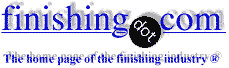
-----
Rinsing / "Spent" HCl
For Geoff Crowley (and Anybody Else):
For the last month I am calculating, and gathering information; and writing an article regarding rinsing between HCl and flux baths. There is also a large section on rinsing sulfuric acid off the steel. This article has three issues: (1) A machine that purifies rinse water (it has been working perfectly for 9 months in a plant); (2) Improved rinsing methods; (3) Rinse aids that work. At present these three appear to very greatly reduce the amount of iron+2 that transports to the flux and then to the kettle. Thus your question to finishing.com about how to get rid of "spent" flux would no longer have meaning. Predictably this rinsing process (simple and effective) would provide so small of transfer of iron+2 to the flux that purification or disposal would just plain not be required. Take note that I am extremely conservative and these methods appear very good. A reduction in spent HCl is also predicted. So far there seems to be no negatives. Incidentally it is now my experience that Iron+2 that is oxidized to Iron+3 (hydroxide) in the flux does indeed cause extra dross at the kettle. The Iron+2 that remains on the product causes longer "cook-off" times at the kettle resulting in thicker than desired zinc coating on the product.
On a different issue, I am now tracking HCl spent acid production and have found a three and one-half fold difference among plants. I know exactly the reasons for this great variation. Thus I invite you (and anybody else) to post or contact me privately and provide the liters of spent HCl produced/metric ton of galvanized steel. For some plants I believe it possible to reduce the spent HCl by a factor of 3.5 or greater.
Writing this article has taught me very much indeed. I am considering submitting it to Intergalva for Paris, 2012.
Regards,
Galvanizing Consultant - Hot Springs, South Dakota, USA
November 3, 2009
November 4, 2009
Tom (and others),
The amount of spent HCl must be highly dependent on product mix, if to be measured in liters per tonne. Plants that do a high proportion of structural steel (heavy beams sections etc) will have a lower surface area per tonne of steel to pickle than those doing secondary steelwork, and then again those doing predominantly very light section (sheet metal) even higher consumption per tonne.
But I'd guess that this ranges from 15 l/t in heavy to 35 l/t in light.
I think there are several systems of flux purification out there, and we have recently been evaluating some on offer here. These mostly claim to be able to recycle flux to the extent that it never need be disposed of (as you say).
I don't know of any rinse aids that really work, but the theory sounds OK. I just haven't come across one that does what it claims.
On rinsing methods: I know this varies from one plant to another, and age of plant, original design etc. I know of some UK plants that do not rinse at all!
My own view is that double rinsing is the minimum, and having the second rinse countercurrent flowing to the first, with top up fresh water only going to the second rinse, and that to be heated (if a source of low grade waste heat available) is best.
We have experimented with agitated rinsing, and found that this holds high promise. We have not developed this further yet, but the theory appears borne out that it will rinse much better, particularly in crevices, incomplete welds etc (the typical places for "acid weep" to form afterward).
I agree that Fe+2 not removed by rinsing, accumulating in flux and eventually reporting to the zinc, does increase dross formation. There's a strong correlation between Fe content of flux (from analysis) and dross rate of formation.
Cleaning rinse water is possible. By pH adjustment outside the rinse tank, its possible to precipitate Fe+2 as brown sludge, which can be physically removed from the stream and the "purified" water returned to the rinse tank. This reduces Fe+2 being carried over to the flux, and hence reduced dross formation.
I also agree that "dirty" flux (too much Fe in it) results in poorer
(slower) alloying leading to poorer quality, slower dipping, thicker coatings. There's a reasonable correlation between Flux Fe and average thickness of the coating.
Look forward to Intergalva 2012!
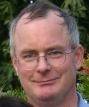
Geoff Crowley
Crithwood Ltd.
Westfield, Scotland, UK
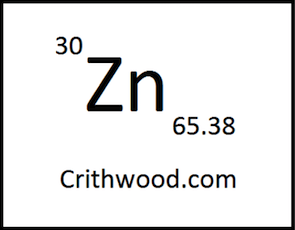
November 5, 2009
Geoff,
I have normalized liters spent HCl/MT product for 1/4 inch thick steel. Most of the galvanizers results are in the mid 20's (liters spent HCl/MT of 1/4 inch thick steel). One result is around 7. As soon as this galvanizer becomes available to me I will get more details. He pickles 15,000 tons/year of general job-shop work in a single 20,000 U.S gallon tank. Even I find this difficult to believe. I do know the several methods that he is doing correctly.
