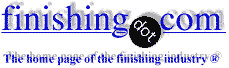
-----
Anodize is cracking
November 6, 2009
My name is Jeff. I am a Sales Engineer at a machine shop near Milwaukee WI. I have a problem with micro cracking of the Black Anodize plate on some small 6061-T6 aluminum parts that not one of three plate houses can seem to figure out. The parts were plated per MIL-A8625 Type II, Class 2. The first two platers failed on all their attempts, but the last house managed to make good parts the first two times, but now have failed in their last two attempts. The cracks are very small, you need at least 10 power magnification to see them, but they are something that the customer will not accept. The cracks run horizontally up and down the length of the part. Under 20 power magnification the parts appear to have facets, micro flat areas between the cracks.
Any ideas on this would be greatly appreciated. We have a customer who is screaming for parts!
Thanks,
Machine Shop - Oak Creek, Wisconsin, USA
First of two simultaneous responses --
Not much to go on, but it sounds like these parts have been baked after anodize. The aluminum expands many times more than the anodize, so will crack.
James Watts- Navarre, Florida
November 6, 2009
Second of two simultaneous responses --
Jeff
What are the physical dimensions of the part? On which surface(s) is the phenomena? Is the material extruded? What is the coating thickness of the anodize?
- Colorado Springs, Colorado
November 6, 2009
The material is extruded 6061-T6. It is a small turned part that is less than .250" in diameter and about an inch long. The cracks appear on all the diameters running lengthwise from end to end. The plating thickness is .0002 - .0003. Please know that these cracks are very small and can only be seen using 20 mag.
I am now working on a theory that it is the black dye that is showing the cracks and not the anodize itself.
Does that make more sense? Any sense?
Thanks, for the help.
Machine Shop - Oak Creek, Wisconsin, USA
November 10, 2009
First of two simultaneous responses --
A crack is a crack. The black just make it easier to see. Oblique light in a proper frequency will allow you to see it at 20X in the undyed part in all probability.
James Watts- Navarre, Florida
November 10, 2009
Second of two simultaneous responses --
Jeff
Anodize builds up perpendicular to the surface, so small diameters can cause 'cracks or voids' to form in the coating, although typically with thicker coatings and smaller diameters.
The fact that your second supplier was able to produce acceptable results (as well as unacceptable) suggests that there is variation within the manufacturing process. Were the acceptable parts made from the same heat lot of material as the unacceptable ones? Expect to see different heat lots perform differently with regards to anodize. Do you get your bar stock from the same supplier every time? Is your machining operation under control?
You may need to try a third supplier. Consider supplying some first article parts from the same heat lot of material to each. If you have suppliers who can tweak their process (and have control over it), they might try running at the high end of their anodize solution operating temperature, or running at a lower current density. Also, you might want to look at some parts that have been dyed but not sealed, and parts that have not been dyed or sealed, to isolate where it is occurring in the anodize process (if that is the case).
- Colorado Springs, Colorado
November 10, 2009
We have isolated the problem. The cracks are forming right at the anodize process itself. Before the dye or sealant, the cracks are numerous and readily evident. They get worse as the diameters get smaller (smallest is 0.125").
Anyone have any ideas as to why this is happening?
We are probably going to try a 7075 material and see if the cracking is better, worse or the same.
Thanks to all,
- Oak Creek
December 17, 2009
Willie Alexander answered the question, I will elaborate. All anodizing looks cracked on a curved/round surfaces because, as Willie said, the pores form vertically from the surface, so if the surface is curved the coating forms with a built-in crack. The reason that different anodizing shops appear differently is because they call use different: free acid concentrations, dissolved aluminum, temperature, and current density, all of which affect the shape of the coating.
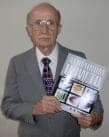
Robert H Probert
Robert H Probert Technical Services

Garner, North Carolina
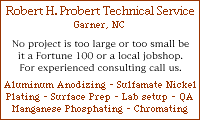
December 18, 2009
Based on Willie's and Robert's answers, I would put on the absolute minimum anodize and in the lab work on trying different temperatures. colder will be denser and warmer will be more open and probably thinner for the same time of anodizing.
James Watts- Navarre, Florida
December 21, 2009
Jeff
Have you verified the actual coating thickness?
- Colorado Springs, Colorado
December 22, 2009
I don't have the capability to check the anodize thickness, however I do know that the build-up is per my specifications .0003 per surface.
Jeff TarkowskiMachine Shop - Oak Creek
January 13, 2010
Jeff
If you are measuring a .0003" build up per surface, the coating thickness is double that. See if your anodizer can pull parts early from the anodize bath to determine at what thickness the problem is first detectable. Then see if the coating can be dyed the proper color.
Your anodizer might try increasing the anode to cathode ratio- anodize some dummy panels with the parts to create a full load.
If you have not done so already, consider fabbing and anodizing some test coupons with like diameters from other sources of material- is your extrusion a contributing factor.
- Colorado Springs, Colorado
January 18, 2010
Q, A, or Comment on THIS thread -or- Start a NEW Thread