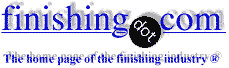
-----
Conversion coating failure
September 10, 2009
I have an aluminium die-cast housing AlSi10Mg(Fe) that is exhibiting corrosion around the threaded areas after a 30 day salt fog test. There are three different finishes on the completed part (I will call them: - internal surfaces, external surfaces and threaded areas). The threaded areas are located within the external surfaces. The internal surfaces are not exposed to the salt fog (due to the housing being sealed to IP67). The corrosion takes the form of blistering in the powder coating around or near the threaded areas. When the blisters are removed the aluminium surface exhibits the typical appearance of white and chalky corrosion. As there is no corrosion away from the threaded areas leads me to believe that the powder coating is not at fault.
After machining and deburring, the internal areas are masked off after which a chrome-free conversion coating is applied (to the external surfaces and the threads). An M8 stainless steel (316L) stud is fitted into one of the threads (this is a grounding point for the unit). The stud's threads are then masked and the remaining threaded holes are plugged. The part is then powder coated (Polyester, 2 coats
70µm minimum thickness). The masking is removed (not the stud or the plugged threaded holes) to expose the internal surfaces. The part is then plated with copper (9 to 12µm thick) followed by silver
(2µm). The silver surfaces are coated with Tarniban or Everbright. The stud is unmasked. To summarize, the finished part is powder coated with silver plated internal surfaces and (non chrome) conversion coated threads. Note é chromate surface conversion is not an option.
I am looking at preventing the ingress of liquid into the threads by mechanical methods (i.e. sealing washers), but I would rather solve the underlying cause of the corrosion by changing the coating process(es) and not the physical design.
1, I believe that the conversion coating is being breached by fitting of the stainless steel fasteners. Or the conversion coating is still too far from 316L stainless steel on the galvanic scale. True or false?
2, Would silver plating the threads (instead of surface converting) give a more robust coating (to withstand the fasteners being fitted) whilst being closer to 316L on the galvanic scale?
3, To reduce the weight of the unit in the future there are plans to change the casting to magnesium. What is the best coating conversion for magnesium (non chrome of course)?
4, This is a question about testing. Should the unit be grounded in the salt fog chamber during the test? I am wondering if grounding affects the cathode/anode relationship between the various metals.
Design Engineer - Incheon, South Korea
Q, A, or Comment on THIS thread -or- Start a NEW Thread