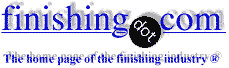
-----
When to Choose Anodize, Chromate, or (Maybe) No Finish for Aluminum
June 25, 2010
Hello folks,
We design and assemble hand held products that include machined Aluminum parts. Usually these parts are 6061 but one portion in particular is 2024 (that part needs 2024's Copper content and must stay 2024). Our hand held products are normally used indoors or outdoors with exposure to sunshine and occasionally a light drizzle
(we are not expecting them to stay wet or be used in heavy rain, etc.) We do not expect them to be subjected to salt water spray
(except very rarely). The 2024 part is a part with external faces
(that encounter the environment) and internal pockets (fairly well-sealed from dust and water from outside). This 2024 portion is formed by two halves (both nearly mirror images of each other) that are screwed together with 18-8 screws to form a shell.
Now, I was shown-the-ropes doing Mechanical Design that when I design a part from Aluminum, I should generally call out the good 'ol MIL-A-8625 spec. on the drawing (especially when stainless steel screws would be used to fasten). I was also taught about using MIL-DTL-5541 to Chromate parts when electrical conductivity (EMI shielding contact) is important and where abrasion resistance is not critical.
So, with this 2024 part: I am currently specifying Anodize and masking of the surfaces of the two halves that come together when the screws are tightened. I am also specifying that those masked surfaces then get the Chromate finish after Anodizing so we have a nice EMI shield created. The parts work fine now.
My question is the following. I am considering leaving-off the Chromate since:
1) The surfaces that get that finish are not open to the environment.
2) There is a very minimum of expected salt water or other "nasty" environmental things this part will encounter.
3) As to the EMI conductivity issue, I have found old (few years) pieces of 6061 stock (never Anodized) where if I probe the surface, they still conduct without having to dig through the surface. I can't say if that's true for 2024 but I'd guess it would be (since old Copper behaves the same way).
How can I decide whether to bother with the Chromate finish? Could I just specify masked Anodizing?
One person here is concerned that unfinished Aluminum pieces held together will eventually get stuck together.
I'll appreciate any thoughts you experts have. Thanks!
Best,
Eric
Mechanical Engineer - Woburn, Massachusetts, U.S.A.
July 26, 2010
Eric
Most anodizers will chromate the part first to ensure a sound surface to apply a mask. If you require the surface to be free from anodize, chromate optional, another choice would be to machine the anodize off.
If corrosion of the bare aluminum is a concern, apply the chromate.
- Colorado Springs, Colorado
Q, A, or Comment on THIS thread -or- Start a NEW Thread