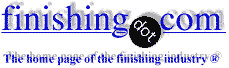
-----
Tantalum Wet Etching for Photolithography
Dear Sir ; How do you do? My name is Sung Jei Hong. Now I am looking for etching solution for tantalum. I work for tantalum thin film deposition on glass, photolithography on it and selective etching of Ta. My problem is that photoresist patterns are attacked by etching solution during Ta etching. (The etchant is composed of 20% HF, 40% HNO3 and 40% D.I. water. The etching temperature is room temperature.) I want the etching solution that does not attack the photoresist and Ta under the PR. Also, I hope it can be used under room temperature. Would you please recommend the appropriate etching solution to me as soon as possible? Sincerely yours Sung Jei Hong Senior Researcher KETI
Sung Jei HongKyungGi-Do, 451-860, Korea
2000
The etchant you mention is the standard one used in published texts. How about using gold as the resist, then lapping the gold back down to the Ta? Regards, Tom
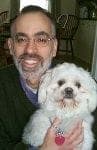

Tom Pullizzi
Falls Township, Pennsylvania
2000
2001
Dear Sir,
I am looking for etching solution for tantalum and Copper. I work for Copper electromigration test.
Cu film(5000 A) deposition on Ta glue layer(500A), photolithography on it and etching of Cu and Ta respectively.
I usually use etching solution composed of 25% CH3COOH, 25%H2O2, and 50% DI water at room temperature.
My problem is that photoresist patterns are attacked by etching solution during Cu and Ta etching.
I want the etching solution that can prevent under etching. Also, I hope it can be used under room temperature. Would you please recommend the appropriate etching solution to me as soon as possible?
Sincerely yours,
- Arlington, Texas
Even though this is a pretty old question, I'll answer it in case you are still searching (or someone else is interested). I was doing a search for alternative Ta etchants myself.
Tantalum is most readily etched with a mixture of hydrofluoric acid and nitric acid. You are using too dilute of a mixture and this is the cause for the resist degradation. Resist is attacked by the nitric acid. You need to use a 1:1 mixture and leave out the water. This should etch the tantalum before the resist gets severely attacked. This works quite well but the HF would attack all kinds of things (like your glass substrate, and skin and bones, etc. so use extreme caution in handling this material).
The earlier suggestion by Tom Pullizzi of using a gold mask is a good one, although, most people may dislike the extra process step. Tantalum is etched by peroxide -- the same way it etches tungsten or titanium -- by forming its mineral acid, in this case tantalic acid. But this process is fastest done at high pH and elevated temperatures. A strong base speeds up the dissolution of the Ta2O6. I've seen formulations of 1N solutions of NaOH heated to 90C, then
5-10% peroxide is added right before the tantalum film is immersed. This of course would wreak havoc on your resist.
I am quite surprised by Jee Yong Kim's etchant of acetic acid
⇦ on
eBay
or
Amazon [affil link] with hydrogen peroxide. In this case, the acetic acid , being an low molecular weight polar solvent, would degrade the resist. (What's the acetic acid for? Complexing agent for the Cu and Ta? I know titanium can be etched with peroxide and EDTA. Perhaps stabilizing the tantalic acid? Hey, try EDTA and H2O2 for Ta!) Even for Cu, the rate may be slow. I have to give it a try.
If you have a dry etch system, even a simple low cost one, try using a fluorine containing gas, like SF6, with 10% oxygen. That should etch the Ta quite quickly.
- Austin, Texas USA
2002
Q, A, or Comment on THIS thread -or- Start a NEW Thread