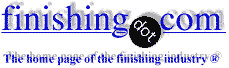
-----
High Phos Electroless Nickel on Stainless Steel 303 and AA6061
September 15, 2010
My company currently plates high P EN Ni on SUS303 pin and AA6061 housing separately, and then plunge those 2 parts together (tight fit). I am now working on a project that changes the process sequence that move the EN Plating to after plunging. I found that the adhesion on SUS303 pin is not passing tape test. Do experts provide suggestions for this issue? The process I am now using is
1. alkaline clean
2. Rinse x 2
3. micro-etch
4. Rinse x 2
5. desmut (HNO3+NH4NH2)
6. Rinse x 2
7. Zincate
8. Rinse x 3
9. Acid Rinse
10. rinse x 2
11. zincate
12. rinse
13. EN Ni
Thanks
- PRC
![]() |
Your process steps are for aluminum and are inadequate for any stainless steel since there was/is no activation step. In fact, the nitric acid step probably is acting as a passivation step. - Navarre, Florida September 15, 2010 You'll need to continue to plate them separately, Benny. Your pretreatment cycle looks fine for the aluminum, but the SS needs an entirely different pre-plate cycle. For the SS, you would do alaklaline clean, rinse, HCl activation, Wood's nickel strike, rinse, EN plate. ![]() Jon Barrows, MSF, EHSSC Kansas City September 15, 2010 |
We have discovered that the adhesion force is increased when the stainless steel pin is annealed before assembly and EN plating. 70% testing samples of annealed parts pass tape test, that is much higher than non-annealed parts (pass rate = 30%)
Do you know why the heat treatment improves the adhesion force?
Benny Hong
- PRC
September 28, 2010
Dear Benny Hong
Type 303 grade stainless steel is a free machining version of 304 grade via addition of sulfur and phosphorus. Also referred to as "A1" in accordance with ISO 3506. The typical chemical composition of 303 grade stainless steel is as follows: C: 0.15% max; Mn: 2%; Si: 1%; P: 0.20%; S: 0.15% min.; Cr: 17-19%; Ni: 8-10%. Type 303 grade stainless steel has good resistance to oxidation when intermittently exposed to temperature up to 760ļģ°. It also has good oxidation resistance in continuous service up to 870ļģ°. However, heat-treatment is not recommended as 303 grade stainless steel is sensitive to carbide precipitation with continuous use at 425-860ļģ°. The formation of chromium carbide will reduce the chrome availability for passive film formation and decrease the corrosion resistance.
During electroless nickel plating of stainless steels, a nickel strike using Wood's nickel bath is commonly used to improve the adhesion of the electroless nickel coating. The presence of passive film on stainless steel could influence the adhesion of the electroless nickel coating. On heat-treated 303 grade stainless steel, the depletion of chromium following chromium carbide precipitation will reduce the chrome availability for passive film formation. This may be one of the reasons for achieving 70% pass on tape test for adhesion.
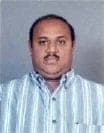
T.S.N. Sankara Narayanan
- Chennai, Tamilnadu, India
(ed.note: The good doctor offers a fascinating blog, "Advancement in Science" )
September 29, 2010
Q, A, or Comment on THIS thread -or- Start a NEW Thread