There have been perhaps six continuous flux "treatment" machines sold in North America that I am aware of. On this issue I have "no comment," because I do not want to defend myself in a lawsuit.
I agree there are many rinse aid claims with few results. I did work
33 years ago in which I discovered a surfactant that reduces the surface tension of water from 80 dynes/cm to 30 dynes/cm. Thus a basket full of parts may have 4 liters of rinse water after 2 minutes draining. This same basket filled with the same parts will have only
1 liter of rinse water after 2 minutes draining if the rinse water has 3 parts of this particular surfactant/10,000 parts rinse water. A test for this surfactant takes 10 seconds. This surfactant also prevents the pickled steel from corroding (rusting). This particular
"rinse aid" provides a four-fold improvement in rinsing for basket parts. You must not have read all my published articles.
For many, many years I have been an advocate of two rinse tanks and an advocate of counter-current rinses. Indeed, a two tank rinse system and counter-current rinse has given clean flux for many years for sulfuric acid users (if you know how to use it). Now the whole
"ball game" may have changed. If this new rinse purification
(machine, methods, aids) performs as it is currently performing in Chicago on a wire line, I may indeed be converted to one acid rinse tank without counter-current rinse. Counter-current rinse increases spent HCl, but without it (stagnant rinse) rapidly contaminates the flux. I NEVER thought I would make statements that I just have.
Hot rinse causes the pickled steel to corrode (rust) and is a waste of energy.
Agitated rinse improves rinsing about 15%, but also stirs up the dirt and iron (+3) hydroxide off the bottom.
Actually, Iron+2 does NOT increase dross in a dry kettle. In the early years I purified many fluxes (removed iron +2), but dross did NOT decrease. %GZU did decrease via thinner zinc on the product and less dry ash.
I did several lab experiments on rinse water purification using ammonium hydroxide to raise the pH and then used air, hydrogen peroxide, ozone, or electrolysis to oxidize the iron+2 to iron+3 hydroxide. Believe me this is a mess which turns to "tomato soup," and causes the steel to corrode badly. I gave up.
The guy who is building these rinse purification machines (including rinsing methods, and rinsing aids) is at the China Hot Dip Galvanizer's meeting, selling his systems. When he returns, he goes to Brazil.
I am still not sure what I will do with the article that I am writing. Paris and 2012 are too far and too long from here and now.
Thank you for your thoughtful reply.
Regards,
Galvanizing Consultant - Hot Springs, South Dakota, USA
November 6, 2009
I have a little difficulty understanding the apparent difference between your statement..
"Incidentally it is now my experience that Iron+2 that is oxidized to Iron+3 (hydroxide) in the flux does indeed cause extra dross at the kettle..." and "Actually, Iron+2 does NOT increase dross in a dry kettle..."
except that it's Fe+3 (from +2) that causes the increased dross.
Our experience is that there's a strong correlation between the two.
"Hot rinse causes the pickled steel to corrode (rust) and is a waste of energy."
It would be a waste of energy if that energy were not being wasted anyway. This heat comes from the quench tank in this case, and is not able to be used elsewhere easily. It would otherwise be wasted. The steel is not in the warm rinse long enough to get rusty, its straight into the flux afterward, and that's hot of course also. The effect is less cooling of the flux, and so less energy required to heat that flux. Net result - energy saving, not waste.
"Agitated rinse improves rinsing about 15%, but also stirs up the dirt and iron (+3) hydroxide off the bottom"
Yes it would stir up the tank if it were dirty. If its clean then not a problem. I have no measurement on the increase in rinsing, only the qualitative result that it decreases "acid weep".
There are flux / rinse cleaning machines available manufactured in USA, UK, Netherlands, New Zealand and perhaps other places.
regards
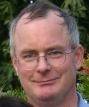
Geoff Crowley
Crithwood Ltd.
