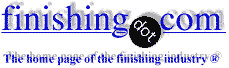
-----
Superfinishing Stainless Steel
ACRONYMS:
SUS = an acronym for stainless steel based on Japanese JIS standards.
Q. Hi how are you.
I'm Korean and live in Korea.
I am trying to make an super mirror SUS (8k or 10K)
At first I tried to make it using green wax and buff.
But it still make a scratch.
When I reflect the light I can see the scratch.
so I try to chemical mechanical polishing processing.
I don't know how nitric acid work to make a super mirror.
I think nitric acid is make a passivated.
When I saw chemical mechanical polishing processing in another factory they used nitric acid, oxidized steel and water.
It removed a scratch and made an over 8K surface.
How does it work?
Please teach me how can to make a super mirror without electrolytic polishing.
Thanks.
- seoul/ south korea
A. Hi Kim. You can buy #8/8K finished stainless steel if you wish. And there are dozens of youtube videos showing you how to do it yourself if you prefer, or where to buy machines if you want to do it in production.
But I think the thing that most people who are new to this don't realize is that it cannot be done in a single step, or even two or three steps. It takes four steps at best, and probably more.
Simply, you need to do a coarse grind until there are no scratches deeper or wider than the size of your grit; then you do it again with a finer grit and stop only when there are no scratches deeper or wider than that finer grit. Then you move to a finer grit and repeat, and a still finer grit and repeat. A trick that some people use is to do the coarse grind in one direction, the next step in the perpendicular direction, the third step back to the original direction, etc. -- the reason for this is that if at any point you see a scratch running perpendicular to the direction you're polishing, that step is not yet finished and you must not move on.
Luck & Regards,
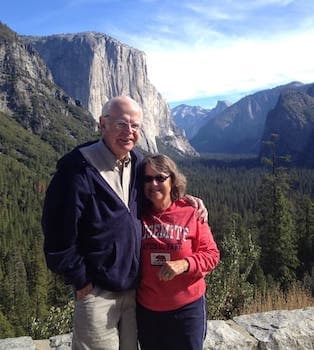
Ted Mooney, P.E. RET
Striving to live Aloha
(Ted is available for instant or longterm help)
finishing.com - Pine Beach, New Jersey
December 2021
December 2, 2021
Q. Really thanks to answer.
We have to make 8K STS from 2B STS on coil to coil machine.
When I finished polishing, I used 0.3 µm wax, but it makes a scratch.
I think buffing makes the scratch.
So I turn to chemical mechanical polishing processing from buffing, but I don't know how can I do chemical mechanical polishing.
I heard that it uses HNO3, Fe2O3, and water.
I want to change from HNO3 to citric acid -- is it possible?
... and can you teach me the process of chemical mechanical polishing?
Really thanks for your answer.
- seoul/ south korea
December 2021
Hi again. Sorry I am not familiar with that but we will leave your question on line and hope that a reader can help you,
Luck & Regards,
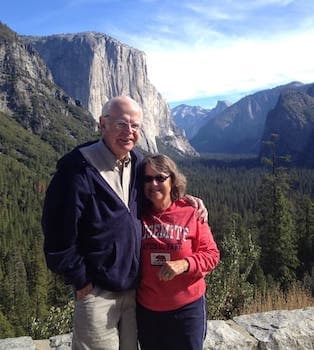
Ted Mooney, P.E. RET
Striving to live Aloha
(Ted is available for instant or longterm help)
finishing.com - Pine Beach, New Jersey
A. Maybe somebody can prove me wrong, but I really don't think it's possible to chemically etch your way to a smoother surface, i.e., with acid. Electropolishing, or acid with electric current, sure, because in that case it's the current doing the work and the acid is only there to carry the current. But acid on its own is going to remove material from the surface randomly, not selectively from the microscopic "peaks" as you would need to increase the smoothness. Sometimes acids are used as "brighteners" for metals, but in those cases you are not making a smooth, reflective surface, but rather an etched surface that scatters light more in the direction of the viewer. Sometimes etching makes the surface darker though, light is scattered more away from the viewer.
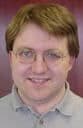
Ray Kremer
Stellar Solutions, Inc.

McHenry, Illinois
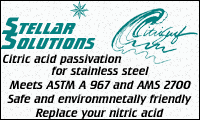
December 2, 2021
A. One very common reason for getting a scratch at late stages is that your cloth is contaminated. This is caused by a failure of cleanliness between stages and/or a failure of cleanliness in storage of the buffers/polishing cloths.
Between each stage of finishing, you must clean the surface of the sample well. Pay particular attention to small holes and crevices which tend to retain particles. Your working area, workholders, etc. should also be clean. Your cloth used for final polishing must only be used for that 0.3 µm media and be stored in a clean manner. If it is contaminated, just throw it out and replace it.
If you transfer any grit from earlier stages, you will very easily scratch your sample. Patience and cleanliness is the key.
- Melbourne, Australia
March 17, 2022
Q. Dear Sirs / Gentlemen,
We are scared of using superfinishing stones which give mirror like finish on the bearing races as some of our suppliers has threatened us as superfinishing stones contains lead which is poisonous (Dangerous) to health and use of lead is banned in American countries is that so?
