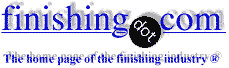
-----
Alternative to anodise?
We have recently been getting very inconsistent results when we send our parts to be black anodised, a high proportion of our parts have to be rejected due to them not being of a high enough standard. We require a very high quality gloss finish but the faults include dullness and uneven coats. The parts vary from simple flat panels to quite intricate parts.
I was wondering could anyone recommend an alternative? We would be open to any variation as long as it provided a good surface finish and was more reliable, the time lost in returning parts is the biggest issue for us.
design engineer - Dublin, Ireland
March 30, 2010
Hi, Chris. There are alternative metallic finishes including black zinc, black nickel, and black chrome. There are also various paints, powder coatings, and other black finishes.
Still, this may be a quality control issue rather than a technology issue, and usually you can't solve quality control issues by switching technologies. If you can give us more input we may be able to offer more info in the way of solutions. Good luck.
Regards,
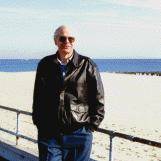
Ted Mooney, P.E.
Striving to live Aloha
(Ted can offer longterm or instant help)
finishing.com - Pine Beach, New Jersey
March 30, 2010
First of two simultaneous responses -- April 2, 2010
Thanks for the reply,
The parts I am dealing with are bent flat panels about the size of an a3 page made using 5083 aluminium. It is these parts which require a perfect finish. We also have some parts made from 6082 which are smaller, the finish of these is less important although they still have to look right.
I will look into the methods you recommended. I agree that it could be a quality control issue, I was just looking into other methods which left less room for error.
- Dublin, Ireland
Second of two simultaneous responses -- April 3, 2010
Hi Chris,
I am assuming your anodizer is not capable of getting the parts to be anodized properly jigged to the racks. Loose contacts would lead to dull and uneven coating finishes. Intricate parts need skill and an understanding on part of the anodizer to get them racked adequately and at the same time avoid racking marks on the parts.
Anodizing is used on cases of high end cameras and mp3 players and there is no reason why it can be discounted just because an anodizer is not capable of getting a job properly done.
- Bombay, India
Having reviewed our anodising process I think it could be down to the polishing stage. The polishing is done by an external polisher who does it manually, this could be where the errors are coming from.
Is it possible to get a mirror finish using electropolishing? We feel this might improve our results and eliminate the human error factor.
- Dublin, Ireland
April 6, 2010
April 6, 2010
Hi, Chris. It is possible to chemically bright dip, which is often done on lamp reflectors, or to electropolish, which is done as things as precise as telescope mirrors. But I have to agree with Winston.
Regards,
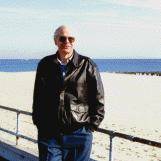
Ted Mooney, P.E.
Striving to live Aloha
(Ted can offer longterm or instant help)
finishing.com - Pine Beach, New Jersey
Mirror finish can be achieved on aluminum alloys having purity of at least 99.7% and above. This is available mostly in sheet form and used for light reflectors. Extruded alloys are of a lesser purity and while you could get good luster during the electrochemical brightening process, the luster would reduce in anodizing. Black color requires at least 10-15 micron thickness of anodizing to lock on to.
You could try buffing the sheets to a mirror finish, anodize and color them and then buff them again to get some luster back into the sheets. You could avoid electrochemical polishing if you go this route though it would not really harm the end result. You would only need a skillful buffer to do this job.
- Bombay, India
April 7, 2010
Q, A, or Comment on THIS thread -or- Start a NEW Thread