Westfield, Scotland, UK
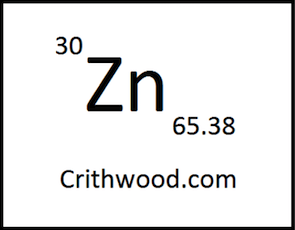
November 9, 2009
Geoff,
Fe(OH)3 (solid orange precipitate) causes extra dross.
Fe+2 (dissolved green solution) causes thicker zinc on steel. That's it. At the proper pH of 4.2 for flux, iron+2 is NOT easily oxidized to Fe+3. Fe+2 does oxidize easily at pH's above about 5.
Hot rinse, if it dries on the pickled steel allows oxygen in the air to corrode the steel. 30 years ago I saw a plant start-up in which the acid rinse was heated to 70 C. After rinsing, the steel rapidly dried as it was draining and all the steel product corroded horribly to brown-orange. The manager immediately sent the hot rinse water to sewer and the next day we started with ambient (tap) rinse with no problems. Thus we seem to be talking about hot versus warm rinse. My experience is that neither is good.
Regarding acid weep, which in some cases could be caustic or acid degrease weep (or even flux weep if flux displaces the previous liquid contents of the pocket). I suspect that whatever solution the steel is first dipped into is taken into the pocket weld (perhaps if the pocket is wide, subsequent solutions would displace previous solutions). Thus a galvanizer and I have discussed an experiment where we should put the open side of the pocket down (to keep it empty) or to fill the pocket with straight water before dipping into the first process tank. If the galvanizer does this I will get the results.
I agree that dirt or iron+3 hydroxide would only get on the product if these solids were in the rinse tank. Certainly iron+3 hydroxide is present in the bottom of most flux tanks and thus bubbling in a flux tank is likely not a good idea because it would cause excess dross.
There are flux treatment machines for sale. I do not know of any in the USA that are currently long operating. I had one of these machines on the drawing board 30 years ago. I gave up because in lab I just plain got a mess and most galvanizers do not want to be a chemical factory. I do not know of any acid rinse treatment
(purification) machines operating in the USA except the one I mentioned in Chicago.
I now have a five-fold difference for spent HCl for two galvanizers
(all data normalized). By knowing the pickling methods, I now know for sure the best way to pickle with HCl. I never thought I would learn so much about spent acid in writing an article about rinsing.
In the USA most sulfuric acid users have a crystallizer (thus zero spent acid). I have a two-fold difference in the amount of iron-zinc sulphate crystals produced by two galvanizers. AND the practices of pickling are very similar to those of HCl. There is also a correlation with concentrated acids consumed/ton of 1/4 inch thick steel.
I am now composing a list of rinsing practices and it has about 20 items. I will soon compose a list of pickling practices which will have at least three major items each for HCl and for sulfuric.
The writing is going extremely well. I now have a short data sheet for galvanizers to fill out relating to pickling, rinsing and flux practices. So far I have several plants with bad practices and only a few with good practices.
Regards,
Galvanizing Consultant - Hot Springs, South Dakota, USA
In considering pickling with HCl, perhaps you could also consider pickling in hot iron chloride.
If Kelingarn's work in HCl pickling is extrapolated, then it could be suggested to pickle in what in effect would be spent HCl, that is Iron chloride. But at this low HCl concentration, (near zero), then temp would be an important factor in speed of pickling.
I have heard of, but do not personally know of, some who apparently do this, using the iron chloride continuously with only additions being water.
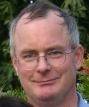
Geoff Crowley
Crithwood Ltd.
Westfield, Scotland, UK
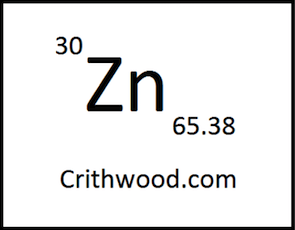
November 13, 2009
November 14, 2009
Geoff,
For hot dip galvanizing, pickling with hot iron (+2) chloride has several chemical problems including: (1) The high +2 iron concentration would cause excessive iron (+2) carry-over into the rinse and then to the flux; (2) How would zinc stripping be accomplished? (3)As zinc+2 ion accumulates in the hot iron (+2) chloride solution, the pickling rate would greatly slow down. (4) How would this zinc+2 ion be removed from the pickle bath? (5)Increased energy costs of using HOT iron (+2) chloride solution would increase production costs. (6) How would the loss of chloride ion (due to drag out) be made up? (7)Where does the oxyen+2 in the millscale go?
