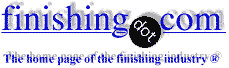
-----
Acid Tin Plating - is pretreatment of Nickel underlayer necessary?
July 7, 2010
We are a consumer electronics OEM. We're having persistent solderability problems with a surface-mount ferrite chip inductor. The metallization is pure matte Sn (3-5 um) with Ni underplate (1-2 um) over Cu. The thicknesses are all within spec, but wetting balance testing shows slow wetting times (usually suggests surface oxides) and declining wetting force (suggests contamination or issues with the Ni underlayer).
Based on data they provided, I surmise they use either methane-sulfonic acid or stannous sulphate for the tin layer and sulfamate for the Ni layer. As we prepare to audit their plating operations, I am trying to determine what parameters or variables might be contributing to these solderability problems.
Some basic questions:
1. Is porosity of the Sn layer a concern if the min thickness of 3 µm is achieved?
2. How is porosity measured and controlled? ASTM tests I have seen appear targeted for Sn over steel substrates. Is solderability testing the best measure of Sn layer integrity?
3. I know that organics are co-deposited in Sn layers and should be
<0.2 wt % for matte Sn. How do platers control this to prevent excess organic content in the Sn layer? Would you expect a good plater to have the analytic capability on-site to measure this?
4. Is pre-treatment of the Ni layer necessary? I have read that SnCl is sometimes used ahead of the Sn plating chemistry - is this common? Essential?
5. Any red flags to be aware of with the sulfamate Ni process?
Thanks in advance for any advice or suggestions. I greatly appreciate this forum and the tremendous contributions I find on it!
OEM Component Engineer - Framingham, Massachusetts, USA
July 21, 2010
Dear Todd,
What you ask, needs a much more extended answer than any volunteer here will give. I recommend you to ask a consultant (see their adds on MF), I will help you a bit:
Some basic questions:
1. Is porosity of the Sn layer a concern if the min thickness of 3 µm is achieved?
Yes, Sn directly on Ni can be porous even at 3u if the plating company .
2. How is porosity measured and controlled? ASTM tests I have seen appear targeted for Sn over steel substrates. Is solderability testing the best measure of Sn layer integrity?
Finally the solderability test is the best, but you should consider the way you will do these tests, using wetting balance after dry heat test 16H - 155ÄC - air and steam ageing or high RH/RT-tests will be a good predictor. If you can agree this with your supplier, that would be a good start.
3. I know that organics are co-deposited in Sn layers and should be <0.2 wt % for matte Sn. How do platers control this to prevent excess organic content in the Sn layer? Would you expect a good plater to have the analytic capability on-site to measure this?
This is a nasty question, a very expensive instrumental analyses exist but is ample used and is complicated (GC). Normally a company should make regular activated carbon treatments to the electrolyte, in order to remove the organic contaminants which stem from breakdown products of the needed organics in the electrolyte.
4. Is pre-treatment of the Ni layer necessary? I have read that SnCl is sometimes used ahead of the Sn plating chemistry - is this common? -->(No) Essential? -->(No)
Directly after plating a fresh Nickel-layer, it will be active, but the nickel will quickly passivate. If you have your question marks here, co-operate with your supplier to see where your problem is. An acid predip before the Sn-plating is quite common. Nickel containing organics is more prone to passivation as an organics free Nickel. The influences in your own soldering process (Flux-type, soldering time, temperature, profile, etc.) are tremendous too. The Sn layer is at the low boundary with the 3u.
5. Any red flags to be aware of with the sulfamate Ni process?
Many...to name a few: [Ni],[H3BO3] [Cl], pH, T, A, V, Metallic contaminations, organics, frequency of carbon treatments analysed/done/recorded? Flow mechanics....to name a few.
I strongly recommend you to include a knowledgeable person from one of the bigger suppliers for these types of chemistry. It will prevent you from pinpointing around, making your supplier mad and in the end not having solved your problem(s). Of the utmost importance is a good co-operation between you and your supplier, in an open atmosphere, without immediately laying claims on the table or asking for rigid controls on items which never proved to be a cause for the problem. Maybe you should think about a screening DOE in which you include parameters from their process which can be of influence. If, during the audit you loose all confidence in your supplier, it will be a different story.
Best regards,
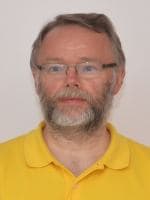
Harry van der Zanden
consultant - Tilburg, Netherlands
July 27, 2010
The nickel underlayer is used to prevent a layer of brittle copper-tin intermetallic compound from forming. This could flake off in extreme cases.
High operating temperatures will accelerate the formation of this layer if there is no nickel barrier layer.
consultant - Cleveland Heights, Ohio
Hary,
Thank you so much for the thoughtful and detailed reply. As a follow-up, I wanted to tell you that this information has proven very helpful. We worked closely with the supplier and have solved this problem.
Thanks again to you and to everyone who makes this forum an excellent resource!
- Framingham, Massachusetts, USA
August 26, 2010
Q, A, or Comment on THIS thread -or- Start a NEW Thread