present state of nickel supplies a more fruitful line of investigation would be to follow a thin deposit of nickel from this solution with some of the deposits or combinations of deposits now being adopted as alternatives to nickel-chromium.
The most important line of research in this subject is, however, closely allied to the fundamental causes of porosity in plated deposits. Plated aluminium has been widely used on hollow-ware domestic articles subject to frequent washing and cleaning and it has been successful in this field. It has also been employed for functional engineering purposes with reasonable success; for instance, the Tourist Trophy has been won on several occasions by motorcycles with nickel/chromium-plated pistons, but its application to articles subject to the full severity of the weather has been very limited. Before the war, many bus fittings, exterior and interior, were of plated aluminium and lasted very well, but the car and cycle industries have been reluctant to adopt it until more evidence of its performance is available.
When a plated aluminium surface is exposed to the weather a pore may be more serious than on steel or brass as the corrosion appears to spread along the interface and destroy adhesion over a wide area. This is often allied to thick, unsatisfactory zinc deposits such as are common with the immersion method, and it can be claimed for the electrolytic method that it has appeared to last better on exposure tests than its modern rivals. However, until there is a more definite lead from research the only safe method is to deposit an adequate thickness of metal on aluminum to ensure minimum porosity.
ACKNOWLEDGMENTS
The author is indebted to his co-directors of the Ionic Plating Company Limited, for permission to publish this paper. He also wishes to acknowledge the skill and resource of the many practical platers who have developed and operated this process, with special mention of his colleague, Mr. G.W. Airey.
REFERENCES
1. W. Bullough and G. E. Gardam, J. Electrodepositors' Tech. Soc., 22, 169 (1947).
2. F. Keller and W. G. Zelley, Proc. Am. Electroplaters' Soc., 36, 143 (1949).
3. F. Keller and W. G. Zelley, J. Electrochem. Soc., 97, 143 (1950).
4. G. L. J. Bailey, J. Electrodepositors' Tech. Soc., 27, Advance Copy No. 10, (1951).
5. E. H. Hewitson, U. S. Patent 1,627,900 (1927).
6. G. C. Close, Light Metal Age, 4 (March 1946).
7. J. Fischer, Metallwirtschaft, 11, 473 (1932).
8. W. J. Travers, U. S. Patent 1,971,761 (1934).
9. J. Fischer, U. S. Patent 2036,962 (1936).
10. E. M. Julick and W. A. Mehmel, U. S. Patent 2,430,468 (1947).
11. R. Fyfe, Metal Industry, 77, 300 (1950).
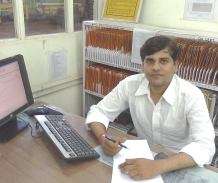
Manoj Kushwaha
plating & painting - Rampur, India
Q, A, or Comment on THIS thread -or- Start a NEW Thread