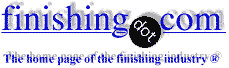
-----
Caustic Analysis -- aluminium anodizing etch

Q. I have been reading this site for a very, very long time. Not frequently. Only when I need data. Hahahahahaha!
www.zhuongrong.com.tw/userfiles/files/20211222115710834.pdf
In the title "Alkalinity", may I know how is that active and inactive alkali calculated?
I cannot seem to get the numbers as shown. Sodium hydroxide is the only exception as it is straightforward.
I wrote to PQ Corporation. They do not reply, sadly.
(I have another question related to sodium metasilicate, but I think it is wise for me to open a new thread as the topic is not about active/inactive alkali. And since this is a community thing, people would easily find relevant pages by the headline/search term, I think).
Hobbyist, wannabe scientist. - Malaysia
May 2, 2025
A. Christopher,
The matter at hand here is that of strong acids/bases versus weak acids/bases.
With strong acid and bases, such as HCl and NaOH, as you said it is straightforward. There is full dissociation between the components.
With weak acids and bases, the dissociation is partial and exists in an equilibrium. The dissociation constants for these equilibriums are studied and are well known for common substances. Acid dissociation constants and commonly referred to as the Ka, and the alkaline/basic equivalent is Kb.
I could be wrong, but I expect this is what they mean by "active alkali" (dissociated OH-) and "inactive alkali" (undissociated OH-), with the "total alkali" being the sum of the two, i.e. what you would get if the equilibrium was driven all the way to the one side, such as by reaction with excess acid, such as a titration. Notice also that the pH is governed solely by the "active" or dissociated OH- or H+. Also notice that solutions of weak acids and bases typically create pH buffers due to the equilibrium effect.
That should give you enough information to find further information on these topics should you need it.
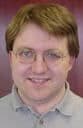
Ray Kremer
Stellar Solutions, Inc.

McHenry, Illinois
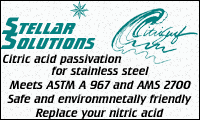
Yo Ray!
I read your content and...whoa!
Firstly, you read my mind even when I mentioned nothing on dissociation! You also mentioned buffer! Apt information!
Secondly, I did not know that alkaline substances also has undissociated and dissociated forms/states! I mean, I do know that there are alkaline buffers. I have been making tris-EDTA-borax buffer as otic solution for a very long time. What I mean is buffers in relation to metallic stuff are rather new and amazing to me.
I am not a business person but I coincidentally possess some chemicals that are frighteningly identical to what is used as corrosion inhibitors AND for cleaning metals. I coincidentally want to clean air-conditioner fins which are coincidentally aluminium. Price of hiring people to clean/wash is exorbitant. Air-conditioner cleaner in a can is either too weak or too harsh on aluminium. Which is the reason why I am bothered to make my own aluminium cleaner that is strong enough, and safe on aluminium.
But I will make a new post about it (easier for other people to find, and not all mixed and messed up). I think people in the business such as you would not respond, or would not respond in full, because I understand that corrosion inhibition is a billion dollar 'trade secret' despite this site is a community thing.
All right. I will then not bother about calculation. As you mentioned and what I read what others had mentioned, the only way to know the numbers is to titrate. Neither do I have the materials, advanced knowledge, nor equipment to do so.
Once again, you are amazing! I did not know that you have been in the business for almost 30 years, and that you are a material scientist/chemist! No wonder you sort of know what I ask without me directly asking.
Hobbyist, wannabe scientist. - Malaysia
May 16, 2025
⇩ Related postings, oldest first ⇩
Q. I've become responsible for doing this - there are many ambiguities. "Free" sodium hydroxide..."total" sodium hydroxide...my heads in a maze. I have finally managed to get the "right" answer (what the production manager expected) by titrating a 5 ml sample with 1.0N NaOH [1N NaOH on
Amazon [affil link]
to a phenolphthalein endpoint, and multiplying the titrated volume by 5.1. I do not know where this factor comes from; or its chemical significance.
The vendor provided another procedure that dictated titration to a pH of 11.0 (by pH meter) that yielded consistently low results.
Does anyone out there have any helpful words of wisdom?
Help!
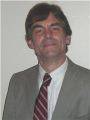
Dave Wichern
Consultant - The Bronx, New York
April 9, 2010
![]() ![]() |
"The Chemical Analysis of Electroplating Solutions"
by Terrance H Irvine ![]() on eBay or Amazon or AbeBooks (affil link)
"Analysis of Electroplating & Related Solutions"
by Langford & Parker ![]() on Amazon or AbeBooks (affil link) A. Hi Dave, - Navarre, Florida A. Hi Dave - Auburn, Washington A. Dave - Colorado Springs, Colorado A. Hello, Dave. The two things that you really want to know in an aluminum etch bath is the free caustic and the total aluminum content that has built up. This is an analysis that I use for a bath that has about a 40 g/L free caustic content and <50 g/L aluminum. The bath that I have used also contains sodium carbonate and sodium gluconate
(to chelate the aluminum). You may need to adjust this analysis depending on what you have exactly. I hope this helps. ![]() Jon Barrows, MSF, EHSSC Kansas City |
Q. I am still confused.
Using different procedures, I get wildly divergent results.
I gather that there are three bath components that contribute to etching activity: sodium hydroxide, sodium aluminate, and the sodium salt of whatever organic acid they put in the "anti-scale" additive. Is there any simple way of determining each? Is there any way of determining each?
I have found that addition of the anti-scale additive reduces the titrated NaOH concentration substantially. Have others found the same? If so, please inform me.
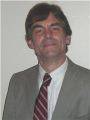
Dave Wichern
Consultant - The Bronx, New York
May 28, 2010
A. I agree with John Barrows analysis method. That was the method used in Alcan NZ for all three of their anodising plants.
John Arrolmetal Treatment - Singapore
October 26, 2014
Q. Dear friends,
What is the significance of dissolved aluminium in Etching bath? We use NaOH as etchant, does Aluminium play any role in etching bath?
- Abu dhabi, UAE
November 11, 2014
Caustic Etch Analysis
Q. I started a thread about this a few years back. Had some time to think about it - how to put this on a rational, scientific basis.
How about this: measure the viscosity of the bath with an Ostwald viscometer. Then, dilute the bath with DI water, then add back enough sodium hydroxide to keep the alkalinity constant. Now measure the viscosity again. Repeat this for 10% fresh water + NaOH, 20% fresh water + NaOH, etc. You'd need at least 5 - 6 dilutions, as the relationship between dilution and viscosity will not be linear.
Now, evaluate the etch rate you get from each dilution + NaOH empirically, by etching a test coupon and weighing before and after. Very strict attention would have to be paid to keeping agitation and temperature constant.
Now, you have an idea between viscosity and the effective etch rate. One could measure the viscosity and alkalinity of your working bath and add just enough NaOH to get just the etch rate you wanted.
Why should this be? Well, as the bath ages in service, and sodium aluminate, sodium [anti-scale additive] sodium carbonate, and other crappo build up, the viscosity will change. This will affect the rate at which active etchant diffuses into the work piece/process bath interface zone, and hence the etch rate.
Does this make sense? Has somebody done this already? Am I totally full of beans?
Sounds like a lot of work, too. If I had a place to do it I'd do it for free. Might make a nice article for a trade journal. Also, this problem got under my skin and I would like to solve it.
Thanks in advance for any feedback.
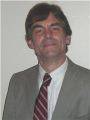
Dave Wichern
Consultant - The Bronx, New York
August 14, 2015
Q. I was hoping for some feedback. Oh, well.
I've changed my thinking about this, a lot.
The etch rate determinations aren't necessary. That eliminates lots of work. I found this great Paper in the Journal of Chem & Eng Data - "Viscosity, Density, and Refractive Index of Aqueous Sodium and Potassium Aluminate Solutions." Answered two questions: is viscosity related to aluminate concentration? and, is the change sharp enough to precisely determine aluminate from viscosity?
