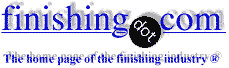
-----
Corrosion of plated Stainless Steel Sinks
August 17, 2009
My company has been having an issue with corrosion on the inside of stainless steel sinks for the past 2 months or so. I have included some photos so you can see the problem.
We have been finishing sinks in various sizes and geometries for over
25 years now and our process has remained unchanged for the past 12 years.
The alloy of the base material is unknown at this time and I am attempting to learn who the manufacturer is through our customer.
(note: this customer is the only one who has this problem)
The sink is 13-3/8" x 10-1/2" x 5-1/4" deep. Our process for this sink is:
Sand and polish the inside and lip to a mirror finish.
Apply the satin grain to the unplated sink.
Vapor degrease
Ultrasonic clean in aqueous solution
Cathodic Electroclean 3 volts for 2-5 minutes, Triple rinse
Neutralize in 5% sulfuric, Triple rinse
Chloride Nickel Strike, 5 volts, 200-250 amps for 2 minutes, Triple rinse
Flat Nickel Plate, 4 volts, 60-70 amps, 3 minutes. (flat ni = bright ni with no brighteners)
Then we apply a flash of the final color. In this case it is an almond gold although it is difficult to see in the photos.
This sink was never placed into service and the spots you see were formed in the matter of a few weeks from plating. Since we never have had this problem with any of the thousands of sinks we have plated in the past 25 years I'm thinking this problem was caused by;
a change in base material;
a change in manufacturing process (maybe mfg has eliminated passivation from their process);
or a cleaning product at our customer. (maybe bleach or an acidic cleaner).
What are your thoughts on this?
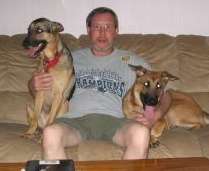
Tim Hamlett, CEF
- West Palm Beach, Florida, USA
I would suggest to check filtration ,dummying and a test sample of other type of steel.Good luck
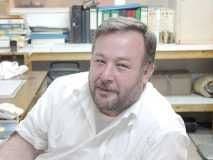
Khair Shishani
aircraft maintenance - Al Ain, UAE
August 19, 2009
Hi Tim,
Because your company has been so successful over the years producing a good product, I would say the sink mfg for this particular customer is suspect. Because your nickel thickness is low, any imperfection in the base material will bleed through in a short time. You could ask your customer if they receive material certs on the steel for each lot coming in. Also it wouldn't hurt to see if the mfg changed their process in the past two months. Good Luck!
Fellow Plater - Syracuse, NY USA
August 20, 2009
Addition information:
I have learned that the sinks are made from either 301 or 304 SST and the manufacturer does not perform a passivation step because no steel tools are used in their process.
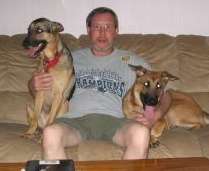
Tim Hamlett, CEF
- West Palm Beach, Florida, USA
August 20, 2009
September 4, 2009
Here is some further info just to let people know what is happening with this issue.
I had the sink cut up and sent to a metallurgical lab. they performed an EDS on three areas. The center of a pit, the dark area around the pit and an area of no corrosion.
As expected the area of no corrosion only gave evidence of the elements of the 304 stainless and the coating system. The dark area around the pit returned a high level of carbon which we are at a loss to explain. Maybe it is carbon from the 304 SST that came out of the alloy during the corrosion process.
The center of the pit showed evidence of potassium chloride. Potassium chloride has many uses including fertilizers and solder fluxes. Our customer resides in a highly industrial area of the midwest and it is possible the KCl came from the environment. Or since this is a sink, maybe from fluxes used in soldering pipes although I don't know if sweated copper pipes are used in an aircraft cabin.
An audit of the fluxes, cleaning products, waxes and all other chemicals we use here showed that KCl is not in any product we use at our shop. We are confident that the problem did not orginate in our shop or process.
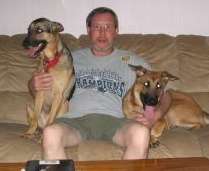
Tim Hamlett, CEF
- West Palm Beach, Florida, USA
Q, A, or Comment on THIS thread -or- Start a NEW Thread