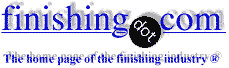
-----
Copper strike
During our Nadcap audit it was discovered that we did not ask our customer for permission to apply a copper underplate prior to electrolytic nickel per qq-n-290. Now my customer wants to know if there was testing done to confirm that it would provide better adhesion or at least would not effect the quality of his part.
any input would be appreciated.
Plating Shop employee - San Diego, California
October 13, 2009
First of two simultaneous responses --
Since you do not say what the parent metal is, the copper undercoat of the nickel plate will give at least as good a part as if it had been left out, and in some cases, it will be significantly superior to the no copper part.
James Watts- Navarre, Florida
October 14, 2009
Second of two simultaneous responses --
Hello Mark,
Although it may be a little late now, ask the customer if you could get some sample parts in for comparative testing. One lot would be plated without a copper underplate, the other lot with the copper underplate. Do adhesion testing yourself on both lots and document your conclusions.
You could send a letter with the plated samples and conclusion documentation. In the letter you could state that a copper underplate is common practice (for the substrate you have) to ensure good adhesion of the subsequent nickel coating. Also state that the copper underplate should not affect the quality of the part, and tell them why it wouldn't. In all my years of plating I never had a problem with a Cu underplate on any part.
Urge them to do any testing they would like on both sample test lots. Good Luck.
Fellow Plater - Syracuse, NY USA
October 14, 2009
November 4, 2009
Mark
The responses so far are perfectly reasonable except that as it was found on a Nadcap audit we must assume that it is an aircraft part.
Not only were you not plating to spec but there is possible impact on product (no matter that it could be better). Copper is softer than nickel and this may be a wear sensitive part.
Aircraft designers are very resistant to change when a part has a proven service history and the cost of testing any change can be enormous. They expect suppliers to do exactly what the spec says and they expect Nadcap to ensure that they do.
Next time you fly, look down and ask yourself if "should be OK" makes you feel comfortable.
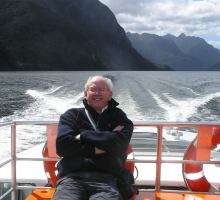
Geoff Smith
Hampshire, England
Q, A, or Comment on THIS thread -or- Start a NEW Thread