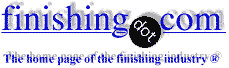
-----
Wear resistance of chromate over cadmium
Type II chromate over Cadmium, QQ-P-416F, scratches easily. Does not appear to be wear resistant. what is the best way to approach this from an acceptability of scratches?
Parts are connectors.
Cable Assemblies - St. Petersburg, Florida
May 3, 2010
First of three simultaneous responses --
Don't handle it for 24 hours is a start. the chromate is for corrosion protection and not wear resistance. PS: the cad scratches easily also.
James Watts- Navarre, Florida
May 5, 2010
Second of three simultaneous responses --
Chromate films are basically a gel. When it scratches, it heals itself. You may see a cosmetic scratch, but that doesn't mean that the chromate isn't performing its function.

Jon Barrows, MSF, EHSSC
Kansas City
May 5, 2010
Third of three simultaneous responses -- May 6, 2010
Phil,
Not a lot to go on, but cadmium is very soft for a metal and the chromate film applied is very, very thin. This coating type is not applied for its wear resistance.
Now, the crucial question is does the scratch go down to the base material, i.e. can you see the steel/aluminium under the coating?
If it does go down to base metal you can repair the scratch by dressing out the area and then electrobrush plating the area (often called Dalic Plating or Selectron Plating, these are brand names). If the scratch is just a surface defect then you can touch up the scratch locally with a passivation solution. If it is a yellow/gold iridescent passivate rather than an olive drab passivate you could use the following solution:
Sodium dichromate 150-200 grams per litre
sulfuric acid (s.g. 1.84) 4-9 ml per litre.
Swab clean the area, apply the solution by swab or brush. Leave on the surface for 15-30 seconds and then rinse off with distilled or demineralised water. Allow to dry, it may be aided with dry compressed air, but do not wipe dry as the coating will still be very soft.
Aerospace - Yeovil, Somerset, UK
Q, A, or Comment on THIS thread -or- Start a NEW Thread