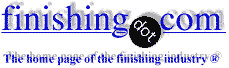
-----
Tarnishing of tin plating, Problems & Solutions
Q. Good morning,
We are doing tin plating on brass material.
After storage in-house some parts getting blackening.
10%.
Where is the issue; we are still not finding it?
Kindly give your feedback.
And QC Engg - Ahmadabad (Gujrat) India
April 23, 2023
A. Hi Sudarshan,
Please advise what you are doing. Is this bright acid tin or alkaline tin stannate or what. And what is your plating cycle? Specifically, what steps do you follow after tin plating?
See the simultaneous responses below from Phil Pace and Sara Michaeli, advising of the need for a post-dip in chromate or an alkaline tank. David Shiu makes the same point on this thread, and Robert Probert makes it repeatedly on many threads.
Luck & Regards,
Ted Mooney, P.E. RET
Striving to live Aloha
(Ted can offer longterm or instant help)
finishing.com - Pine Beach, New Jersey
Q.
Sir/Mam,
We are very troubled by tarnishing issue in copper busbar on tin plating.
In this process we tin plate on copper flat busbar and wrap with butter paper and send to customer.
After a few days opening packaging a few busbar observed tarnishing at both end but not middles.
So can you please suggest how to control this permanently?
- Jalgaon- Maharashtra-India
April 23, 2023
A. Hi Mayur
We appended your question to one of several threads here on the topic. No one can suggest what is not being done right until you tell us a bit about what you are doing, like acid or alkaline tin and the general process you're following.
But if tarnishing occurs only on the ends, not in the middle, and the ends received no special treatment, with no difference in the processing of the ends vs. the middle, I'd probably look at the packaging & shipment methods and investigate whether fretting corrosion during shipment is the issue. Good luck.
Luck & Regards,
Ted Mooney, P.E. RET
Striving to live Aloha
(Ted can offer longterm or instant help)
finishing.com - Pine Beach, New Jersey
⇩ Related postings, oldest first ⇩
Q. Hello,
We are having trouble with .0001" /.0003" tin plating over BE/Cu finger stock tarnishing within one week of shipping. It happens during shipping between Pennsylvania and Singapore. The tarnish is black and occurs in a mottled pattern. We have tried packing a desiccant in with the material, without success. Does anyone have any ideas as to the root cause of the tarnish?
- Allentown, Pennsylvania
2000
A. That is an extremely thin coating. Probably without a nickel barrier underneath it. Copper is very probably migrating thru the tin as an alloy and as pure copper. There have to be pores in a 1/10 thousandth thick tin coating.
James Watts- Navarre, Florida
A. Matthew:
I agree with Jim: the copper will alloy with all of the tin pretty quickly at that thickness unless you have a barrier like nickel. This will occur faster as the temperature is increased. I don't have charts at my fingertips right now, but a week at 90 to 100 &F might be enough.
That said, I am not sure that the resultant appearance from alloying or exposed copper would be a black color. The black color sounds more like some type of corrosion of the tin. Moisture could be the problem, some sort of chemical contamination, possibly from packaging, could also be a factor. You probably will need to do some analysis to figure out for sure what the mechanism of blackening is, then start looking for a root cause.
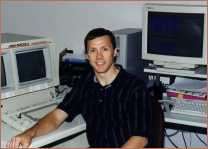
Larry Hanke
Minneapolis, Minnesota
I had also thought about the "black", and assumed it was probably something like a copper sulfide. Larry is very probably correct, you have another problem as well as the thin coat.
James Watts- Navarre, Florida
![]() |
A. Is the tin solution and acid tin? Especially with brighteners. If so you may need to add a neutral rinse after plating to kill the acidity and brighteners. Phil Pace- Tulsa, Oklahoma A. Blackening of tin deposits is normal unless you do some post treatment like chromate or dipping the parts in an alkaline solution, about 30 g/l NaOH at 30 °C. ![]() ![]() Sara Michaeli Tel-Aviv-Yafo, Israel |
Q. We are doing a Cu flash prior to the tin plating. After looking at a cross section of the corroded parts we can see the corrosion occurs on the top layer. We are doing an alkali dip after plating, potash specifically.
We tried to do a clear chromate conversion over the parts, but they performed poorly in the salt spray booth. The chromate line is normally used for zinc plating. Is there anything special for chromating over tin? Matt Evans
- Delaware Water Gap, Pennsylvania
2000
A. Matthew, acid tin is very prone to tarnishing unless it is totally free of plating residue and is dried quickly. You may want to try a product we use from Enthone OMI called TB-RA. We've found it to be helpful in neutralizing the leftover film. We use it on all three types, sulphate, msa and fluoborate. The only drawback is a little more drying stains if you don't remove the water quickly. Tom Salvino is the Enthone rep in your area I believe. Good Luck!
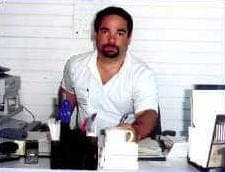
Jim Conner
Mabank, Texas USA
A. Tin fretting corrosion can also be a culprit if the parts are shipped in bulk. Vibration occurring during shipping can cause the parts to rub against each other (also called 'micromotion'). The rubbing causes tin displacement and subsequent tin oxidation (dark spots or mottling).