We are really looking for such stones which gives mirror stones, we need some guidance from you as to convince our operators on the health grounds.
1)What really contributes to the mirror finish during superfinishing ?
2)If it is lead how dangerous is the lead to the human beings ?
3)If at all it is the lead or barium (some says ) to what percent it will be there in the stone.
4)Does it have any reaction with the coolant used by us, i.e., Honilo 481 of Castrol?
5)Does lead put directly in to the stones if so does it makes fumes at the temperature generated at the point of contact of the bearing races and the stones.
6) As it melts at very low temperature does the manufacturers give us the certificate that the process involved in manufacturing these stones,along with the temperature of sintering which is approved by the international standards with respect to pollution norms set by the international quality standards?
Thanking you and looking forward to receive your reply at the earliest
Yours faithfully,
K.Badarinatha- Bnagalore, Karnataka, India
A. It sounds as if someone is trying to give you mis-information. Wet polishing is normally referred to as burnishing media. This can be either steel or porcelain or an equally hard fine particle material which does not breakdown during processing. Therefore, this media works primarily via lapping and weight. Any material removal is caused by fracturing or fatigue of the materials being worked. Whoever told you lead is involved is incorrect. Normal composition of porcelain media is around 71% silicon oxide, 22% aluminum oxide, 4% potassium oxide and 3% other materials. No lead! Basically porcelain is inert and behaves like a glass container meaning chemicals will not normally effect this media even in a concentrated liquid. Any fumes encountered would be from a liquid additive or chemical accelerator used to speed up processing. This maybe what you are referring too. This involves a whole lot more than can be explained here.

AF Kenton
retired business owner - Hatboro, Pennsylvania
September 7, 2008
Q. Hi,
I am Kunal Makwana from India, and we have a Cold-Rolling Mill. Our Rolls for the Mill are made up off Hardened Alloy Steel (K-310), and have a surface hardness of 58 HRc.
The Problem : I would like to have a Mirror-Finish on the surface of the Roll. Since the Rolls is more than 2000 pounds in weight, there is no job-worker/consultant for providing me a Finish as desired on the Roll.
Process till now which we have implemented : Since the Roll is heavy, and there are no one who could do an electropolish or so on the Roll to give it a mirror-finish, we have to get the finish on the Roll mechanically. Firstly we have done a rough polishing with an 80grit NORTON Abrasive. Then we super-finish the Roll with 600 & 800 grit sulfur-based honing stones. Then we again super-finish the Roll with 1000 & 1200 grit Graphite based super-finishing stones. Then we apply a paste of Boron Carbide on the surface with the help of the Super-Finishing Machine. And at last, we polish it with a Polishing paste (NAGEL, Germany) again with the super-finishing machine.
Result : The surface roughness comes down drastically (which is good for us, as we need a very smooth surface), but not as desired. To get a mirror finish on the roll one needs to have a surface roughness average of 0.5 microinches Ra, which is still not happening after using the above method.
Your Help Required : If anyone could suggest us any other alternative method (or) any changes which would help us get the desired finish on the Roll. If any parameters of the Roll needs to be changed (like surface hardness), or if any other Alloyed Roll itself needs to be made? The Roll is used in a skin-pass mill.
Thank you in Advance.
Regards
product designer - Gujarat, India
July 22, 2010
Q. Need some expert advise on ways to achieve Ry < 0.4 on Stainless Steel 303 or 304 shafts for huge volume orders.
I had tried numerous method to achieve Ry < 0.4..
1. Centerless grinding - Ry > 1.0
2. Electropolish - Ry > 0.6
3. Barrel Tumbling with ceramic beads - Ry > 0.6
Sadly to admit, but I'm are lost in this situation.
Hope a few of the senior experts here can drop an apple on my head...
Thank you in advance.
Sincerely,
R&D - Perth, Australia
A. Centerless grind followed by polishing with diamond paste on balsa wood.
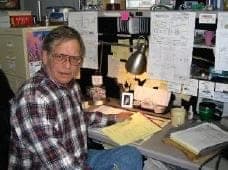
Jeffrey Holmes, CEF
Spartanburg, South Carolina
July 27, 2010
A. This is a very stringent requirement that will take some effort to meet. My first piece of advice is that it will take more than one process step to attain Ry < 0.4, as you have already discovered, so be prepared for that. Second, Type 303 SS will not polish well, regardless if it is by electropolishing or conventional finishing techniques, so you may want to eliminate that from consideration and stick to Type 304.
With such a low surface roughness specification I am assuming that the shaft also requires excellent straightness and concentricity, with low runout. If so, you will likely need centerless grinding to start with, unless this shaft is relatively short. Based on this assumption, I would look into one of the following processes to improve the as-ground surface:
1. electropolishing
2. roller burnishing
3. automatic shaft polishing (through-feed process, sometimes called superfinishing)
4. media tumbling, possibly multiple steps, and/or Isotropic Super Finishing
Automotive component supplier - Michigan, USA
July 29, 2010
A. Before attempting to recommend something please tell us what is the shape or geometry of the parts and what do you mean by huge volumes. G. Marrufo-Monterrey-Mexico
Guillermo MarrufoMonterrey, NL, Mexico
July 30, 2010
Q, A, or Comment on THIS thread -or- Start a NEW Thread