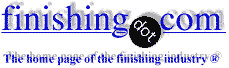
-----
Deionizer Silicate Levels Suddenly Skyrocket
October 25, 2010
We currently employ a mixed bed deionizer (with course sand, and fine paper filtration prior to deionization) to provide our plating shop with high quality water. We subcontract weekly silicate testing on our hot DI seal tank for our chromic acid anodizing process, to ensure minimal contamination. Recently, we noticed serious paint adhesion problems, initially flagged by a failed salt spray corrosion resistance test (ASTM B117). After being given an early warning on the results, we began checking as many parameters as we could.
Here is the order of what I found:
- Chromic acid anodize test coupons processed (336 hour salt spray test)
- Silicate levels in DI hot seal tank checked - found to be at 0.297 ppm (the day after coupons were processed)
- Silicate levels in DI hot seal tank checked - found to be at 7.5 ppm (1 week later)
- Additional silicate testing performed (using colorimetric test kit) - very high silicate levels found in water coming out of DI bottle (around 10 ppm at this point)
- Testing performed at the same time revealed water between filtration and DI bottle to have around 4ppm of silicates.
I've heard that DI bottles can just "let go," but I have not experienced anything this serious. Previous week's silicate tests showed around 0.2 ppm regularly. Also, something seems peculiar given that the corrosion failure occurred at a point where silicate levels were acceptable (spec calls for seal water to have less than 4.0 ppm).
My questions are:
- Is there something that can come down the incoming water line that can cause the DI bottle to release its collected contaminants? Too low a pH perhaps?
- Could that unknown factor be the cause for the early and anomalous failure, or is it more likely that we're dealing with two unrelated issues?
- We are looking to add a second, polishing DI bottle to the line. Is it expected that such a drastic hit to our incoming line would throw off the second bottle as well, or would it act as a safety net in a situation like this?
- Is there a way to continuously monitor silicate levels? I think all I've been able to find are spectroscopic and colorimetric tests.
- Is 4 ppm of silicates actually an acceptable level in the seal tank? We had had another failure roughly a year ago, and I went back and checked records, and the silicates had steadily increased to around 0.900 ppm during that period. It has caused some doubts for me.
If I have failed to ask some pertinent question here, please throw me a line and answer it anyways!
Thanks for any help!
Nathan
Manufacturing Engineer - Sidney, BC, Canada
Silica is the first ion to leak from a mixed bed or an anion exchange resin bed when it reaches exhaustion.
Measurement by conductivity or resistivity will not detect this silica leakage because it is not conductive. And, at exhaustion, the silica concentration in the water leaving the resin can be several times higher that the feed water due to a phenomenon know as chromatographic peaking. Long before a conductivity breakthrough, silica will begin to leak off the resin. In fact, during early silica leakage, the conductivity of the water may actually drop.
There are a couple of possible solutions to this. One, as you suggested is to run two tanks in series and to always have the freshest tank in the polishing position. If your water composition is relatively constant, you can change out the tanks based upon the volume of water processed, safely before the silica leakage begins, instead of by conductivity. This will take a little trial and error.
Lyle Kirman
consultant - Cleveland Heights, Ohio
November 2, 2010
Hello, Nathan. Lyle is the true expert on this subject, I'll just add a little detail. When you have two cannisters in series as he suggests, put a sample port in the line between the two cannisters. Then, regularly analyze for silica at that point so that you know when it has bled through the first cannister and is starting to load the second. Either your silica test or the conductivity sensor will indicate that you need to get that first cannister rotated out. If you keep on top of it, you'll never have silica get into your seal tank. Another solution that I wouldn't mind hearing Lyle comment about is to use an RO system for primary purification followed by DI polishing. If I'm not mistaken, the RO will easily reject the silica and then you can reasonably monitor your resin status by conductivity/resistivity alone.

Jon Barrows, MSF, EHSSC
Kansas City
November 2, 2010
Thank you both for your responses.
We have installed a second polishing DI bottle with a sample port between the two to test for silicates, as well as a conductivity alarm to hopefully give us an early warning - this was our plan from the beginning, so I'm pleased to see that your suggestions support it! Due to our recent investment in deionization, we would likely not be looking to go the RO route for a while.
I am still confused as to why it may have failed corrosion resistance, THEN tested within spec for silicates, then let loose, but I suppose it's entirely possible that these were unrelated failures (there were significant adhesion failures during the period of high silicates, but not during the period of poor corrosion resistance, even though that caused us to take a closer look).
Thanks again,
Nathan
- Sidney, BC, Canada
November 18, 2010
John's comments are very complimentary, and his technical expertise is evident. As John suggests, an RO before the mixed bed resins will have a remarkable effect in extending the life of the mixed bed resin tanks. Typical rejection of silica is 97-98% by the RO membranes. This is more than should be expected, since at neutral pH values most of the silica is not ionic and the molecular weight is relatively low. Exchange frequencies will be reduced by a factor of twenty or more!
Lyle Kirmanconsultant - Cleveland Heights, Ohio
November 29, 2010
Q, A, or Comment on THIS thread -or- Start a NEW Thread