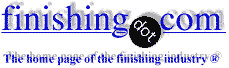
-----
Glass Fibre Reinforced Polyester Tank for Alkaline Cyanide Free Zinc Process
Q. We are an electroplating job shop in Istanbul specialist about zinc plating. we are about to make up a new alkaline cyanide free zinc electrolyte and like to use glass fibre reinforced polyester tank. does anybody have an idea if this kind of tank will react with the electrolyte or is it safe.
Emrah NAL- Istanbul, Turkey
2000
A. Hi !
Why don't you check with your local manufacturers of FRP resins. In North America there are trade names such as DERAKANE and HETRON and ATLAC all of which are superb acid resistant polyesters and vinylesters. The rule of the thumb is to use a Vinylester resin where there are any alkalines.
But consider some other things, too. If you lift parts in & out you could scrape the walls of the tank.
All fibreglass products, if even correctly made (!) do NOT like abrasion as they not homogenous throughout like the weaker thermoplastics. Food for thought. Cheers !
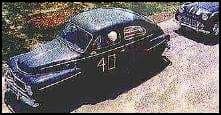
Freeman Newton [dec.]
R.I.P. old friend (It is our sad duty to
advise that Freeman passed away 4/21/12)
A. Hi, I know that the Hetron and Derakane are not available throughout Europe (trust me, I tried !). However, we found a supplier of FRP tank linings in Holland, and they have a very good FRP tank lining. We use it in one of our hard chrome plating tanks, as a replacement for our Koroseal lining. They company's name is Innoplate International. Tim
Tim Jaarsmahardchroom - Hengelo, The Netherlands
A. My personal experience as a supplier of zinc plating and other chemistry is to draw up a specification for the supplier of the tank or resin stating that it must be tolerant to the electrolyte and WILL NOT LEACH in the plating solution.
I then prove this by getting a sample of the finished product (or comparable sample) or by making one up from the resin.
I then take a liter of the plating solution. Run a Hull Cell ⇦ huh? test with a sample from the liter. Adjust solution for optimum results.
Run another sample from the liter. SAVE PANELS!
Soak sample of the tank material in the plating solution for 1 week.
If the solution is heated, it should be heated the same number of hours per day as it would be if operational.
After the week run a new test panel.
It should be similar to the optimum one (or slightly less bright). If it is hazy or cloudy or shows other signs of organic contamination, then the resin or tank material is not suitable for that particular electrolyte.
Please note, this is a rudimentary test, but it has proved a point many times when troubleshooting installings in new or newly relined tanks. Gene
Gene Packmanprocess supplier - Great Neck, New York
Re. Gene Packman's comments. (& what is his Company called?) Yes, that is right. Make up a sample. Test it in the solution at the operating temperature for at least a week.
HOWEVER, even a well made sample may not exactly reflect operational usage. Why? Because with samples, one takes t.l.c. and can spare the time for Tender Loving Care. Hence the pedantically correct amount of catalyst and promotor is mixed with the resin. This may not always be the case with the finished product.
Further, a good FRP laminate will have a so-called corrosion barrier consisting of just pure resin and mat (NO cloth or woven roving!) with perhaps a veil coat (90% resin) over that. Even further, some manufacturers will, h'm, reduce their costs by using only the expensive top-of-the-line resin in that max. 0.l00" thick corrosion barrier. Makes them very competitive, doesn't it!
I am somewhat biased against FRP constructions sometimes, ESPECIALLY for chrome tanks! My preference being a tank made out of type l, grade l PVC suitably fibreglass reinforced so that it doesn't deflect. Disadvantages? Size limitations! Costly! Also, as with Koroseal type linings, I would have used a shieldof, say, 1/4" PVC at the liquid/air interface.
The world's first successful PVC:FRP dual laminate plastics were made in Canada ... l96l ... although current bonding techniques to the PVC are much simpler to-day ... and it is the permanence & strength of the bond which is critical to success as one can go to much higher operating temperatures one can reduce the thermal expansion factor to that of the fibreglass.
Cheers !
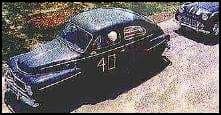
Freeman Newton [dec.]
R.I.P. old friend (It is our sad duty to
advise that Freeman passed away 4/21/12)
Freeman, My company name is not included since I am not an advertiser on this site. I am including it now since you asked Gene Packman, PAX Surface Chemicals, Inc.
Gene Packmanprocess supplier - Great Neck, New York
Q, A, or Comment on THIS thread -or- Start a NEW Thread