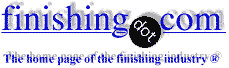
-----
Plaforization - What is it really?
Q. I am in the automotive industry in which we powder coat coil springs with customer specifications that go beyond just salt spray testing. If we can eliminate waste products and lower costs produced by the zinc phosphate pretreatment this sounds like the solution. I recently have been introduced to Plaforization and I am also curious as to the real substrate coating applied. Is this another form of Iron Phosphate coating and if so what are the detrimental effects that are potentially associated with this coating?
What are the mechanisms for the powder adhesion?
How does this substrate compare to Zinc Phosphate substrate?
Any feedback on this would be appreciated.
Wayne
industrialist - Hopkinsville, Kentucky, USA
July 7, 2010
A. My understanding is that Plaforization is an iron phosphate coating that needs no rinsing and which manages to convert typical oils and greases on the parts, like cutting oil and fingerprints, into a sort of organic sealer so that oil removal is not necessary either. They claim that as long as the quantity of oil and grease is not excessive, the process is single-step and generates no waste products except filter cartridges which collect the solid particles of dirt.
While we can't compare or evaluate proprietary products here for several reasons, including the anonymity of the internet (it pulls shills out of the woodwork who often disguise themselves as satisfied customers), certainly the process basically works. There are also other brands of non-phosphate pretreatments, dried-in-place pretreatments, etc., as well.
While these reduced waste processes are a substitute for iron phosphating, I think most people will acknowledge the superiority of zinc phosphate over iron phosphate. Although zinc phosphating has an environmental and cost impact, unless a process the alternative is proven to last 15+ years in severe outdoor exposure like zinc phosphating does, I think it is foolish to judge a pretreatment process by the waste products of the pretreatment step itself, rather than by the waste of repeatedly re-mining, re-smelting, re-rolling, re-fabricating, re-pretreating, re-painting, re-packaging, re-selling, and re-landfilling replacements.
I don't know whether the deluge of cheap Chinese outdoor furniture and accessories that barely lasts 2 years is the result of pressure to abandon zinc phosphating, or is just coincidental, but it's an environmental and sustainability travesty. Additional comments are welcome so long as they speak of concepts and technical issues rather than claims that one secret proprietary process is better in some way than some other secret proprietary process :-)
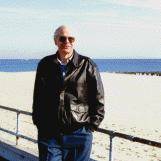
Ted Mooney, P.E.
Striving to live Aloha
(Ted can offer longterm or instant help)
finishing.com - Pine Beach, New Jersey
July 9, 2010
Q, A, or Comment on THIS thread -or- Start a NEW Thread