-----
Finishing Shop won't warranty powdercoat finish if applied over hot dip galvanized
Q. As a Landscape Architecture firm working in 5 New England states, we have frequently designed custom steel railing systems for high altitudes, ocean-side and waterfront settings. We typically specify Hot Dip Galvanizing and powder coating (often to match light posts and signage elsewhere on the project) In some cases we have had resistance from the powder coating companies hired to do the painting to offer warranties when finishing over HDG metal. Most project have budgets that support an extra cost in trade for long term durability, so it is difficult to understand the challenges they are expressing with powder coating on galvanized material.
Some finishing companies have proceeded with the work with out question, while others have opted out. We often conduct cleaning and profiling, of the HDG materials, and it has been suggested we pre-heat the parts prior to applying the powder coating to release trapped gasses.
Please advise on 1.Why some powdercoat finishers resist a duplex approach. 2. The best pre-treatment steps (process, materials and products )to insure good adhesion and a long product life that we can get powdercoaters to uniformly warranty.3.The best powdercoat product to apply on HDG surfaces.
Arek Galle
Landscape Architect - East Providence, Rhode Island, USA
May 25, 2010
|
A lot of people have trouble with Powdercoat over HDG.
There are a few tricks:
(1)Galvanisers usually wet quench the galvanised product to speed up cool down. This quench is water with Sodium Dichromate added. The Dichromate is added to delay the on-set of white rust in storage. It also interferes with adhesion of the powdercoat film. Ideally the Galvanised product would be allowed to air cool. Obviously, it is then susceptible to white rust. So it should be protected from moisture and ideally powder coated within 24 hrs.
(2)The galvanising process tends to lock gases into the coating. These gases should be driven off before chemical pre-treatment and powder application. This is generally achieved by pre-heating the galvanised object to about 20-30 °C (metal temperature) higher than the powder cure temperature for about 20 minutes. Otherwise pinholeing is very likely to occur. There are also de-gassing additives that powder manufacturers can add to the powder to delay the gel time and increase the opportunity for gases to escape. I have found it best to combine both techniques.
(3)Chemical pre-treatment is best achieved with Zinc Phosphate or Chrome Phosphate. A grain refined Zinc Phosphate system will provide excellent results.
A typical good quality Zinc Phosphate system would incorporate the following stages:
Alkali clean
Overflowing fresh water rinse.
Activating rinse
Zinc Phosphate
Overflowing fresh water rinse.
Acidulated rinse
Overflowing fresh water rinse
De-ionised water final rinse
This system will provide great key and corrosion resistance.
(4)The quality of powder consumable is also critical.
I have best results with TGIC resin system powders.
I hope the foregoing assists
bill doherty
trainer - newcastle nsw Australia
Like many coating operations, the pretreatment is the most important stage.
If a coater doesn't have the required pretreatment for HDG then applying powder to it will surely disappoint.
A competent pretreatment from HDG to finish will typically include:
* Some "fettling" or dressing of the HDG to ensure its smooth enough, removing spikes drips etc that are typical with HDG.
* Degreasing. Removal of handling greases, oils etc (even if invisible)
* Acid etching
* conversion coating (choices here include zinc phosphate, chromate or newer technology such as manganese.
* all the above should have several stages of rinsing in between.
* drying.
The question of preheating the material is far from clear. Some people claim that the so-called degassing stage will prevent gassing (or blowholes) in the powder, claiming that this gas comes from within the HDG coating somehow. There is little definitive science based research on this to prove or disprove it. If the material is preheated too hot then some pretreatments (zinc phosphate for example) can be detrimentally affected.
The gassing phenomenon seems linked to several variables in the whole process, even including the base steel chemistry.
The best coater to powdercoat on HDG is one specialising in that, not one doing a little HDG occasionally.
Specialists can and do offer warranties on the coating up to
25 years (sometimes more).
Most reputable branded powders can be used on HDG.
An additive (which slows the jelling action in the powder setting) can be used with powders to be used on HDG to good effect.
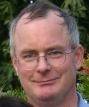
Geoff Crowley
Crithwood Ltd.
Westfield, Scotland, UK
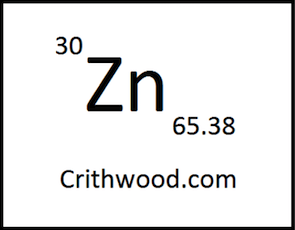
|
Disclaimer: It's not possible to fully diagnose a finishing problem or the hazards of an operation via these pages. All information presented is for general reference and does not represent a professional opinion nor the policy of an author's employer. The internet is largely anonymous & unvetted; some names may be fictitious and some recommendations might be harmful.
If you are seeking a product or service related to metal finishing, please check these Directories: