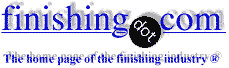
-----
Dichromate problems for hot-dip galvanizing

Q. Dear Sir,
I want to know what should be the concentration and temperature of chrome bath (hex or tri) to completely passivate the zinc coating on hot dipped galvanized pipe. Please let me know it in terms of percentage or ml/liter.
galvanizer - Anjar, Gujrat, India
2007
![]() |
A. Sir: Galvanizing Consultant - Hot Springs, South Dakota, USA A. Between 10 and 100 parts per million by mass is commonly used. That's 0.001 to 0.01 per cent by mass. Since the chromate salts are solids, your optional unit of mL/L is not applicable. ![]() Bill Reynolds [deceased] consultant metallurgist - Ballarat, Victoria, Australia We sadly relate the news that Bill passed away on Jan. 29, 2010.
"Hot Dip Galvanizing
A Guide to process Selection & Galvanizing Practice" by M. J. Hornsby ![]() on eBay or Amazon or AbeBooks (affil link) A. The required concentration depends greatly on the temperature at which you passivate. ![]() Geoff Crowley Crithwood Ltd. Westfield, Scotland, UK ![]() |
Using DI water in quench tank to minimize White Rust on galvanize
by NACE
[only rarely available]
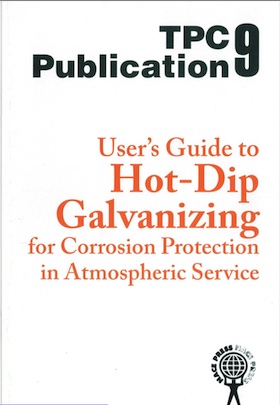
on eBay or Amazon
or AbeBooks
(affil link)
Q. Sir,
I am Arunkumar from Pondicherry - India
Currently I am using de-mineralized water for quenching tank , this seem to reduce the reaction rate of white rust.
Kindly give your opinion in this regard.
Thank you
plating shop employee - Pondicherry, India
September 9, 2009
A. I would expect that since it will have trace amounts of chloride,sulfides and other nasty anions vs tap water.
James Watts- Navarre, Florida
A. I feel the Raw water / Softened / DM water does't make any difference in quenching or does not influence the quality of the finishing of Hot dipped steel. the chlorides/carbonates or any minerals of the quenching water does not have time to react with the quenched metal parts, which are suspended while quenching that too only for a shorter period.
Water may have its influence only when the hot dipped metal is allowed to stay into quenching bath for a much longer duration.
- Chennai, Tamil Nadu, India
September 28, 2009
A. Sir:
I recently had a workshop here on the ranch and a company employee came here, for which I consulted many years ago. They had put two ion exchange canisters for the water for their quench (no chromate). It was a fairly expensive operation costing about $0.04/gallon (I think around $10,000/month). Since that time this company has been purchased by another company and now they use hex chrome in their quench and the ion exchange tanks have been removed. I had the guy bring tap water and the conductivity meter registered 200 microSiemens (about 160 ppm total dissolved solids). I doubt seriously that they needed DI water. In your case if you take the conductivity or TDS of your tap water you may get a high (or low) value and help you decide if DI water is worth the money.
Regards,
Galvanizing Consultant - Hot Springs, South Dakota, USA
October 1, 2009
Multiple threads merged: please forgive chronology errors and repetition 🙂
Q. I want to know a little bit about different concentrations of dichromate in applying with hot - dip galvanizing for milled steel . What is the suitable and economic concentration for the chromate? I am trying to use Kalium Dichromate (potassium) K2CR2O7 for the coating. Is this material suitable ?
chinnappan savariyappanplating shop employee - India
April 1, 2010
A. Sir:
Most North American galvanizers use sodium dichromate dihydrate, likely it is less expensive than the corresponding potassium salt. Also the usual concentration is around 500 to 1000 ppm and I like to use the color of the solution (e.g. standards in long, big test tubes) to estimate concentration. In use the pH of the solution drifts upward and must be carefully controlled using the proper chemicals. It is quite wise to have a water tank for quenching prior to the hex chrome tank.
Chromium trioxide (chromic acid) flake (dark purple flakes) is NOT suitable for hex chrome treatment of galvanized product. This chemical causes terrible stains on the product. Keep in mind that Europe has banned the use of hex chrome and with good reason. Hex chrome is a terrible cancer causing agent, and it easily comes out of solution into the air (e.g. the higher the oxidations number (e.g. +6 in this case)) the more covalent (more volatile) is the compound). The biggest problem is when a massive galvanized product is pulled out of hex chrome quench while it is still quite hot. At 300C, I measured 17000% the maximum CDC hex chrome in the air 4 feet above the hex chrome tank as a massive steel piece was being withdrawn.
Regards,
Galvanizing Consultant - Hot Springs, South Dakota, USA
April 9, 2010
Sludge in passivation quench of hot dip galvanising line
Q. Hi guys
I have a customer how has questions relating to the sludge build up in the passivation quench after his kettle. He has no water quench prior to his passivation and uses his passivation as a quench and passivation tank, he find that sludge builds up relatively quickly in the tank and asks the following:
1) What is the sludge caused from, is it ash, etc.?
2) Is there a way to reduce the amount of sludge build up in the passivation tank
3) Does the chemical composition play a role in how quick sludge is built up ie, do non chrome containing passivation/ quenches build up sludge quicker than chrome based ones?
4) What is the rule of thumb on the frequency of dumping this tank
Thank you
Donavan
Supplier - Germiston, South Africa
July 31, 2012
A. I've seen the same. Using a combined quench passivate, various ash drops off the work and settles in the tank.
Accumulation rate dependent on ash present, tonnage processed, and perhaps other factors too?
One method of removal is to use your drossing equipment, and at about half the frequency.
So if you dross fortnightly, then every second drossing, use the dross spoon to clean the tank. Saves pumping!
And it will settle using the same down time that the zinc requires after drossing.
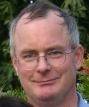
Geoff Crowley
Crithwood Ltd.
Westfield, Scotland, UK
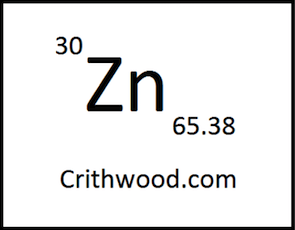
![]() |
Q. Thanks Geoff, - Germiston, South Africa August 7, 2012 A. Donavan: Galvanizing Consultant - Hot Springs, South Dakota, USA |
Q. Thanks Dr Cook
500 ppm, what would that relate to in % by vol of sodium dichromate?
Why or how would a "bad flux solution" impact on the quench and in what way? In terms of dissolved solids?
Could you expand on your comments to Geoff with the new ways to improve zinc drainage and the new technology that you were referring to?
Thank you
- South Africa
August 13, 2012
A. Donavan:
At 500 ppm (0.05%) % by weight and % by volume are virtually identical. I also used a few hundred ppm of acetic acid . Another guy thinks using phosphoric acid to control pH is better, especially if the product is to be painted. He is likely correct.
Bad flux (especially low ACNV and high baumé) causes more flux carry-over into the quench resulting in more chloride in the quench tank (at a faster rate).
Additional comments on my new process are not possible at this time.
Regards,
Galvanizing Consultant - Hot Springs, South Dakota, USA
Rinsing scheme for trivalent & silane galvanizing quenches
Q. Hello! Dear sirs, would you tell me, please, what kind of washing scheme is needed after passivation of hot-dipped zinc coatings in a solution based on trivalent chromium. And after passivation in silane-containing solution?
Kind regards
- Russian Federation
May 25, 2018
A. Hello Maxim,
I think silane based passivation systems are not mature for consistent results yet, so I would go for trivalent chromates for hot dip galvanization process.
And, it's only my opinion, for hot dip galvanized parts the customer is not looking for "better white corrosion resistance" but a good thickness for long-lasting parts in the field.
So, I hope you take the best choice for your product and your customers!!
Best of luck!
TEL - N FERRARIS - Cañuelas, Buenos Aires, Argentina
June 11, 2018
Thank you very much, Daniel, for your response. I agree that zinc mainly provides protection for parts and I suppose these two characteristics (protection and pretty good look) are not mutually exclusive. Besides, in the future, maybe, passivation methods without chromium will be preferable. I am concerned about the environmental friendliness of the process with respect to both trivalent chromium and silanes.
Best of luck for you, Daniel!
- Russian Federation
June 13, 2018
Q. Hello I'm Hatta and I got a problem with our final appearance of guardrail (whitening runs) which suspected from our chromate passivation bath because the problem not appear on batch which skipping the passivation. we control our passivation at 0.02% and pH 4.8
Mohamad HattaGalvanizing - Johor malaysia
September 26, 2019
A. Not much detail to go on to answer here..
Is all work affected by the white marks after quench? Or just these handrails?
What's in the tank? 0.02% what?
What else is in there? NaCl? KCl?
What temperature does this tank run at?
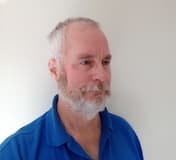
Geoff Crowley, galvanizing consultant
Crithwood Ltd.

Bathgate, Scotland, UK
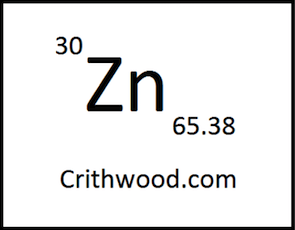
September 26, 2019
A. Hatta: You are running chromate at 200 ppm so it should be a light yellow color. Is the solution clear or cloudy? How old is the chromate solution? Is it made up from sodium dichromate or potassium dichromate or hopefully NOT chromic acid (CrO3) which stains the product. Hopefully you adjust the pH using conc. HCl. pH 4.2 is better. What is the TDS (total dissolved solids) in the chromate quench. Above about 4,000 TDS white rust is common. What is the TDS of your tap water? Sodium or calcium in the chromate quench can cause white rust. Do you use a water quench prior to putting the product into the chromate quench, so as to wash off the flux residue in water rather than the chromate quench?
Regards,
Galvanizing Consultant - Hot Springs, South Dakota
September 27, 2019
Thanks for your attention Mr Geoff & Dr Thomas. I'm using sodium dichromate at 0.02% , acetic acid to control pH around 4.5-4.8 and the temperature is 65 °C. Anyway I've tried to increase the conc. of sodium dichromate to 0.04% with pH 4.2 as told by Dr. Thomas and the problem seem to be settled but the thicker items got a bit yellowish.
Frankly I've no strong background in technical or chemistry but since following you guys it helped me a lot.
Galvanizing - Johor malaysia
October 1, 2019
A. Hatta: The Ka for acetic acid is about 10 to the minus 5 which means that no matter how much acetic acid you put in your quench the quench will not have a pH lower than 5. acetic acid "buffers" the quench to pH 5. You will need a small amount of HCl to lower the pH to 4.2. Perhaps 1/2 liter or 1 liter will do the job.
Regards,
Galvanizing Consultant - Hot Springs, South Dakota
Really appreciate on your valuable advice sir. I will try to work on it
Galvanizing - Johor , Malaysia
A. Hatta: To calculate the exact amount of conc. HCl to add to the chromate tank, put 50 ml of chromate solution in a conical glass flask, add 15 drops of 0.1% bromophenol blue
⇦ on
eBay or
Amazon [affil link]
sodium salt and titrate with 1:100 HCl (1 ml conc. HCl + 99 ml of distilled water). When the solution changes from a dark color to the normal yellow chromate color stop adding the 1:100 HCl. By proportion calculate how much conc. HCl to add to the chromate tank.
Regards, Tom Cook
Galvanizing Consultant - Hot Springs
Q. We recently had complaints from a customer that slit our hot dip galvanized material. They're complaining about black dust that formed on their felts (used for back tension) when they slit the coils.
We analyzed the dust and it shows Zinc oxide, which is normal. But why some coils and not all?
Is it possible that the sludge build up in the chrome tanks and then sprayed onto the strip surface and squeezed be the reason thereof?
Please advise.
- Vredenburg, South Africa
July 21, 2020
A. Zinc Oxide (a/k/a 'white rust') is white. That's not the answer. If the black material is magnetic, then it's either iron or iron oxide (magnetite).
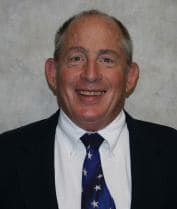
Tom Rochester
CTO - Jackson, Michigan, USA
Plating Systems & Technologies, Inc.

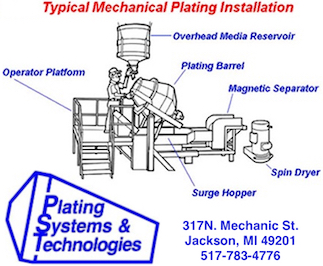
Q. Have you found the root of problem?
Black dust sticks on coil surface after chrome 6 passivation.
- HCM City, Vietnam
August 28, 2023
Q, A, or Comment on THIS thread -or- Start a NEW Thread