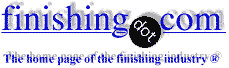
-----
Interpreting salt spray testing results
Hi, I work in a plating shop. I do hard anodize and passivation. My question has to do with test results of salt spray (Steel parts). We passivate parts per spec. The spec only allows you to passivate for a minimal amount of time. After passivation the parts get salt spray tested. We are having a major issue getting parts to pass. I know the majority of parts being rejected should not be. Its pretty obvious what rust looks like to me. Some of the parts being rejected look like they have some type of staining on there. What is the staining caused from and why does it appear on the parts. What can I do about it? I have one more question. If I had a part that's been salt spray tested and it has staining on it, if you took copper sulphate ⇦ on eBay or Amazon [affil link] and tested the stained area wouldn't it show if it was rust or not. I know copper sulphate is used to test for free iron on the surface of a part. Please let me know. It would be greatly appreciated. Thanks J.K.
Jerry KeenePlating shop employee - Wichita, Kansas, USA
January 22, 2010
Have you looked at the air lines used to provide the compressed air to the salt spray chamber? If they are steel and have corroded on the ID, that could be the source of rust on your parts. There is supposed to be a filter before the air enters the chamber. A regular paint spraying air drying /filter combination does not work. Staining can occur if the stainless is hung with something that wicks and holds liquid by capillary action. These areas have to be ignored.
As far as copper sulphate, it may not find Free iron on the surface if the passivation condition is borderline. Ferrous cyanide testing can be used as described to referee the presence or lack of non-passive areas.
metals - Paramount, California
January 22, 2010
Any ideas on what air filter it is that you use on your salt spray chamber? A model or type?
Tony Henning- Wichita, Kansas, USA
January 26, 2010
Air filtration is possible source. Suspension methods can also be suspect. We use only clean plastic/PVC racks in our chamber and ensure that any corrosion products left behind from previous tests are removed.
What is the condition and alloy of the tested parts? Machined, as-casted, shot-peened? Are the passivation baths and rinses properly maintained? More information regarding the test specimens and process technique is needed.
Aerospace - Dayton, Ohio, USA
February 20, 2010
Q. Hello, we have a salt spray chamber to test our zinc plated, hot deep galvanized and painted metal parts.
We know that 24 hours on the SST are equivalent to 1 year on a "normal" environment. But, is there any standard, chart or reference where we can interpret the hours on SST vs expect useful life?
Thanks in advance
Roberto
- Guadalajara, Mexico
May 17, 2012
Q, A, or Comment on THIS thread -or- Start a NEW Thread