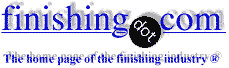
-----
Pin hole corrosion in 316 stainless steel
November 13, 2009
We have some pin hole corrosion on some 316 stainless material where marine growth has attached its self. The growth is in the form of a shelled moulusk,like a welk. Where these creatures have been attached we get pinhole corrosion like a laser penetration.
The application is a cooling chamber where sea water is used.
Anyone come across this? Is this bacterial or chemical action?
Designer - UK
November 18, 2009
Sounds like some crevice corrosion. Is this above, below, or at the waterline? It is possible that the mollusk is providing some oxygen that is needed for the rust to start. This is quite possible, since the creature takes oxygen from the water. If this is an ongoing thing you may want to use 2205 alloy to help prevent it.
If you want to repair the problem, is it possible to empty the water to a point below the rusting and fix it? Once a pinhole starts there is no way to stop if from progressing unless you grind it off or remove the rust and put a product on the surface that will prevent the water, chlorides and oxygen from entering the pinholes.
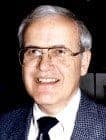

Lee Kremer
Stellar Solutions, Inc.

McHenry, Illinois
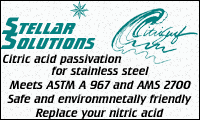
Hi Lee,
I read your reply with great interest. Obviously you are very experienced in the area of corrosion of stainless steel while it has always been of marginal involvement for me. But one point which I would appreciate further clarification is that crevice corrosion is caused by
the presence of oxygen rather than the lack of it. It was my understanding that that stainless steel required the presence of oxygen (or other oxidising conditions) to keep it from corrosion! You live and learn.
Harry
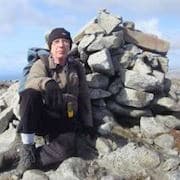
Harry Parkes
- Birmingham, UK
November 19, 2009
November 19, 2009
The problem description lends itself to two corrosion mechanisms. First would be chloride based pitting corrosion. Second is microbiologically induced corrosion. I have seen several cases where this occurs in piping systems and storage systems. It is most prevalent in stagnant or low flow areas. Most commonly, iron based or sulphate reducing organisms are present, and if chlorides are present, then the corrosion is accelerated. Time frames from 6 months to 2 years for failure have been observed.
Please note that I have no experience with mollusk organisms, but it could be a similar mechanism.
Best of luck.
Kansas City, Missouri
November 21, 2009
Found this at
www.azom.com/details.asp?ArticleID=2868#_Properties
"Stainless steel 316 has excellent corrosion resistance when exposed to a range of corrosive environments and media. It is usually regarded as "marine grade" stainless steel but is not resistant to warm sea water. Warm chloride environments can cause pitting and crevice corrosion."
My personal idea is 12 mils of epoxy. Regards
- Concord, California, USA
Thanks for the post to date.
The growth is below the water line.
A bit more information the material is 316Ti.
The construction of the vessel is cylindrical and sealed at both ends, with water inlet and outlet at one end. There are Ti tubes running inside the vessel which contain resistor heating elements. The untreated seawater is passed into the outer vessel to cool the elements. I am unsure as to the temperature of the seawater but I am guessing at may be 40-60 c on the outlet.
We also appear to be experiencing corrosion of the Ti tubes as well.
- UK
November 25, 2009
I trust that it's not too late to contribute and provide a brief response to your letter. In Australia, we are only now returning to work after our summer vacations. so I do apologize for the belated reply
The presence of oxygen is both a blessing and a curse.
To achieve an effective protection for the stainless steel, it is necessary for the chromium to oxidize and it is this process that we refer to as 'passivation.' It is therefore necessary to aim for the highest ratio on the surface of chromium to iron. To achieve this, where practicable I would recommend electropolishing for applications involving a marine environment. Firstly because of what I just alluded to and secondly, to develop a smooth surface to inhibit adhesion of any biological matter.
Should there be be any surface exposure, no matter how microscopic, of Fe, oxygen will convert this to iron oxide. That is the curse!
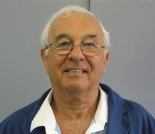
Joel Levinsohn
- Sydney, Australia
January 14, 2010
Q, A, or Comment on THIS thread -or- Start a NEW Thread