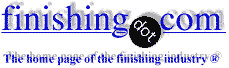
-----
Tank is rapidly deteriorating [Georgia]
Hello,
I am actually writing to see if someone can give me a scientific explanation as to why a tank was deteriorating.
The tank - 316 Stainless, containing 25% Nitric 2% sodium dichromate, heated to 140 degrees F.
The problem - the tank was deteriorating rapidly. No current, but we did find out that the tank was not grounded correctly. Once the ground was fixed it stopped (rod placed directly into the ground)
My first thought when this started happening, was that some moving parts in the tank were not stainless and a galvanic reaction was taking place but after replacing just about everything the reaction was still occurring until the ground was fixed.
Even though it has stopped I am curious as to exactly what was happening.
Thank-you,
Micheline Forth
finisher - Rincon, Georgia, USA
July 30, 2010
![]() |
Micheline, Kansas City, Missouri Hello Micheline. Did it fail at or adjacent to the welds, but nowhere else? That would be my guess. The heat generated during the welding of the tank is sufficient to cause the chromium and the carbon in the alloy to precipitate as a chromium carbide which leaves the heat effected zone (weld area) without any significant corrosion protection. The use of 316L instead of 316 reduces the amount of carbon available and leaves more alloyed chromium free to form corrosion resistant oxides instead of carbides. Pickling or mechanically polishing the welds after welding also helps to restore corrosion resistance in the welding zone. Instead of SS, I always recommend CPVC, PVC or PVC-lined tanks for Type II passivate solutions. Polypropylene is my recommended tank material for most of the passivate solutions that do not contain chromates. These materials avoid several potential problems. Good Luck. ![]() Jon Barrows, MSF, EHSSC Kansas City |
August 5, 2010
Hello,
Thank-you for the responses.
Ira,
Several heaters and probes were changed out due to corrosion.
Jon,
The corrosion was happening everywhere, but once the tank was correctly grounded the reaction immediately stopped. I am interested in knowing the science behind this.
Sincerely,
Micheline
finisher - Rincon, Georgia, USA
August 3, 2010
Did you consider the heater (especially if it is electric)?
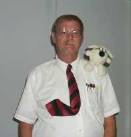
James Totter, CEF
- Tallahassee, Florida
Q, A, or Comment on THIS thread -or- Start a NEW Thread