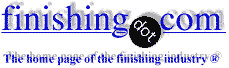
-----
How Do You Test for 303 Stainless Steel
I've got some components supposedly made from 303 and they've gone totally corroded, is that normal and how can I test if they really are 303
Ian Wilson- UK
2000
Stainless means corrosion resistant, not corrosion proof. 303 is the low end of the resistance. Even great SS like 316 will corrode badly if mistreated. Complete corrosion on 303 with nothing else stated would not be unusual at all.
James Watts- Navarre, Florida
2000
The first test that I would do is to check it with magnet. If the magnet sticks, it is most likely not 303 stainless steel - probably plain steel or 400-series stainless. If it doesn't stick, the material could be 303 or any of the other 300-series austenitic alloys - 304, 316, etc.
There are chemical spot tests that you could use to sort it out, but these are rather tedious and involve a wide variety of chemical reagents. If you really want to know the alloy, your best bet is to send a sample off to a test lab for chemical analysis.
BTW: Mr. Watts is right - any stainless steel alloy will corrode in the wrong environment. Let us know what this part was exposed to, and maybe someone can suggest whether 303 should stand up to that environment.
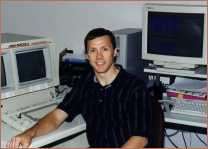
Larry Hanke
Minneapolis, Minnesota
2000
2000
Hi !
As the man (men!) said, 303 is at the low end of the table, probably a low nickel content. All stainless steel can corrode ... can even rust as some photo labs have found out to their chagrin.
We, in the English language happen to call it 'stainless'. Germans call it 'rust free' ... in French it's 'non oxidizing'. An euphemism, eh?
The manufacturers of s.s. will have corrosion charts showing the difference between the ordinary type 400 series and the better 316 series. You might well be able to run your own tests if you saw the difference between these series based on a given corrosive material.
Lastly you say that you were told that your stainless was a series 300. But were you told the truth?
I don't know the UK mfgrs. names. You could try HENRY WIGGIN (Birmingham and London). They could point you in the right direction. But their super NiCr alloys are the best in the world and expensive and reach far beyond mundane 3l6 stainless in quality.
Cheers !
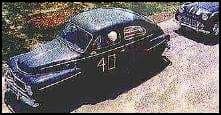
Freeman Newton [deceased]
(It is our sad duty to advise that Freeman passed away
April 21, 2012. R.I.P. old friend).
Ian,
I have run into this problem before. We had some parts made for corrosion testing that were supposed to be stainless steel, but the plant used the wrong components. They used some low carbon steel components instead of stainless steel components. We used a magnet to prove that one of the three samples was built incorrectly. The one that rusted stuck well to the magnet.
The magnet test works if the metal is actually not stainless steel. It may not help if they are just different grades of stainless. Make sure you use a large, strong magnet. A little one will not help.
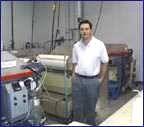
Tim Neveau
Rochester Hills, Michigan
2000
Scrap yards use x-ray fluorescence to test for different alloys. This is an easy, non-destructive test if you have the right equipment. My suggestion would be to contact a local scrap dealer. He should have the equipment and know-how to help you determine if it is 303 SS.
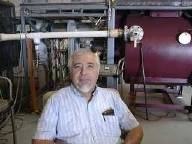
Jim Treglio - scwineryreview.com
PVD Consultant & Wine Lover
San Diego, California
Most of the responses read so far are on the mark. Two simple tests will tell if the material is 303 or not. First, check for magnetism with a strong magnet. There may be some residual magnetism from cold working. Second, make a 5% solution of sulfuric acid [sulfuric acid on Amazon, affil link] . Obtain some glossy photography paper, Kodachrome II RC available at many camera shops. Cut a strip of the paper, soak it in the acid for 45 seconds and then apply the emulsion (smooth) side it to the material for 45 seconds. Remove the paper and look for a brownish stain. This indicates significant sulfur present. Only 303 and 430 F are resulfurized; 430 F is magnetic. Procedure is courtesy of Central Steel and Wire, Chicago, Illinois and has worked many times to sort suspect material.
Bruce Croix- Monee, Illinois, USA
2000
How can I verify or test screws and washers which I purchase are made from SS316 and not SS303?
Doron MoskovichQuality manager - Israel
2007
Q, A, or Comment on THIS thread -or- Start a NEW Thread