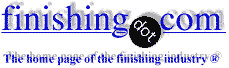
-----
Aluminium alloy 6061 is bead blasted but oxidizes during shipping
Many articles need bead blasting in our company,But we always receive some customer complaint regarding some bead blasting surface is found oxidation stain while the customer receive the parts.generally we check the appearance before delivery, they all are ok without any oxidation stain,but the articles are send to customer by sea,about one month or two months later.the problem will appear. We also take some actions, putting some desiccant with the articles together into package, but the problem still exist.So we have to consider whether we need the other treatment after bead blasting to avoid the oxidation problem.after all the bead blasting surface haven't any resistance for oxidation, the outside is still aluminium.
If you have any experience to deal with the problem.please let me know .I will appreciate your any comments
Quality engineer - DongGuang, Guangdong, China
May 20, 2010
First of two simultaneous responses --
Paul, Not sure I understand your exact corrosion / oxidation issue? Is it white or some other color ... ? What type of blast media is presently used? What type of parts? Can the parts be blasted in the USA?
I'd recommend using a non ferrous blasting media. Depending on your goals for surface texture, life of media and costs; stainless cut wire, aluminum cut wire or aluminum oxide, etc.. all will work. If the corrosion persists after shipment some sort of barrier coating / rust prevent would need to be applied to the parts prior to export depending on the next operation.
North Tonawanda, New York
May 22, 2010
Second of two simultaneous responses --
Aluminum + atmosphere (that too of the ocean)+ time = definite corrosion. Adding a desiccant is not a solution.You could try trivalent passivation or anodizing the part to give it some kind of surface protection and prevent corrosion. If the part is in sheet form, peel-able lacquer could give some kind of protection too. You will of course have to check with your customer to see if the surface finishing is alright with them as it would be a definite increase in cost and cause variation in appearance. You will also have to meet with the minimum requirements of the surface finishes and find a compatible job worker who can give good results. I hope this helps.
Winston D'Souza- Bombay, India
May 23, 2010
Dear all
I need add some information
This article is a tubular,the OD need be blasting;The media of blasting is stainless steel beads.the oxidation is significant black spot.
We ever did passivation for some article after bead blasting,the colour is more white than the ones without passivation.the cost also increase so many.
Though we talked with customer's designer ,He don't believe the article with blasting will oxidate at all.
- DongGuang, Guangdong, China
May 25, 2010
Q, A, or Comment on THIS thread -or- Start a NEW Thread