Bill McDade- Glendale, Arizona
February 2, 2009
Q. Matt,
We have been struggling with a similar issue. We have tried several different plating vendors and always get the black/brown tarnish on the plating over time. We have even tried plastic lining the shipping box and use desiccant. We are plating per ASTM B545 Class B (approx. 0.0002 to 0.0005" thick)
Did you find a solution to this problem?
- Avon Lake, Ohio
April 6, 2009
Tarnishing problem on Tin Plated wire"
Q. I am doing Tin plating. I need a procedure for protecting tarnishing of Tin plating. Please let me know. My tin plating process(post-treatment) Tin plating - rinsing(2) - dipping in a solution Na3PO4 - rinsing(2) - skin pass - dipping in a solution stearic acid ⇦ on eBay or Amazon [affil link] - drying - coil
HyunHee Kim- Korea
2001
Q. I have the same problem and am interested in a remedy. We use the same process but on small cast iron disks we do not use the stearic acid ⇦ on eBay or Amazon [affil link] .
Jack ShwallerMorgan AM & T - Houston Texas
2003
Q. We are into reel to reel plating of stamped parts; of late we are facing Black marks in MSA Matte Tin plated parts with an undercoat of Nickel. This appears over a period of time and in areas where the Tin plating is damaged (scratches).
The Tin plating thickness is 2 - 4 micrometers. It is prevalent on Brass base material predominantly. Please let us know what could be the possible causes. Thanks in advance.
Vijayakumar Balasubramanian- Bangalore, India
September 19, 2013
A. I suspect that your nickel coat is not thick enough to keep the copper in the parent material from migrating up and alloying with the tin.
James Watts- Navarre, Florida
Blackening of tinned copper strands in rubber cable
Q. Tinned copper strands inside the cable insulation turns black after curing in high humid and high temperature chamber.
But this does not always happen. Sometimes only a few strands turn to black colour.
Unable to understand the reasons for the same.
- Alwar, India
July 4, 2016
A. Hi Srinivasa. The insulation is rubber? Then I would expect the consequent sulfur ⇦ on eBay or Amazon [affil link] to cause blackening, especially if the tin plating is thin or inconsistent. What exactly do you mean by tinned copper: the whole wire is electroplated with tin (what thickness?), the whole wire is hot-dipped in tin, or only the ends of the wire are hot dipped? Thanks.
Regards,
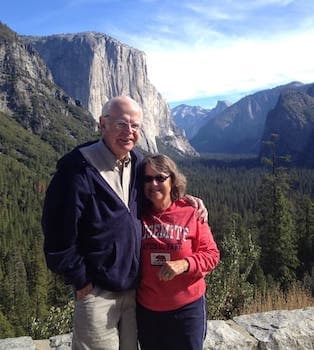
Ted Mooney, P.E. RET
Striving to live Aloha
(Ted can offer longterm or instant help)
finishing.com - Pine Beach, New Jersey
Q. Thanks Mr.Ted,
Tinned copper is hot dip tinned strands of the wire. And we do not use sulfur in rubber
- ALWAR, RAJASTAN, India
A. Hi. It would seem that some of the strands are not reliably tinned, as un-tinned copper will turn black in such circumstances.
Regards,
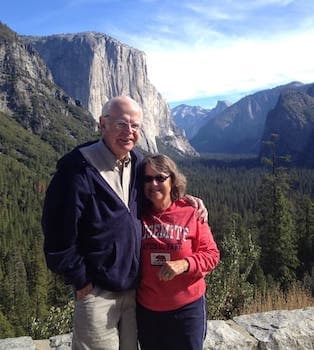
Ted Mooney, P.E. RET
Striving to live Aloha
(Ted can offer longterm or instant help)
finishing.com - Pine Beach, New Jersey
Q. In 132/11kV Trafo cable box, flexible corroded tinned copper link has been oxidized. Why does it happen? Please note: cable box is free from the rain and a heater is also provided in the cable box to eliminate the humidity.
Divan Mujipeer- Al Karama-Dubai- uae
July 20, 2016
Q. We are getting parts of switch terminal with tin plated over the brass. A slight copper flash is being done over the brass before tin plating. But around 20% of terminals getting rejected due to blackish / grey in colour patches. What needs to be done to eradicate this problem. thanks
radhakrrishnan sqa manager - India
October 17, 2016
A. Hi Radhakrrishnan,
If tin discoloration happen only after prolong storage then you may apply anti-tarnish after tin plating and before final rinse to protect tin deposit from tarnish during transportation / storage.
Regards,
David
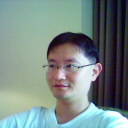
David Shiu
- Singapore

this text gets replaced with bannerText
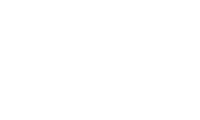
Q, A, or Comment on THIS thread -or- Start a NEW Thread