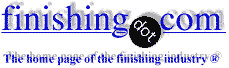
-----
Alkaline Zinc Nickel plating process
Kindly suggest us why we have to go for Zinc Nickel plating process for steel and Brass.
If so what type of plating bath is recommended Acidic or Alkaline bath. If alkaline bath any cyanide formation will be there during plating.
Thanking you,
eagerly waiting your reply at the earliest.
Manager Plating & Painting Shop - Bangalore, Karnataka, India
June 10, 2010
The only thing that you HAVE to do is whatever the customer asks for.
Every type of plating solution has at least one reason why you should use it. They all have at least 1 reason why you might not want to use it.
There are hundreds of plating books on the market. Buy some used ones and read a lot.
- Navarre, Florida
June 11, 2010
![]() |
Dear Chandramani, - Bangalore, KARNATAKA, India Hi, ![]() Praveen Kumar plating process supplier Mumbai, India |
June 29, 2010
Dear Chandramani,
A balanced Zinc-Nickel alloy plating deposit provides an excellent level of corrosion protection to components specially under difficult thermal conditions. Automobile Engine components under bonnet is a common example.
Zinc-Nickel deposit, during corrosion produces less volume of white rust powder like that of cadmium.So this can be considered as an alternative to cadmium plating is specific areas.
I will reproduce a portion of my own writing
Quote
"As your basic concern is to have a cyanide free environmentally friendly plating process, you have asked me to explore about the possibilities of replacing Cadmium plating with cyanide free zinc plating.
Cadmium plating have been at the core of military specs for years world wide, its replacement in such a critical area till recently(5 years) had no alternative. U.S military by virtue of concern over using poisonous cyanide and cadmium directed their research to this direction. Now considerable portion of their specs are met with alkaline cyanide free Zinc- Nickel plating process.
Cadmium plating gives good corrosion resistance with low friction, lubricity and solderabilty.It has the advantage of making a barrier layer in between two different metals.
Thus preferred in aerospace industries where aluminum is most in use. During corrosion, the volume of Zinc hydroxide generated in the size as volume is much more than that of cadmium produces and is weaker.Thus cadmium plating cannot be replaced with mere Zinc plating for military applications"
Unquote
Regards
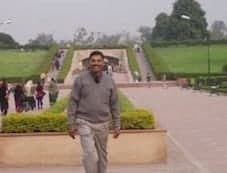
T.K. Mohan
plating process supplier - Mumbai, India
Q. Is a rolled depolarized nickel anode bar the correct type of nickel bar for an alkaline zinc-nickel plating bath?
STEVEN CARTERCARTER ALLOYS CO - phila, Pennsylvania USA
April 27, 2020
A. Hi Steven. Back in 2004 Asif Nurie in topic 29744 offered a good description of his process, noting that inert nickel anodes are used and the nickel additions are made chemically. It could be that things have changed or that other vendors use different methods; if so hopefully someone will post an update here :-)
Regards,
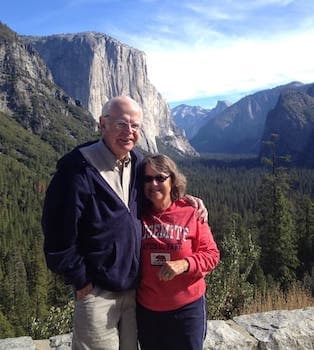
Ted Mooney, P.E. RET
Striving to live Aloha
(Ted can offer longterm or instant help)
finishing.com - Pine Beach, New Jersey
May 2020
A. All zinc/nickel plating baths gradually build up in decomposition products that reduce cathode efficiency. This is true regardless of the proprietary process being used. This effect is more apparent in barrel plating installations than rack installations. This detrimental effect can be eliminated by using one of the proprietary options offered for preventing certain electrolytic reactions from occurring at the anode (membrane or similar products). For installations that are not interested in these special anode options, the most popular anode choice is flat nickel sheets that are at least 6-7 mm (1/4") thick. Another option is to use nickel plated, perforated flat steel plates, similar in thickness to the pure nickel sheets.
Submerged, nickel plated, steel anode rails are suggested in the plating bath, and will reduce clean-up time on the equipment, and provide better contact of the anodes to the buss bar. Titanium baskets should never be used in a process solution due to the poor electrical conductivity of titanium. Likewise, titanium baskets should never be used in the external zinc generator because they will retard the proper chemical dissolution of zinc.
- Cleveland, Ohio
June 15, 2020

Q, A, or Comment on THIS thread -or- Start a NEW Thread