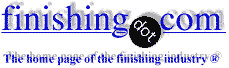
-----
Passivation of Polished Aluminum
Quickstart:
"Passivation" has a very well understood meaning when speaking of stainless steel, but its meaning in other metal finishing situations can be quite vague, referring to many different processes which reduce a metal's activity or susceptibility to corrosion.
Q. Hi,
I am wondering if it is possible to passivate aluminum? I currently have a set up for citric acid passivation for stainless steel parts. Would this same process be useable for 6061 aluminum?
- Warrendale, Pennsylvania
May 8, 2025
A. Hi Emily,
Unfortunately not. Stainless steel is a passive, inherently corrosion-resistant material, just requiring removal of any traces of iron on its surface with citric or nitric acid. Aluminum is a very active material best protected from corrosion by anodizing, chromate conversion coating, or clear coating (or paint or powder coating if you don't need to retain the grey metallic look)..
Luck & Regards,
Ted Mooney, P.E. RET
Striving to live Aloha
(Ted can offer longterm or instant help)
finishing.com - Pine Beach, New Jersey
A. Emily,
"Passivation" generally means different things for different metals.
The stainless-steel style passivation treatment is merely the removal of iron from the surface, so it's applicable to non-ferrous metals when iron contamination is involved, but otherwise it's not applicable.
The natural passive aluminum oxide surface layer forms with no intervention, you don't have to do anything.
Surface protection that's better than the natural oxide layer would involve one of the processes Ted mentioned.
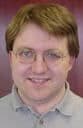
Ray Kremer
Stellar Solutions, Inc.

McHenry, Illinois
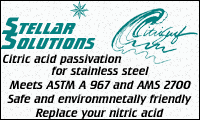
Multiple threads merged: please forgive chronology errors and repetition 🙂
Passivation of Aluminum Cylinders
Q. I need information on how to passivate aluminum cylinders prior to use and on the effects of heating the cylinders to remove moisture once the passivation coating is in place. Will the boil off of moisture effect the passivation coating? What are the effects of temperature on the metal structure and passivation coating? Any additional information on reaction mechanisms of NO or NO2 with aluminum would also be greatly appreciated. Any active aluminum sites will 'rob' the active ingredient in the cylinder fill and, with the tight product specifications in place, cause the cylinder to fail QC. Thank you for your help.
Mildred S. WeberConsulting Engineering - Baton Rouge, Louisiana
2005
A. Hi Mildred.
The usual passivation treatment for aluminum is chromate conversion coating, which shouldn't be heated above 140 °F in your drying process. Anodizing might be ideal, but maybe not. If you can't tell us what the fill material is, it might be best to privately retain a confidential consultant because the answers you receive here might be misleading when we don't know the actual situation and are just conjecturing.
Good luck.
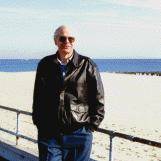
Ted Mooney, P.E.
Striving to live Aloha
(Ted can offer longterm or instant help)
finishing.com - Pine Beach, New Jersey
What is Passivate finish for Aluminum
Q. Dear all, I want to know what is Passivate finish for Aluminum heat sink.
Mingbo ZhouElectronic cooling factory - Dong Guan GuangDong P.R.China
2007
A. It is always difficult to know the meaning of a one-word finishing term like 'passivate', which is prone to be used as slang, when it is offered out of context; the more so if a language translation occurred somewhere. My guess is it is referring to chromate conversion coating of the aluminum, but you really need to find out from the customer what they want.
Luck and regards,
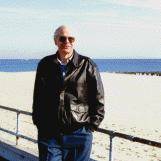
Ted Mooney, P.E.
Striving to live Aloha
(Ted can offer longterm or instant help)
finishing.com - Pine Beach, New Jersey
Q. I need to passivate bare aluminum for my project. Is there any simple way to do that? Such as immerse the aluminum bar into high concentration acid like sulfuric acid or nitric acid? Please help and thanks a lot! ^_^
Jie Liproduct designer - Hatfield, Pennsylvania
April 27, 2009
A. Hello, Jie. The word "passivate" is troublesome because aluminum cannot be passivated in the same sense as stainless steel; but it can be passivated in the same sense as zinc plating, i.e., with a chromate conversion coating. What exactly do you mean by passivate, and why do you need to do it?
Regards,
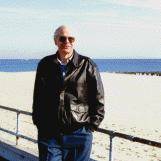
Ted Mooney, P.E.
Striving to live Aloha
(Ted can offer longterm or instant help)
finishing.com - Pine Beach, New Jersey
A. Yes, oftentimes one must be specific about what is meant by "passivation".
If the goal is simply to remove any surface contaminant iron that may have been deposited during machining and tooling, stainless steel passivation procedures apply. This can be done quite easily with citric acid.
adv. Let us know if we can help.
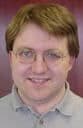
Ray Kremer
Stellar Solutions, Inc.

McHenry, Illinois
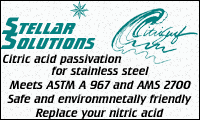
June 2, 2009
Q. I need polished aluminum sheet that will not oxidize and will maintain an emissivity of .05 over time. I believe passivation in nitric acid will do this but want to make sure I am going the right way and to find someone that can do this. Any suggestions are welcome.
Mark DiPietroDesign Engineer - Campbell, California
September 8, 2009
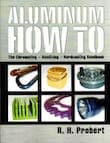
Aluminum How-To
"Chromating - Anodizing - Hardcoating"
by Robert Probert
Also available in Spanish
You'll love this book. Finishing.com has sold almost a thousand copies without a single return request :-)
A. Nitric acid passivation is a process used to remove free iron from Corrosion resistant steels (read stainless steel) and is an etchant, not a passivation process for aluminum.
Try a clear chromate or trivalent chromate perMIL-DTL-5541
[⇦ this spec on DLA] F class 3.
Metal Finishing - San Jose, California
A. For high end material, I would look at bright dip and clear anodize and sealed with DI water. You might find a suitable clear coat for it also.
James Watts- Navarre, Florida
Q. Alloy 1100-0 seems like it might be my best choice. It is resistant to corrosion and has very low emissivity. What would be issues with this?
Mark DiPietro [returning]- Campbell, California
A. This is the old problem of the term "passivation" used for multiple processes.
If the concern is surface contaminant iron turning to rust, then a stainless steel type passivation (nitric or citric based) is what will remove that iron for you.
If the concern is to protect the aluminum from something along the lines of chloride corrosion, some sort of coating or anodizing is probably best.
Of course normal oxidation on the surface is something you DO want, aluminum naturally forms an aluminum oxide layer.
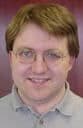
Ray Kremer
Stellar Solutions, Inc.

McHenry, Illinois
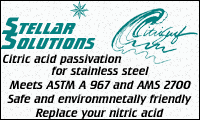
9th Edition, Vol. 5
"Surface Cleaning, Finishing & Coating"
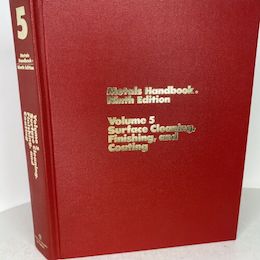
on eBay or Amazon
or AbeBooks
(affil link)
A. Hi
I believe that James is right. Bright dipping or electropolishing followed by a very thin anodizing is the way to go. ASM's Metals Handbook Vol. 5 "Surface Cleaning, Finishing, & Coating" has interesting coverage of this topic.
Luck & Regards,
Ted Mooney, P.E.
Striving to live Aloha
(Ted can offer longterm or instant help)
finishing.com - Pine Beach, New Jersey
Why does bare aluminum continues to corrode?
Q. Dear Sir or Madam, If aluminum naturally produces an aluminum oxide coat, why does it keep producing the white corrosion afterwards? How can I prevent for this to happen?
Leticia VargasAutomotive - Novi, Michigan, USA
October 2, 2018
Treatment &
Finishing of
Aluminium and
Its Alloys"
by Wernick, Pinner
& Sheasby
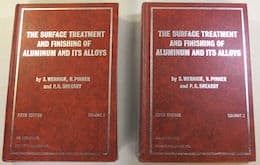
on eBay or Amazon
or AbeBooks
(affil link)
A. Hi Leticia. This issue is easier to understand if we postpone the discussion of aluminum for a couple of sentences and think about steel first. We all know from a lifetime of experience that unprotected steel will soon start rusting and just keep rusting. The reason it keeps rusting is that the rust is loose, fluffy, and hygroscopic -- the rust contributes nothing at all towards sealing the underlying steel away from the environment. On the other hand if you paint or lacquer steel, it helps keep water and oxygen away from the underlying steel and it can slow the corrosion.
Now, back to aluminum. Aluminum is a very active metal that reacts instantly with oxygen to produce an aluminum oxide white rust. In an ideal situation that aluminum oxide would be tight, adherent, and waterproof and would shield the underlying aluminum from continuing corrosion much like a paint or lacquer would; in a less ideal situation the aluminum oxide would be porous and hygroscopic, and ineffective in shielding the underlying aluminum from the environment.
Anodizing is a process of very carefully engineering and controlling the formation of that aluminum oxide in order to make it tight, adherent, and waterproof. If we simply put bare aluminum out into the environment and let the oxide form as it will, what usually happens is, depending on the grade of aluminum, the localized corrosion forces, etc., ugly white corrosion and pitting build up. Aluminum needs to be protected from the environment with anodizing, or chromating, or chromating followed by painting or clearcoating. Good luck.
Regards,
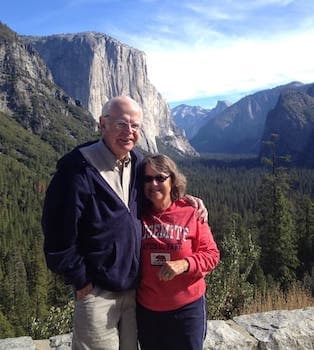
Ted Mooney, P.E. RET
Striving to live Aloha
(Ted can offer longterm or instant help)
finishing.com - Pine Beach, New Jersey
Q, A, or Comment on THIS thread -or- Start a NEW Thread