(chemical mass balance).
Actually there are some rinse water treatment systems in use, even in the USA. They are of two types. (1) To treat rinse water so that it can be dumped down the sewer. (2)To treat rinse water for reuse.
The first of these usually uses lime (low price) which produces cleaner rinse water and if it can be put down the sewer (most countries have a limit on zinc ion e.g. 5ppm). Also produced in this process is a filter cake which must go to an approved land-fill. Obviously this method is both labor and equipment intensive. The sewer limits on zinc tend to be more restrictive with time. Much water is wasted in this method.
The second method, which attempts to reuse the water for rinse has some chemical problems. The key here is what "base" to use to raise the pH of the rinse water. Typical bases are lime, caustic soda ⇦liquid caustic soda in bulk on
Amazon [affil link]
, ammonium hydroxide, zinc, and zinc oxide
⇦ on
eBay or
Amazon [affil link]
. Using lime gives calcium and magnesium chlorides in the flux which collect moisture and thus spatters very badly at the kettle. Using caustic soda ⇦liquid caustic soda in bulk on
Amazon [affil link]
(sodium hydroxide) gives sodium chloride in the flux which is non-volatile and causes long cook out times in the molten zinc and very thick zinc coatings on the product. Using ammonium hydroxide causes ammonium chloride in the rinse and causes the steel to corrode badly. Using zinc metal or zinc oxide raises the density of the flux and lowers the ACN, and raises the pH, and certainly causes too much zinc chloride in the flux than would normally be consumed.
The problems of these previous rinse purification methods are very substantial and completely unlike the machine, methods, and rinse aids that started this thread.
Regards, Dr. Thomas H. Cook, Hot Springs, South Dakota, USA
PS the rainbows are 2 pounds and (even though winter is starting) respond very well to hand tied dry flies.
Galvanizing Consultant - Hot Springs, South Dakota, USA
November 16, 2009
1. High Fe carryover to rinse.
Thats what the rinse is for, to rinse! A double rinse system will remove much of the Fe carryover. Besides many nearly spent HCl tanks are this concentration of iron chloride anyway!
2. Stripping should be minimised anyway, and ideally done in a separate tank to pickling. Othewise the pickle HCl gets consumed rapidly and the pickle tank gets contaminated preventing its sale as a byproduct for water treatment industry.
3. see 2
4. see 2
5. Only if the heat is from a primary source. There's much wasted heat in a galv plant. Harnessing that isn't too difficult. For example, where does the heat of the 450 deg C steel go after galvanizing.
6. In the same way that loss of any other chemical due to drag out. Like HCL, flux, etc. All these need to be topped up. So either some iron chloride added directly or perhaps (from a hybrid iron chloride
/ hydrochloric acid plant), the by-product of HCl pickling.
7. you got me on that one... :-)
On rinse cleaning.
MgO has been used successfully to adjust pH so allowing the iron hydroxide to ppt and settle.
There might be other pH adjusters that could work?
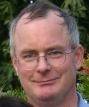
Geoff Crowley
Crithwood Ltd.
Westfield, Scotland, UK
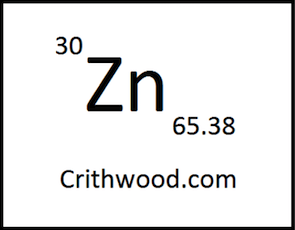
November 17, 2009
Geoff,
Regarding the use of magnesium oxide to neutralize the acid rinse and precipitate iron +3 hydroxide. The magnesium oxide could be the chemical base to raise the pH but a second agent (air, peroxide, ozone, etc.) is required to oxidize the iron +2 to iron +3. The resultant precipitate of iron +3 hydroxide looks like tomato soup and filters and filter presses like tomato soup. Not a pleasant experience.
