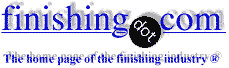
-----
Want satin crystalline finish from anodizing
May 6, 2010
Hello Guys,
We are aluminium anodizers situated in western part of India. We are looking for crystalline matte finish. we have tried many things but we are consistently failing in it. Do we have to add some additive to the etching solution to get the required finish? If so which additive is suitable one? Or the finish can be derived from buffing? If so what type of buffing have to be done on the aluminium section?
Waiting for the replies
Plating Shop - Ahmednagar , Maharashtra, India
Aluminum etched in a solution which has ammonium nitrite and ammonium bifluoride will matte the surface evenly.
John Hu- Singapore
May 8, 2010
Dear Sir,
I have tried ammonium bifluoride but in that we get a milky matte finish. I am looking for satin crystalline or scotch brite finish which is generally done by adding some additives to etching solution. I am actually looking for the proper additives which can give me proper finish. If you can help me please reply over it. Anyways thanks for responding to the thread
- Ahmednagar, Maharashtra, India
May 11, 2010
Hi, Sumit. You have previously asked the same question as letter 49178 and as letter 50951, and received 7 answers now without success. How do you come to know that this process can be done via additives to the etch solution, but not ammonium bifluoride? Have you seen it done by others? Has a supplier offered you a proprietary but you don't want to buy it from them?
If you can send a photo of the finish you are looking for, maybe we can all be on the same wavelength because there are so many different finishes for aluminum and they are achieved by etching or bead blasting or bright dipping or with a timesaver or by applying a lacquer, and apparently you have a different finish in mind than the other readers are picturing from the verbal description description. Good luck.
Regards,
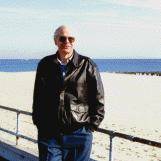
Ted Mooney, P.E.
Striving to live Aloha
(Ted is available for instant or longterm help)
finishing.com - Pine Beach, New Jersey
May 2010
First of two simultaneous responses -- May 13, 2010
You could get satin finish as follow:
1. clean the parts
2. bead blast the parts with girt #220
3. soak clean
4. caustic light etch
5. de-oxide
6. bright dip
7. de-oxide
8. anodize
- Singapore
Second of two simultaneous responses -- May 15, 2010
Dear Sir,
You are very right that their may be ambiguity in perceiving the finish. It's better to upload the photo.
I have tried different concentration of etching solution of sodium hydroxide and with many permutation and combination of timing but I failed to got the satin matte crystalline finish.Many customers have approached us with a sample from China or UK or US which have the finish for which we are looking for. Many have suggested us that their is a additive to be added to etch bath to get the required result. We are looking for the companied which can provide us the additive.
Your response and help over this is highly appreciated
Hello John,
Thanks for replying. I am unknown to the concept of bead blasting. Does bead blasting mean buffing of aluminium section or polishing of aluminium sections with polishing/buffing wheel of aluminium oxide. If you can please tell me bead blasting I will be grateful to you. And please specify what did you mean by deoxide ?
- Ahmednagar, Maharashtra, India
Thanx Ted for uploading the pics. This is the type of finish I am looking for. Eagerly waiting for positive follow up over this.
Sumit Lodha- Ahmednagar, Maharashtra, India
May 27, 2010
Sure as what I said before (bead blast, bright and clear anodizing).
You can get knowledge on bead blast technique on internet.
- Singapore
May 28, 2010
May , 2010
Hi. Unfortunately the pictures are a bit out of focus, and it's hard to photograph a reflective surface anyway. But as I look at them I would agree that they look bead blasted. However, unless it's just due to poor focus, they have sort of a syrup-y look to them, and I'm wondering if there is a lacquer/clearcoat sprayed on them after anodizing? Sometimes lacquer is applied to discourage fingerprints.
Regards,
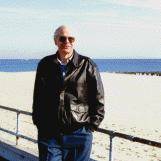
Ted Mooney, P.E.
