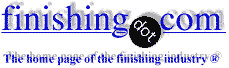
-----
Effect of Nickel plating in High temperature(900 °C) and Pressure (90 bar)
September 22, 2009
We are using Rapid Compression Machine in our experiment. We did nickel plating inside the bore of the cylinder, where temperature and pressure go as high up to 950 °C and 90 bar. And we are using hydrogen as fuel for combustion. After 25-30 times run we found that the bore is covered with black layer. And we tried to remove the black layer with acetone, but it didn't completely remove.
I want to know how nickel plating is affected in such a high pressure and high temperature.
Can we do chrome plating in above of that present Nickel plating?
Student - Akron, Oh, USA
Step 1, you do not say what kind of nickel you are using. It makes a huge difference. I think that 900 °C is way beyond the functional use on all Ni plates. EN might work. The black is probably from the organics that were plated in the NI from the brighteners.
James Watts- Navarre, Florida
September 24, 2009
Electroplated nickel melts 500 °C above that and has a compression strength twenty times higher than that. So, the temperature or the pressure (physical variables) do not play a roll here, at least, in principle. The black residue comes from a chemical reaction (of course accelerated by the high temperature). Most surely, your combustion cycle is too rich in oxygen and the nickel is oxidizing. You may want to adjust your mixture but your idea is correct. Chrome is resistant to oxidizing atmospheres and will protect the cylinder.
Guillermo MarrufoMonterrey, NL, Mexico
September 29, 2009
Q, A, or Comment on THIS thread -or- Start a NEW Thread