Once the magnesium oxide is used, what is formed in the rinse water is magnesium chloride, which subsiquently is transported on the product to the flux solution. Once magnesium chloride is part of the flux solution, the flux will not dry because magnesium is a powerful collector of water from the air. Thus entry into the molten zinc has great molten zinc spatter and very much slows entry into the zinc. Magnesium chloride is not volatile, having a melting point of 708 C and a boiling point of 1412 C. Thus "cook off" times are long and thicker zinc coatings result. If magnesium chloride in the flux becomes too high percent, black (bare) spots are sure to occur. Magnesium oxide (likely formed and contained in the kettle smoke) is listed in the CDC Pocket Guide to Chemical Hazards and is OSHA max 15 mg/M3. Under symptoms are: "Irrt eyes, nose; metal fume fever; cough, chest pain, flu-like fever."
I do not know an acceptable chemical base to treat acid rinse water.
On number 7, I do not know what happens to the oxygen (actually oxide; oxygen in the -2 state), but perhaps it joins up with two hydrogen +1 ions and becomes water. Certainly for our purposes it is not important.
You never did post your liters spent HCl/metric ton and your average steel thickness in mm (a single number). I assume you are using metric there? I am still writing and the two major goals are pure rinse water (and how to use it), and how to produce less spent acid.
Thank you for your response.
Regards,
Galvanizing Consultant - Hot Springs, South Dakota, USA
1. 17 and 22 liters per tonne.
2. The theory on what happens with the magnesium chloride is sound, but the practical effect doesn't include any of the symptoms you mention. No hygroscopic effect noticed. No extra fume, no increased galv thickness, etc.
But the conc is so low that maybe this never happens. The weight of MgO consumed is insignificant compared to the volume of the rinse tank, and in addition, the rinse is changed frequently as it is the diluent for making up new acid in the pickle tanks.
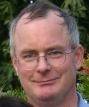
Geoff Crowley
Crithwood Ltd.
Westfield, Scotland, UK
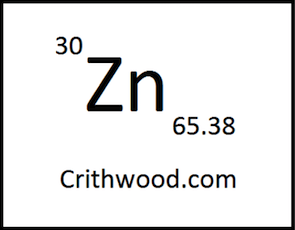
November 18, 2009
November 19, 2009
Geoff,
After several weeks of sorting out these matters, I am not even going to guess which of your spent acid numbers are for which of your two lines which likely have different steel thicknesses. Most folks would guess the lower number is for the line with thicker steel. If you could normalize the numbers to 1/4 inch thick steel (6.35 mm thick steel) then all the numbers would be based on surface area rather than tonnes.
Out of about 8 galvanizers the lowest spent HCl is 7.6 liters of spent HCl/metric tonne and the highest is 88.0 liters of spent HCl/metric tonne. All numbers have been normalized to 1/4 inch thick steel. The galvanizer with the lowest spent HCl pays $2/US Gallon of spent acid to get rid of the spent HCl, whereas the galvanizer with the highest spent HCl pays $0.20/US Gallon of spent acid.
Two days ago I was on the telephone with a galvanizer who claims to not have any spent acid for 5 years. Naturally at first, I was skeptical. Then I noticed that the galvanizer with 7.6 liters of spent HCl/metric tonne and the galvanizer saying that he has no spent acid, have many things in common. As of today, I believe that 5 liters of spent HCl/metric tonne of 1/4 inch thick steel, is clearly possible. This is with pickling times of about 30 minutes to 60 minutes. The galvanizer with 7.6 liters of spent HCl/metric tonne purifies his flux (removes iron +2) every 6 months. With the new rinse water purification device, methods, and aids, the expectation is that he will never purifiy flux again.
When you posted your response about FeCl2 pickling (e.g. high Fe+2 content and low HCl content), a fellow sent me an e-mail commenting to me that this is called "graveyard pickling," that modern high production plants cannot pickle fast enough for required production. In addition, he commented that the high iron+2 is sure to cause problems with the rinsing and flux. He is correct in his thinking from what he knows. Interestingly there is a great deal more about these systems which are unknown to almost everyone. It is sure however, that the rinse purification system (assuming is stands up to the test of time) can give clean flux indefinitely, and can reduce spent acid.
Regards,
Galvanizing Consultant - Hot Springs, South Dakota, USA
I do not understand why, with today's technology, you would be generating spent HCl unless you are diluting the acid. It is simple to chemically treat and filter the acid to remove organics and metals. Many galvanizers and electroplaters have been years without disposing of their acids (including nitric, citric, phosphoric, hydrofluoric, muriatic etc.
