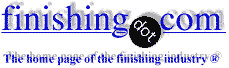
-----
Electroless Nickel plating thickness for ABS plastic
Hi,
I am a project engineer working on a component design. The part in question needs to pass 48 hour salt spray. I am wondering what the typical callout would be for an EN plating over ABS plastic. Specifically, I am looking for the appropriate plating thickness for the Cu and Ni in order for the part to pass the 48 hour salt spray. A bright finish would be nice but not mandatory. By the way, I had some prototypes plated with .0006" thk. Ni - not sure what the Cu thickness was - and the parts came back with a grayish, dull, matte like finish. I would be curious as to what I would have to specify in the plating in order to get a shiny finish (and of course meet salt spray). BTW - I have read in another post that a gray, matte finish is most likely due to excess etching time. However, I was told that no etching was performed on the ABS plastic part. Thank you.
Product Design Engineer - Milpitas, California
November 3, 2009
Most plating on plastics (POP) is done for cosmetic purposes, so it generally has to be bright and stay that way as long as possible. Typical plating cycles include EN metallization, copper, bright nickel and chrome. Automotive specifications often call for additional layers and thickness to increase corrosion and mechanical resistance. Thickness is generally around 0.001" for commercial items but I've seen 0.004" on exterior auto parts subject to physical damage. Regarding etching, ABS was specifically designed to be etched to provide a mechanical "grip" for the plated metal. This roughness should be controlled so the final brightness is met. For a good POP the plater plays the main role but the plastic processing, the resin and the mold design all contribute.
Guillermo MarrufoMonterrey, NL, Mexico
November 5, 2009

Q, A, or Comment on THIS thread -or- Start a NEW Thread