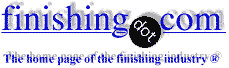
-----
Standard Tests for silver plating on copper
My product is electrical ( MCCB ) and as such we are doing silver plating on copper plates. please suggest me a suitable test to check the life of plating.
Is Salt Spray Test an option ? If yes what is the standard for copper.
Product Development - India
May 14, 2010
May 21, 2010
Dear Amit,
Allow me to first quote some text from the article of Bella H. Chudnovsky, "Degradation of Power Contacts in Industrial Atmosphere: Silver Corrosion and Whiskers":
gases, such as H2S, OCS, CS2, and SO2. Corrosive effect on silver of H2S and OCS gases
is about an order of magnitude stronger than that of CS2 and SO2. However, silver sulfide
can be formed by contact with SO2 in moist air, but only at SO2 concentration two to
three orders of magnitude higher than typical of ambient environments.
Hydrogen Sulfide (H2S) is usually present at the chemical plants, oil refineries,
production of artificial fibers, steel mills, and the paper and pulp processing industry due
to process technologies. It was found that even at minor concentration of H2S in
atmosphere, corrosion produces silver sulfide on the parts being in contact with
environment.
In electrical apparatus, conductive parts are usually made of Copper with Silver plating.
Both base metal (Cu) and plating (Ag) corrode in this environment. Two processes are
active at the same time: general corrosion of silver and creep corrosion of copper.
In recent years, investigations on silver plated contacts used in such industrial
environment, have in some cases shown also strong indication of growth of copper
corrosion products on silver plated surfaces. Unlike most other corrosion films, the
growth of the silver sulfide film is linear over time. There are many factors such as
other pollutants, exposure time.
Ag+ + e- _ Ag 0.800 V standard electrode potential
Cu2+ + 2e- _ Cu 0.340 V standard electrode potential
The equation above shows the galvanic cell potentials of both copper and silver metal reduction. Based on this data, the copper, due to being the more active metal, will always be the anode when electrochemical reactions are possible with these two metals. In addition, copper corrodes significantly faster than silver in a sulfur based oxidizing environment. This results in a very high corrosion rate. The corrosion product contains metallic material that is highly conductive.
Therefore porosity is important if you plate on a Cu-containing base.
Having said this, there are many corrosion tests for Silver on Copper. See e.g. ASTM D4752 and IP PM-DJ 2005. (General Specification for Automotive Spark Ignition Engine Fuels) They prescribed this test for silver plated parts too, due to problems with Silver in the automotive industry. (Sensors in modern automotive fuel systems often use of silver or silver alloys, which are susceptible to corrosion from sulfur in gasoline. In the past decade, refiners have shifted to producing lower-sulfur gasoline. The process includes more severe hydrotreating, which destroys naturally occurring compounds that give some protection against sulfur-based corrosion. As a result, even low levels of sulfur in gasoline can corrode silver.)
In fact, a rash of fuel-sensor failures in mid-2004 was traced to sulfur-related corrosion of silver and copper alloys used in sensors
For testing you can think about dipping the Silver plating in K2S-solutions or expose parts to SO3-gas and/or do a thermal test to look for porosity and adhesion..
For a more scientific approach (But I have to warn you, you need skilled people on this!)
Use Battelle's Class III Flowing Mixed Gas environment to simulate an accelerated outdoor
environment consists of the following parameters:
- Hydrogen sulfide gas: 100 parts per billion (ppb)
- Chloride gas: 20 ppb
- Nitrogen dioxide gas: 200 ppb
- Temperature: 30 °C
- Relative humidity: 75%
The acceleration factor for uncoated electrical connectors is approximately one year for every two days of exposure in the test chamber. This factor does not necessarily apply to coated surfaces. The chamber air exchange rate should be in accordance with ASTM B845, the "Standard Guide for Mixed Flowing Gas (MFG) Tests for Electrical Contacts," Method H.
(You better contact the Batelle Memorial Institute directly for questions about test and correlation to "real life".)
Salt spray (fog) test
A salt spray corrosion test (ASTM B117) can be conducted on Silver in
order to determine its susceptibility to salt water corrosion.
A simple linear relation between result of the tests and "real life" time doesn't exist, as you have too many different parameters in the outside world.
If you google for: " Atmospheric Corrosion of Silver and Its Relation to Accelerated Testing
E.B Neiser and R.G. Kelly" you will get some idea.
To name a few...where are the parts exposed? Heavy industrial atmosphere, nearby sea? In a pollution free area? Indoors, in a controlled atmosphere? Is some form of wear involved? Surface structure of the base on which you plated & properties.....
In general you can say that thicker silver lasts longer and the better your pre treatment and the less the number of pores, the better it's performance will be.
Depending upon your application, you could consider the use of passivation (metallic or organic by nature).
Still a lot more to tell, but I hope this is a good start for you.
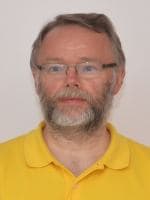
Harry van der Zanden
consultant - Tilburg, Netherlands
Q, A, or Comment on THIS thread -or- Start a NEW Thread