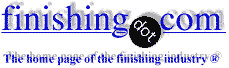
-----
Minimal build thickness brown anti corrosion coating on steel
I need to try an duplicate a minimal build thickness coating that is dark brown in color. This has a similar appearance to milling machine face cutters from Sandvik, Kennametal, etc. It has a minimal build thickness because it is used on a bearing surface of a shaft. My first inclination is to go to a black oxide or phosphate, but it will be in a non-oily environment and I can't afford surface rust for several years. I'm thinking that the milling machine cutters may be proprietary CVD or PVD coatings, but if there are some suggestions of what the coating might be, it would be very helpful.
Matt SlatterEngineer - South Jordan, Utah, USA
July 7, 2010
July 9, 2010
Hi, Matt. I would suspect that the coatings on cutters are all PVD hard coatings. They will be expensive to apply to a larger item like a shaft. But I think the main problem will probably be that they are not sufficiently corrosion resistant because of their thinness. When decorative PVD coatings are put on parts made of steel or other non corrosion resistant materials, there is usually a layer of some corrosion resistant electroplating (like nickel) beneath them.
Regards,
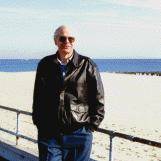
Ted Mooney, P.E.
Striving to live Aloha
(Ted can offer longterm or instant help)
finishing.com - Pine Beach, New Jersey
July 13, 2010
PVD ( physical vapour deposition) is a technique of depositing coatings and there are several variations of this. Generally one deposits metals, oxides, nitrides, carbides, alloys and so on. The applications are varied hard and wear resistant coatings for cutting tools, low friction coatings for sliding surfaces, decorative coatings, erosion and corrosion resistance coatings, etc. Coating thickness can vary from few nanometers to several microns and in some case could be few tens of microns. PVD coatings are generally used where electroplating techniques are not possible though people talk of replacing electroplating techniques by PVD for environmental considerations. Cost comparison would therefore be difficult.
Though hard coatings coatings like TiN, TiAlN etc are commonly used for cutting tools, a PVD coating has to be designed for a particular application.
H.R. Prabhakara - ConsultantBangalore Plasmatek - Bangalore Karnataka India
Matt, the best solution for the journal, bearing surface would be to undersize (0.014" on the O.D.) the target surfaces, then over-build with a corrosion resistant, HVOF applied hard-face material (i.e. tungsten) and diamond grind back to the finish diameter. The surface rust will never re-appear.
Craig Schindler- Fairburn, Georgia, United States
September 28, 2010
Q, A, or Comment on THIS thread -or- Start a NEW Thread