Yes, and yes. A solution that's 1.28 M in Al has a viscosity of 2.187 centistokes; for 1.09 M, it's 1.798 centistokes. That's an almost 10% change. Viscosity can be measured very precisely if you have good technique and careful temperature control.
So, to make a long story even longer...take a nice big sample of the etch when it's doing good. Now, take two portions out; dilute one 8% with water, another 4%. Take another (large) portion and stick a weighed Al coupon in. Let a bunch dissolve. Take the coupon out, weigh it. Split the sample in half, stick the weighed coupon back in one of the portions, and let a bunch dissolve. Pull it out and weigh again.
Now, you have 5 samples. Add sodium hydroxide to the diluted, and the Al enriched samples to match the original NaOH concentrations. This is easy to calculate. Measure the viscosity of each. Plot the data on a graph: aluminate vs viscosity. Call the original aluminate "A(sub)0. Then you have 5 points; you still don't know A(sub)0. But you now have two points above, and two below, the original aluminate value. From looking at the graph, you should be able to figure that out.
I'll stop here. I may be boring you all, or my math might be bad.
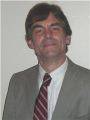
Dave Wichern
Consultant - The Bronx, New York
Q. I've seen phenolphthalein
⇦ on
eBay &
Amazon [affil link]
mentioned in a couple locations now (here, and on Anoplex website "Caustic Etch Titration" page) regarding caustic etch titration. It seems there are numerous different preparations available. Which preparation should be used for this?
Our machine shop has just started up a small anodizing line to bring in house the anodizing of one product we're making. We were running successfully for a few weeks at the start, but are now learning the failure points (we knew that would happen) and starting to learn how to analyze and manage them. One issue seems to be that the caustic etch bath has become weak and less effective (not removing as much material as before, less visible effect on surface of parts).
- Cambridge, Ontario, Canada
August 9, 2021
A. Titrate with 1 ml sulfuric acid to 2 ml of sodium hydroxide bath to determine the aluminum content.
Titration - Newbedford, Connecticut
A. Take a 500 ml beaker [beakers on
eBay
or
Amazon [affil link] , add 5 ml of filtered bath solution by using graduated pipette
[pipettes on
eBay or
Amazon [affil link]
. Add 150 ml of distilled water by measuring with graduated cylinder ⇦ on
eBay or
Amazon [affil link]
. Add 2 to 4 drops of phenolphthalein
⇦ on
eBay &
Amazon [affil link]
indicator. The solution turns pink colour
- Titrate the solution (titrend) with 1N HCl ⇦ on
Amazon [affil link]
(titrant) solution until the colour changes from pink to milky white.
- Record the consumed reading of titrant as "A" in ml.
- Add 5 grams of potassium fluoride
⇦ on
Amazon [affil link]
to the same solution (titrant), the colour turns pink again.
- Continue the titration with 1N HCl ⇦ on
Amazon [affil link]
(titrant) solution until the colour changes from pink to milky white.
- Record the consumed reading of Titrant as "B" in ml.
CALCULATION:
B X 1.8 = g/l of Dissolved Aluminium.
( A - B / 3 ) X 8 = g/l of Free Caustic.
CHEMIST - SHIMOGA KARNATAKA INIDA
August 26, 2023
A. Amruth is correct that titrating your 5 mL filtered sample with 1M (1N) is the best procedure. I would like to add two things.
Firstly, instead of potassium fluoride, you may use sodium fluoride. They will both play the same part, and one may be cheaper than the other for you to source.
Secondly, for samples where you expect a very high concentration of aluminum, I would suggest after reaching your second endpoint to add just a pinch more of your fluoride reagent to confirm your sample has no more remaining unreacted hydroxide. If there is any left, you will see your mixture return to the phenolphthalein pink.
Lab Rat - Fort Wayne, Indiana
December 18, 2024
Q, A, or Comment on THIS thread -or- Start a NEW Thread