Striving to live Aloha
(Ted is available for instant or longterm help)
finishing.com - Pine Beach, New Jersey
Dear Sir,
Thanks for the valuable responses. I know the pics are little out of focus and are creating ambiguity. Can I post the samples at your end so that you can get clear view of it. I will try to learn about bead blasting techniques through world wide web, hope it works for me.
- Ahmednagar, Maharashtra, India
June 1, 2010
Hi, Sumit. Bead blasting is similar to sand blasting. It is done in a similar cabinet, but the beads are small, round, and uniform size. The result is dimples of such small size that they don't look like dimples, but a very uniform satin finish. You often see this finish on firearm components (although those components are stainless steel rather than aluminum).
I don't have nearly the depth of experience of some of our readers, so sending the parts to me would not help the real experts see them. But I do think it is possible for you to send digital photographs that are fully in focus :-)
Regards,
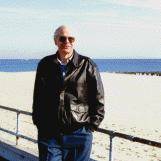
Ted Mooney, P.E.
Striving to live Aloha
(Ted is available for instant or longterm help)
finishing.com - Pine Beach, New Jersey
May , 2010
June 5, 2010
Dear Sir,
Thanks for your valuable solutions. In past 4-5 days I have done little study on blasting. I will be also visiting some blasting shops to get more idea about it. When I enquired them about bead blasting. They asked me following queries
1) What material should be used in gun means whether we have to use sand or aluminium oxide or some another material?
2) At what psi should the operation be operated?
3) what should be the grit size of the material?(In previous reply it was suggested 220 grit. I heard the more the grit size more will be the matte finish. Is this true? )
I know I am bugging too much over this. Your each and every reply is been useful to me and I am very much grateful to you all for this.
waiting for your valuable responses,
- Ahmednagar, Maharashtra, India
Surely there is a firm that sells the blast equipment where you could take samples of your product and they would blast it with several different sized beads. Most companies want to sell both the equipment and the beads. A happy customer means more sales.
Words do not properly describe the finishes that you can get as the blast angle, bead size, pressure and even nozzle size makes some differences in the look.
- Navarre, Florida
June 8, 2010
Grit size selection (aluminum oxide) depends on the roughness requirement of your finished products. 45 psi of blasting pressure would be suitable for your purpose.
John Hu- Singapore
June 11, 2010
Ed. note: Mr. Lodha has now provided this clearly focused closeup of the finish he is seeking --
Thanks for uploading the photo. This is the type of finish we are looking for. Please give me necessary suggestion and advise. In the mean time I have sent some samples to a blasting vendor and have asked him to use glass beads as the media.
Waiting for your valuable responses.
- Ahmednagar, Maharashtra, India
June 16, 2010
June 25, 2010
Dear Sir,
Yesterday I received a sample of aluminium which was blasted with glass beads of ad grade. The sample had little dark tone in finish and had smooth surface. I kept that sample in nitric acid solution of some 10% concentration for 15 minutes and anodized it in sulfuric acid bath for 30 minutes.
To my surprise after anodizing the sample went black. Please convey me what wrong must have been went and what I should do it to ensure proper finish.
Your valuable responses are always appreciated.
- Ahmednagar, Maharashtra, India
First of two simultaneous responses --
Sumit,
You will need to electropolish the sand/bead blasted parts to give it some kind of lustre. Just a caustic/nitric wash will give you the matte grey tone that you achieved.
There are plenty of suppliers here in Bombay who will give you the right chemicals to achieve the kind of finish you are looking for. Your only worry would be to maintain the temperature (around 40-50 C)and solution concentration to get the right results.
While sandblasting will give you the grainy finish you are looking for, remember that it is an additional cost which is almost equal to that of the anodising rates. Hope this helps.
Best regards,
- Bombay, India
June 26, 2010
Second of two simultaneous responses --
follow the process mentioned in my former response (you missed bright-dip process)
John Hu- Singapore
June 27, 2010
Q, A, or Comment on THIS thread -or- Start a NEW Thread