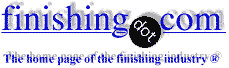
-----
Can't get required anodizing thickness on A380 casting
I have a small part (.01 Sq Ft) that's an A380 casting. Minimum thickness requirement is 30 microns and we're only achieving about half of that regularly now. We've tried varying time and Amperage (100 volt rectifier) on TI and AL fixtures but can't seem to get the thickness. Any thoughts on preferred Chemistry additives, temp, etc?
Chris PattersonPlating Shop Employee - Williamsburg, Virginia
April 14, 2010
First of three simultaneous responses --
If you have 100 volts available, that leaves solution temperature, agitation, sulfuric make up and racks capable of carrying the amperage drawn. Also, everything but the contact points needs to be masked off for optimum use of available current.
James Watts- Navarre, Florida
April 16, 2010
Second of three simultaneous responses -- April 16, 2010
Are you aware that half the thickness is UNDER the original surface so if you are measuring mechanically then you have to double the reading.
If you are measuring with an eddy current instrument you must calibrate the instrument on a bare piece of the same cast alloy, and do it in several places to average out the porosity effect.
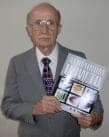
Robert H Probert
Robert H Probert Technical Services

Garner, North Carolina
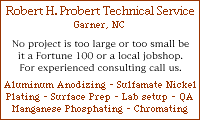
Third of three simultaneous responses --
Experience with A380 diecast tells me you can't get much over about 0.0007 - 0.0008" thickness. The more you try the more spongy and powdery the resulting coating will be. Excessively etching to remove alloying constituents will help your coating, but your customer may not be happy otherwise!

Milt Stevenson, Jr.
Plating shop technical manager - Syracuse, New York
April 17, 2010
Thank you all. We are masking all but contact areas on the racks, and have what we believe to be sufficient agitation and carrying capacity on the racks. We are running in the 40 deg F range, thoughts?. We are using a higher end eddy current device and calibrating on the actual parts. We understand the growth/penetration of the coating. What is your definition of significant etching?
Chris Patterson- Williamsburg, Virginia
April 20, 2010
Q, A, or Comment on THIS thread -or- Start a NEW Thread