David French- Charlotte, North Carolina
November 23, 2009
First of two simultaneous responses -- November 24, 2009
This whole topic of pickling, rinsing and fluxing is one of great debate. There are about as many opinions as opinion givers.!
There seems to have been about twice as much correspondence generated off this board as on it (in my experience).
The whole industry could benefit from some science based research that quantifies the optimum methods and moderates those with practical advice able to be followed by the non-chemist that the typical galvanizer is.
Its an area that's riddled with old wives tales (do you have that saying in USA?), and mythology. And some of the practices that are to be found are plainly nonsense, but are sworn by all the same.
Its a pity that there isn't some form of bench-marking in the industry in order to gain the most effective use of materials. After all, the environment benefits enormously by the corrosion protection that galvanizing affords, and the saving in replacement steel it brings. But it could be an even more effective industry if we followed best practice instead of Mother Goose!
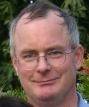
Geoff Crowley
Crithwood Ltd.
Westfield, Scotland, UK
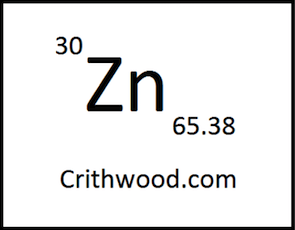
Second of two simultaneous responses -- November 24, 2009
David,
How would you chemically treat and filter HCl to remove organics and metals?
Regards,
Galvanizing Consultant - Hot Springs, South Dakota, USA
November 25, 2009
Geoff,
I too have been very skeptical of most of the claims of various additives and methods to prolong acid life and reduce spent acid. I now have four data sheets: 1)Spent HCl Metric; 2)Spent HCl English;
3)Spent H2SO4 Metric; and 4)Spent H2SO4 English. I have received several filled out data sheets and am convinced that spent acid can be reduced down to one-third or less by various methods (e.g. 5 liters of spent HCl/metric ton instead of 15 liters of spent HCl/metric ton ;normalized to 6 mm thick steel). I would be happy to publicly post these blank data sheets on finishing.com. After the data sheets are returned I can scientifically evaluate them. Alternatively let me know which one you want (likely number 1) and I will e-mail it to you.
Have you decided to not normalize your liters of spent HCl/metric ton of 6 mm thick steel and post it? You can always e-mail it to me.
I do appreciate your responses to this thread.
Regards,
Galvanizing Consultant - Hot Springs, South Dakota, USA
The responses on HCl/tonne were posted a few posts back.
I'm not sure what means you "normalised" by.
Did you use area/weight ratio?
I see the need to "normalise" for direct comparison, but you'd need good info on thicknesses etc to be able to do so. We don't keep much accurate data on quantities of steel pickled by thickness. Typically we don't make comparisons on thickness as that's a lot of work to collect, but we use average weight per item.
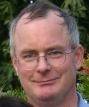
Geoff Crowley
Crithwood Ltd.
Westfield, Scotland, UK
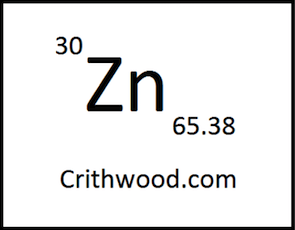
November 30, 2009
Geoff,
For normalization consider:
A center pivot irrigation company with an average thickness of 1/8 inch (0.125 inch) thick steel. If this galvanizer produces 40 liters of spent HCl/metric tonne, then normalized to 1/4 inch (0.25 inch) thick steel, then the value is 20 liters spent HCl/metric tonne (40 times 0.125/.25 = 20).
A steel angle iron tower mfg. may have 3/8 inch thick steel and produce 18 liters spent HCl/metric tonne. Normalized to 1/4 inch thick steel this would be: (18 times 0.375/0.25 = 27 liters spent HCl/metric tonne). Thus what we are doing is comparing the spent HCl/metric tonne based on surface area of the steel. The average thickness of your steel (a single number) can be determined by what lies in your yard.
Regards,
Galvanizing Consultant - Hot Springs, South Dakota, USA
December 1, 2009
Q, A, or Comment on THIS thread -or- Start a NEW Thread