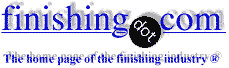
-----
Soda blasting and diluted vinegar rinsing causes cast iron to rust
Q. I am having a problem with cast iron that has been soda blasted and then rusting after the post wash. The normal post wash procedure for other materials is to use water/vinegar 40:1 solution and then rinse with water prior to paint. If any body knows of a product or solution that will dissolve the soda film and at the same time prevent rust until it can be painted and would be kind enough to share I would appreciate it.
Thanks
Frank
Frank Barrysoda blasting - Trenton Ontario Canada
2000
A. Assuming you are spray rinsing, try rinsing the soda off with an iron phosphate cleaner coater, which will passivate the casting, followed by a hot rinse. Alternative would be to use a (hot) final rinse containing 2 g/l sodium nitrite or any rust inhibitor additive available from chemical pretreat suppliers. The problem is the highly active state of the casting after blasting - you must protect the surface during dry off. A third alternative that springs to mind would be to use a dewatering solvent - like WD-40 ⇦ on eBay or Amazon [affil link] but without the oil content. R
Roger Bridger- Croydon, UK
A. You might like to try one of the commercially available, aqueous, paintable RP's that are available as a final rinse. More forgiving and better protection than the iron phosphate.
Dave Wright [deceased]- Mequon, Wisconsin
With sadness we note Dave's passing on Oct. 11, 2013. His longtime friend Anne Goyer offers a tribute to him in The Finishing Touch, Vol. 23 No. 4.
A. I once used one of the water-based rust inhibitor rinse agents on some freshly cleaned carbon steel and still saw rust form almost immediately. This is sometimes a tough application. Industrial painters also use corrosion inhibiting rinse aids that are supposed to provide flash rust protection but not require subsequent removal. You might check with SSPC, the industrial painting association.
Good luck!
Todd Turner- Monroe, Louisiana
A. Try a water soluble vapor corrosion inhibitors. They have a grade that I used to mix in our rinse water. I used it to rinse tooling that was water washed and it stopped the corrosion after the rinse.
Frederick Diekman- Streamwood, Illinois
2000
Zinc phosphated parts are rusting in process
Q. For painting pretreatment, as soon as phosphating and later passivation is done, rust is observed on the job.
How can we prevent the job from rusting.
- Pune, India
May 10, 2012
A. Hi Harshad.
One purpose of phosphating is to deter rust long enough that you have a chance to paint the item. So the problem is either that your phosphating approach is no good, or you are waiting too long to paint -- but we don't yet have any information to try to help you solve the problem. Are you using a phosphating process from a major supplier? Is tech service from them available to help you? Is it iron phosphate, zinc phosphate or what? What solution are you using in the passivation step? Thanks.
Regards,
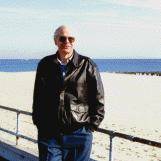
Ted Mooney, P.E.
Striving to live Aloha
(Ted can offer longterm or instant help)
finishing.com - Pine Beach, New Jersey
Q. Hello Ted,
We have pretreatment unit.
Tank 1- Degreasing agent
Tank 2- Water rinsing
Tank 3- Phosphating Solution
Tank 4 -Water rinsing
Tank 5 -Passivation
then Air drying.
However, we are facing a problem of rust mainly on the bottom side of our part which is in contact with restplate; also the rust is so hard and sticky that it doesn't get removed if not cleaned within 2 hours which is not possible in regular process. We see also sometimes blisters and adhesion problem are occurring. This is a new process I am trying to establish in my company.
- India
May 11, 2012
A. Hi Harshad. Because you have 5 stages, this sounds like a zinc phosphatizing system.
The question that you did not answer yet is whether you are using reputed processes from a major phosphate process vendor, or whether you are just trying your own home-brews. Rust, blisters, and adhesion issues represent a whole range of problems, and trying to solve them on a new startup without vendor assistance is exceptionally difficult and more than I know how to do :-(
Regards,
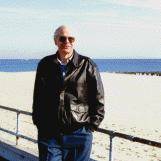
Ted Mooney, P.E.
Striving to live Aloha
(Ted can offer longterm or instant help)
finishing.com - Pine Beach, New Jersey
Ductile iron rusts within a few hours of zinc phosphating
Q. Hi,
We often find red rust in form of dots on SG (ductile) Iron casting surface within 2 to 6 hours of Zinc phosphating, both on machined and unmachined surfaces. Can someone let us know the cause of this?
- Bangalore, Karnataka, India
June 27, 2013
A. Hi Radha,
Zinc phosphate on its own is not sufficient to stop corrosion, it needs a supplementary treatment, be that a dilute dichromate seal, oil or paint. While you leave just a zinc phosphate coating as the only means of protection you will always end up with a level of corrosion.
Aerospace - Yeovil, Somerset, UK
Q. Hi Terry,
The observed rust is after oiling, subsequent to Zinc phosphating. In our steel parts, such incidences never occurred. Even in SG Iron parts, rusting is not frequent.
- Bangalore, India
July 6, 2013
A. Hi Radha,
Check the level of water in your oil, if it is over anything like 600 ppm then consider changing the oil.
Aerospace - Yeovil, Somerset, UK
A. Hi,
It is simple: blow moist free air. Check your phosphating coating it might be less or use hot water dip 80 to 90. Blow air, it will solve.
srinivas
yuken india - Bangalore, karanataka, India
April 25, 2017
Q, A, or Comment on THIS thread -or- Start a NEW Thread