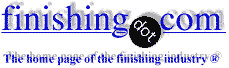
-----
Type III (hard) aluminum anodizing, sealing and surface properties
March 25, 2010
Hello,
I'm not sure if this is the finishing or engineering type of question, but maybe your experience will help to understand the process and results for a DIYer
I have some small parts (6061 T6 alloy, plunger type valves in hydraulic mechanism, will be lubricated and operate in a regular red ATF), these parts are supposed to be type III anodized, valve seat is precision ground regular aluminum casting (no special surface treatment).
The question arose after few test parts were made in following conditions:
Part are just from a lathe, washed, cleaned in industrial cleaner at
60 °C for 5 min, rinsed, etched in NaOH for 1 min, rinse, deoxed/desmutted in a sulfuric/nitric/DI water acid solution for 2 min, rinsed and into the anodizing tank:
Regular battery electrolyte (1.27) was diluted 5:1 with distilled water to lower its density a little (no additives and no break-in parts were used), then the tank was chilled down to -2 C (was monitored and maintained throughout the anodizing process), I used a graphite cathode that was around 4 times larger than the area of the part, tried 2 current densities 25 A/sq ft and 40 A/sq ft, 25 amps produced a ~0,9 micron/min thick layer and 40 amps made 1.3 micron/min, the aim was to achieve around 25 micron thick layer
In both cases of current densities the desired layer thickness was achieved in 30 and 20 minutes, tested using micrometer and measuring parts at room temperature before and after anodizing
When I retrieved the parts, rinsed them in clean water, dried, and touched with bare fingers (no gloves), then the surface seemed sticky, it was very hard (I don't have any hardness measuring tools apart from instrument steel scalpel :) ), as it should be compared to regular Type II anodizing, but still it felt sticky even after rubbing it with cloth, craping with steel, coloring in die
Then I tried to boil couple parts in distilled water for 30 min, and after that the sticky effect was gone, parts felt very smooth
And now the question - I've red that maximum abrasion resistance for Type III finish is achieved when the anodizing layer isn't sealed, but what if the other surface, that it is "rubbing" against, is considerably softer? Would sealing the part make more sense in terms of making the anodizing layer smoother so it would "eat" the valve seat?
hobbyist - Riga, Latvia
Q, A, or Comment on THIS thread -or- Start a NEW Thread