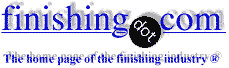
-----
Problems with plating 17-4 inner diameter
June 21, 2010
We are having trouble plating the inner diameter of a 17-4PH barrel. First, I want to say that we successfully plate 17-4PH steel components all the time without problems but I recently had 4 parts to come across my desk that have just thrown me for a loop.
The parts are made of 17-4PH steel (I checked this with an XRF material analyzer).
We are plating in accordance with MIL spec QQ-C-320.
The parts were honed and chemically stripped of chrome in sodium hydroxide solution.
They were grit blasted and the threaded areas and non-chrome plated areas were masked with aluminum tape.
At the end of the plating process the current was reversed for 3 minutes.
After finish grind these were rejected due to poor quality (pitting and flaking at the bottom) and were therefore stripped and re-plated again as above.
This time when they were removed from the chrome tank the aluminum tape had dissolved completely and the part was etched around the threads and lead in chamfer.
The entire bore was left very rough, no chrome and lots of pitting in the base metal.
Even more curious is that these parts have a side port on the outside that appears to have been previosly welded to the barrel, most likely from the manufacturer. The ID where the side port is is discolored and rough.
There is some yellowish color left around the threads (maybe sulfamate nickel from a previous rework?)
Was this caused by the reverse current at the end of the process? Is this normally done on 17-4 steels?
Is it because we did not do a nickel strike before chrome plating
(even though the mil spec allows it)?
I am baffled. Any input would be appreciated.
ps. I have photos of the part if that would help.
employee - Oxford, Alabama
June 22, 2010
Reverse at the end of chrome plating is normally only done when you want to make the natural cracks in chrome larger to hold oil as in large diesel engine piston inserts.
I suspect that the parts went thru the caustic clean with the Al tape still on and it was nearly destroyed. The next probability is that it was never put back on or it was put on over the sludge of the old tame. It does not react grossly differently because of a rework IF the rework is done exactly the same way.
Your header says that you have a problem with ID bores. Are you using ID anodes, and if so, what spacing?
Part sizes would help to give a better answer.
- Navarre, Florida
Q, A, or Comment on THIS thread -or- Start a NEW Thread