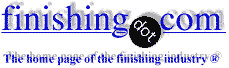
-----
Undisputed best coating system for high volume small stamped steel parts?
[an error occurred while processing this directive]Our company has designed a dual flush retrofit kit for household toilets. We are in the process of selecting a coating system for a steel component which is to be used as a weight inside a toilet tank which will be submerged in tap water for the life of the product. This component is used strictly as a weight to sink the flapper of a toilets flush valve, if the steel gets a minor coat of rust that is okay however we can not end up with a big lump of rusting deteriorating steel which will harm the rubber flapper that is directly below it. Is there an undisputed best coating system that is low cost for a high volume small stamped steel part that can provide the performance we are seeking. The life expectancy goal for of the product is 10 years.
Aloha,
President / Owner of the Product Company - Honolulu, Hawaii, USA
May 3, 2010
Steel. Underwater. Ten year life. Tough specifications. a fairly heavy coating of heat cured vinyl plastisol might work, however an uncoated chunk of lead might cost less.
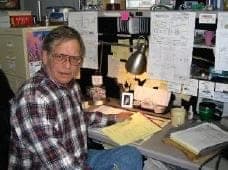
Jeffrey Holmes, CEF
Spartanburg, South Carolina
May 5, 2010
It has always has been an accepted practice to try to make one part do as many functions as possible. All parts eventually fail and more parts generally mean more parts to fail. Also 2 parts generally cost twice as much as one part. Your flapper, I suspect, is rubber so that it can seal. Rubber is cast. Rubber is heavy. Modify your design to have the flapper weight changed to the required weight and cast up as many as you need and fire the guy that came up with the metal weight idea. Occam's razor always applies.

Rod Henrickson
gunsmith - Edmonton, Alberta, Canada
May 6, 2010
Or you can insert mold a piece of steel into the flapper. G. Marrufo
Guillermo MarrufoMonterrey, NL, Mexico
May 10, 2010
Provided the flapper is a thermosetting polymer like rubber or silicone,there are phosphate-based conversion coatings for mold-bonded parts, with excellent adhesion. The polymer will break before the polymer/substrate interface.
You could cure the polymer right onto the stamped piece of steel.
- Toledo, Ohio, USA
May 11, 2010
You might want to consider a thermoplastic coating for the steel part. It will provide years of protection in that type of mild chlorine environment. It can be applied in various thickness to allow for your tolerances.
Craig Gaskincoatings - Surrey, BC, Canada
May 18, 2010
![]() |
May 20, 2010 Rod, ![]() Harry van der Zanden consultant - Tilburg, Netherlands May 20 Hi, Harry; it's nice to have your comments back on the threads. I'm sure Rod was engaging in hyperbole, and that his advice to fire the guy was just an expression rather than serious advice :-) Regards, ![]() Ted Mooney, P.E. Striving to live Aloha (Ted is available for instant or longterm help) finishing.com - Pine Beach, New Jersey Hi Ted, Best regards to all, ![]() Harry van der Zanden consultant - Tilburg, Netherlands May 21 |
Jeff, a couple years ago I made a repair to an older office toilet where the new adjustable flapper would not even work... "to close & refill tank". The water would just keep running with the flapper open. I found a standard 3/8" 18-8 stainless steel washer and dropped it down the pull chain on top of the flapper. Now it shuts every time (50 -100 times a day) for 2 years strong. I looked at ss washer the other day and it is still fine. Cost was only pennies and should last over ten years. Hope this helps!
Tim DeakinNorth Tonawanda, New York
May 22, 2010
Q, A, or Comment on THIS thread -or- Start a NEW Thread