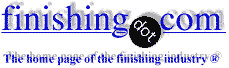
-----
Oil & Gas Equipment Shop Needs Painting Solution for In-House Application
We are a relatively small manufacturer of equipment components for the oil and gas industry. Most of the internal components are Nitrided but the outside of these parts, primarily stainless (316 and 304) have been painted for appearance sake. Occasionally we have had some units for client specific application chrome or nickel plated, and in these applications, the premium cost is covered by additional charge to the customer.
We had discussed black oxide process for the outside, but have read several articles pertaining to the loss of corrosive protection in stainless steel parts, and since these are primarily units for a corrosive atmosphere, that seems to be a non-solution.
Our current painting process is a rather unprofessional system of applying 2-part polyurethane paint to the assembled units with an air pressured paint gun in a small paint booth exhaust system. Units are "hung" on racks and left to dry/cure. A totally inefficient system to be sure. On some occasions we utilize aerosol pressured cans of paint for small applications.
We would like to go with an in-house system of coating not unlike the black oxide (such as Birchwood Technologies [a finishing.com supporting advertiser] BC-40E Tru Temp system) that will not affect the corrosive resistance of the stainless.
Any ideas or suggestions out there ladies and gentlemen?
Thank you!
Operations Manager for mfg. company - Tulsa, Oklahoma, USA
September 13, 2010
Hello, Charles. You'll need a black oxide that is specifically formulated to be applied on stainless steels. Unfortunately, that almost certainly means a higher temperature process and more costly equipment.

Jon Barrows, MSF, EHSSC
Kansas City
September 14, 2010
Black oxide is inexpensive, with limited corrosion resistance and will not aesthetically complement your nitrided part. Though slightly more expensive, the better solution could be to have a cured, thin coating applied via dip-spin; which will offer >500 hours of salt-spray resistance, while looking very good.
Craig Schindler- Fairburn, Georgia, United States
September 28, 2010
Q, A, or Comment on THIS thread -or- Start a NEW Thread