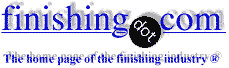
-----
Galvanisation measuring/specifying
cold rolled steel is galvanised to prevent corrosion can someone tell me how galvanising is measured and how much galvanising is appropriate for long time storing
Krishna MenonTrader - Doha, Qatar
August 26, 2009
Galvanizing is a zinc coating. The thicker it is the longer it will last in giving corrosion protection, as it is a sacrificial coating.
So the thickness is measured. Life expectancy is directly proportional to zinc thickness.
Usually measured in microns, you could expect about 100u on 6mm thick steel and perhaps 10-25u on 1mm sheet.
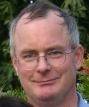
Geoff Crowley
Crithwood Ltd.
Westfield, Scotland, UK
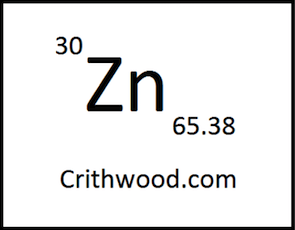
September 2, 2009
Why do I see certain galvanised products with bright Finish and certain products with a Dull grey finish . Which galvanising is better Is it possible to identify on visual inspection. Alternatively can we decide the quality of Galvanisation merely by visual inspection?
Krishna Menon- Qatar
September 13, 2009
September 15, 2009
The variety of colours seen in galvanized steel is from the fact that this is not a coating action, but an alloying reaction with steel. The zinc alloys onto the steel in several alloys mixtures, and these phases of zinc/iron have different colours. If allowed to fully alloy (by keeping the steel hot enough long enough), then the items will appear uniformly dull grey.
If the item is cooled quickly then on the surface will be pure zinc rather than alloy, and this will appear bright shiny.
If the molten zinc contained aluminium (perhaps 0.01% or less), then it might seem even shinier than pure zinc.
Typically thicker steel sections take longer to cool after withdrawal from the molten zinc, so they alloy more through the thickness of the coating, even right to the surface, showing alloy (dull grey) at the surface.
Its not possible to tell the thickness merely by a visual inspection, though an experienced observer might give a very good guess based on colour, thickness of the steel etc.
The corrosion protection afforded by alloy versus pure zinc is nearly identical, and for practical purposes is identical.
Quality can mean different things to different people.
If you want colour, then why not paint it?
If you want thickness of zinc (and so long corrosion protection life), then this might not mean anything visually.
Some measure quality in the physical surface, smoothness, lack of drips (spikes), ash, flux staining etc.
Galvanizing is not normally considered an aesthetic coating, rather a functional coating affording corrosion protection.
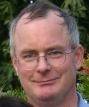
Geoff Crowley
Crithwood Ltd.
Westfield, Scotland, UK
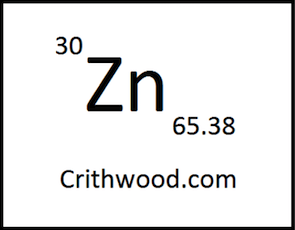
Dear sir,
I m dealing with new building of ship. we are using hot dip galvanized for the pipe through which seawater will pass of 60 &
80 schedule. I do face one problem that as per
ISO 1461, the mean coating
(minimum) on Pipe should be 85 microns and tolerance from owner is given up to 135 microns. I tried to find out max. layer thk. fail to do so. Please suggest if there is any limit for max. thk. layer. I discuss with the local galvanizer over here they are saying that as the pipie thk. is higher they have to dip the pipe more time in the bath and hence the layer becomes thicker. I wish to know that is there any process by which the thickness of layer can be reduced.
- Bhavnagar, Gujarat and India
September 29, 2009
September 29, 2009
There is no maximum stated in
ISO 1461.
Influencing factors on galv thickness include:
Steel thickness (thicker = longer immersion = thicker coating)
Steel chemistry (Some Si and P levels will give thicker coatings unless controlled by Ni present in some zinc baths)
Flux type and composition.
Item geometry (venting or air from and draining of zinc from can slow down process giving longer immersion time)
Surface profile (for example shotblasting to SA2.5 can nearly double the thickness.
The galvanizer is mainly right in saying they don't have much influence on the thickness. If you have sufficient quantity of material, you could choose a special steel chemistry that lowers coating thickness, or you could polish the surfaces prior to galvanizing, or perhaps even use thinner pipe. But most of these are impractical solutions. Why is over 130u thick coating a problem? The thicker the zinc the more protection afforded the steel.
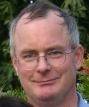
Geoff Crowley
Crithwood Ltd.
Westfield, Scotland, UK
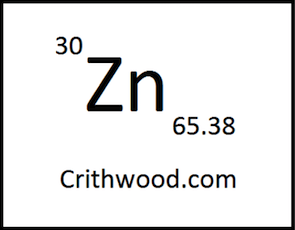
Sir:
From your question it is not known if you are having an "open kettle" galvanize your pipes or if you are having a pipe galvanizer
(automatic, pipe by pipe every 6 seconds or so). I suspect you are having an open kettle (job shop) galvanizer do the pipes in racks.
To get thinner zinc coatings a higher ACN would reduce kettle times and so would IQM.
Regards,
Galvanizing Consultant - Hot Springs, South Dakota, USA
October 1, 2009
November 4, 2010
Dear Mr. Cook,
We are steel fabrication company and we have our in house galvanizing plant.Since I have newly assigned in this department and lack of experience I am struggling to find a solution for bare spots on our job.I am thinking lack of testing in our facility could be a reason and I am planning to start it and hence I was wondering about a method for calculating pH level of our prefluxing tank.Also, could you explain what you imply by kettle times if higher ACN is used in prefluxing tank in order to reduce bare spots ?
Any help will always be appreciated.
Regards
steel company- Dhaka,Bangladesh
November 16, 2010
Salman,
For flux solution the parameters are:
Baumé (density as measured at room temperature;
ACN = ammonium chloride/zinc chloride
temperature
%Fe (iron +2 in flux)
other impurities
pH as measured by color indicators
Each of these must be correct and "in balance."
There are other ways to stop black spots and if desired to reduce zinc coating thicknesses.
Regards,
Galvanizing Consultant - Hot Springs, South Dakota, USA

Q, A, or Comment on THIS thread -or- Start a NEW Thread