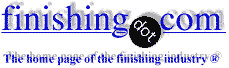
-----
HCl carryover problem in hot dip galvanizing
dear sir,
we are facing problem of acid carry over in flux bath in hot dip galvanizing due to improper water wash capacity, we can't increase our water wash capacity, currently we are using nylon cloth to control HCl but its not that much effective, is there any other way to remove acid before fluxing and after simple water wash
thank you
asst works manager - Nashik, Maharashtra, India
October 11, 2010
October 12, 2010
Sir:
Your real problem is the iron (Fe+2) that gets carried over from acid to rinse to flux. Recently available in the market-place there is an RO machine that takes out the iron from the rinse water and the concentrate is returned to the acid tank for evaporation losses. The purified water is returned to the rinse tank. The medium sized machine is the equivalent to a flowing rinse at 7 U.S. gallons/minute. This system is being used in the USA, Brazil, and China.
Regards,
Galvanizing Consultant - Hot Springs, South Dakota, USA
Thanks, Dr. Cook. Di units, evaporators, etc., have long been used on metal finishing rinse tanks to provide fresh water for rinsing while concentrating the contaminants for return to the previous tank. I am glad to hear from you that RO technology is being applied to the problem as well. Advantages and disadvantages of RO compared to the alternative technologies is an excellent topic, but this site tries to avoid discussions of individual brands and proprietaries.
Regards,
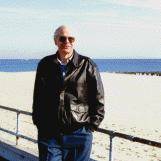
Ted Mooney, P.E.
Striving to live Aloha
(Ted can offer longterm or instant help)
finishing.com - Pine Beach, New Jersey
October 13, 2010
Rinsing in water is the most common way to remove HCl from steel before fluxing, but keeping the rinse clean is sometimes a problem. Many plants use two rinse tanks between acid and flux so that the 2nd rinse is cleaner than the first.
But its possible to reduce acid content in the rinse tank too, by the use of buffers, alkali or by consuming the acid in something like MgO.
Some places have the rinse tank continually being changed, but then for some that presents a problem for the disposal of that slightly acidic water.
Some plants have had a system of pumped sprays, such that the tanks contents are sprayed onto the work as it is being lowered into and hoisted out of the rinse tank. Other still have used agitated rinse tanks to get more effective rinsing.
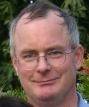
Geoff Crowley
Crithwood Ltd.
Westfield, Scotland, UK
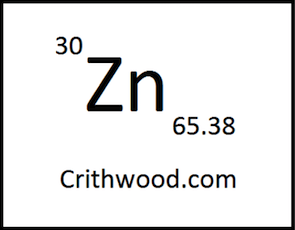
October 12, 2010
Q, A, or Comment on THIS thread -or- Start a NEW Thread