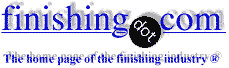
-----
Hydrogen embrittlement of high carbon steel after tin plating

this text gets replaced with bannerText
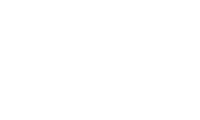
High strength steel is subject to a problem called hydrogen embrittlement which makes it prone to snapping, cracking or fracturing under light loads.
In the plating process the work is sometimes cathodically cleaned which will generate hydrogen at the work surface; it is usually acid dipped -- and acids function by releasing hydrogen at the surface; the work is made cathodic during plating, which again releases hydrogen at the work surface because not all of the applied current always causes plating, but to varying degrees it hydrolyses water into hydrogen & oxygen. Hydrogen from any of these sources migrates into the grain structure of the steel, weakening it.
The general solution is to minimize these sources of hydrogen at the work surface, and to "bake" the parts immediately after plating to release the hydrogen before it does permanent damage.
This is only a very brief intro ... some steels are too high strength to electroplate, mechanical plating is sometimes used instead of electroplating, blasting is sometimes used to eliminate acid dipping, some steels must be baked after pretreatment but before plating, and again after plating.
Q. I am William,
I have been facing a brittleness problem while electroplating a fishing hook. We heat treat and temper a formed high carbon steel wire. While bending it, it was strong and bent okay. We are happy up to this. After we are going to electroplating process we cannot achieve the same ductility of Heat treatment process. It was breaking. It was affected by hydrogen embrittlement.
Baking the hooks is also not working out because tin plating is removed while baking. I use acid tin. I face this problem for 2 years. Someone please help me. How to make good high carbon steel fishing hook?
William hemilton- India, Tamilnadu
January 13, 2022
A. Hi William. We appended your inquiry to a thread which offers good thoughts on this subject, ranging from plating with different material to hydrogen de-embrittlement baking not being the cause of your adhesion problems. But I think the answer may lie not in the tin-plating step per se but in the pretreatment for plating: cathodic electroplating and/or acid dipping. Can you blast a few parts or manually scrub them with pumice as your pretreatment and then directly tin plate them at the lowest possible current density without any further cleaning or activation and see if hydrogen embrittlement is still a problem or not? Then bake some of them and see if adhesion is a problem or not.
Luck & Regards,
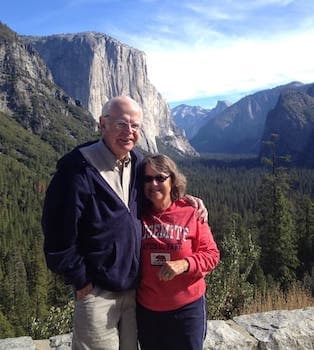
Ted Mooney, P.E. RET
Striving to live Aloha
(Ted can offer longterm or instant help)
finishing.com - Pine Beach, New Jersey
January 2022
⇩ Related postings, oldest first ⇩
Q. Hi, we are trying to get wire products to be used in salt water made from High carbon steel & tin plated, with a copper undercoat and the problem we are facing is hydrogen embrittlement after the process despite a few suggesting that we dip the same in boiling hot water for few minutes after each operation during the plating process, which though made some difference but not the desired result and even baking them made the plating peal off after they were bent. The plating needs to be ductile as the hooks are reused many times and mostly re-bent to shape using a tool.
Can anyone suggest a method to get rid of this problem ? Also, I would be glad if someone could suggest a much better plating (preferably alloy plating with tin) that would be fulfill all these criteria. Thanks!
manufacturer of wire products - Coimbatore, Tamilnadu, India
July 16, 2010
![]() |
A. I would switch to monel wire or a suitable wire for your use. - Navarre, Florida July 16, 2010
"Fundamentals of Hydrogen Embrittlement"
July 19, 2010by Michihiko Nagumo ![]() on eBay or Amazon or AbeBooks (affil link) Dear Vikram Krishnan. - Salem, TamilNadu, India Vikram, Aerospace - Yeovil, Somerset, UK July 19, 2010 |
Q. We are Tin plating C75 Spring Steel components. In a recent lot, the parts after tin plating, failed to qualify the bend test (part should not crack). To cross verify the input condition of the component, we have conducted bend test before plating and the component qualified in the test.
We suspect some abnormalities in the tin plating process which makes our component brittle.
Appreciate if some one could share your expertise in the understanding the problem
Vignesh
Employee - Tamilnadu, India
June 3, 2015
A. Hi Vignesh,
Did the crack happen on tin deposit only or also steel? Did your tin plating process involve cathodic degreasing which generates hydrogen gas onto steel part that might cause hydrogen embrittlement?
Regards,
David
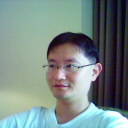
David Shiu
- Singapore
June 6, 2015
July 20, 2015
Q. Hello David,
The crack is noticed on steel.
Our tin plating involves hot De-greasing (Metal Cleaner mixed with water and maintained at temperature 55-65 °C duration 30 minutes) followed by cold water rinsing / Tin plating / Cold water rinsing.
Are there any possibilities of embrittlement in this case?
- Tamilnadu, India
A. Hi Vignesh. There was no acid dip at any point, nor any cathodic cleaning or other source of hydrogen in the process? If so, then the tin plating did cause the hydrogen embrittlement, and it's probably wishful thinking to hope that it was a strange contaminant in the bath that caused it rather than the essential cathodic process of electroplating.
Still, as the current density increases, efficiency declines and hydrogen evolution increases, eventually resulting in "burning" -- so I suppose it's possible that you tried to plate those clips too fast and it accentuated the hydrogen embrittlement issue beyond its normal effect. Good luck!
Regards,
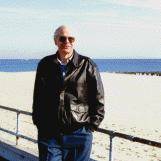
Ted Mooney, P.E.
Striving to live Aloha
(Ted can offer longterm or instant help)
finishing.com - Pine Beach, New Jersey
Q, A, or Comment on THIS thread -or- Start a NEW Thread