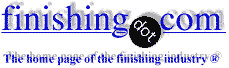
-----
Adhesive bonding problem: aluminum alloy part w/ anodized surface
Q. We are seeking a type of Glue to bond Aluminium parts.In fact, we have aluminium strips and we want to bond them with Aluminium tubes. We prefer the glue to be dried in ambient temperature.
George Zafiropoulos- Kallithea - Athens - GREECE
2003
2006
Q. My name is Mike Guarino. I am currently working on an Electro-Mechanical assembly that needs to pass the immersion test specified in Mil-Std-810-F in section 512. The unit will be dunked in a cold state (not at running temperature). The target ambient operating temperature range is -20 (Goal) to 60 °C. Atmospheric pressure consistent with ground based environment.
I am currently specifying to weld the "Outer Shell" together. Picture a tongue and groove with weld on one side of the groove. The vendor has been complaining that the welding is distorting the assembly. He also said that because it is welded does not mean it will not leak as some welds are porous. He recommended bonding it together. Both pieces are 6061 T6 aluminum alloy. I found a couple of adhesives I'm considering and was wondering if any one out there had any experience with them. They are:
3M Automix 8115 1 part adhesive
⇦ on
eBay or
Amazon [affil link]
,
3M 5042 1 part Adhesive ⇦[ed. note: UTL, might be a typo]
and
Click Bond CB200 2 part Acrylic adhesive ⇦[clickbond.com].
I was also considering using some of these Aluminum radiator sealants found at your local Auto parts store. After the bonding process there is a machining operation so whatever it is it needs to be able to be machined.
Michael Guarino- El Cajon, California
A. Sure will bend or warp IF you put too much heat in the weld. A proper weld is not porous to water or air and only minimally porous to helium gas.
I do not think that he wants to work on hard parts.
That said, there are some good adhesives on the market. Talk to tech services of major companies like 3-M and Master Bond and ? The UV cured ones are nice because there is no cure until you hit it with a particular frequency light beam, and then it is much faster. No pot life to worry about, no mixing and can be readily automated.
- Navarre, Florida
2006
July 27, 2009
Q. I have used UV adhesive to bond the aluminum 6061-T6 parts which is coated with the Anodized surface per MIL-A-8625 / MIL-PRF-8625 [⇦ this spec on DLA], Type II, class 2 and Nickel acetate seal.
According to the Q/A info from your web site; the anodized surface on Aluminum alloy provides a very good substrate for adhesive bonding. Don't understand why my epoxy bonding failed.
My bonding failure phenomena is as below; after applied small pull force (approx. 10 lbs), bonded surface was separated (plain machined surface w/o anodize coat can withstand 60+ lbs pull force w/o failure), some of the adhesive layer sticks to one part, some of the adhesive layer sticks to it's mating part. The area missing adhesive layer is very clean, there is no adhesive retained at all. I am sure I have cleaned both mating surfaces with IPA thoroughly before applying adhesive.
Please let me know the cause of failure. Is anything wrong with the Anodize type II or the seal method?
I was told that Phosphoric acid anodizing is the best for adhesive bonding. Can you tell me what is the theory behind, why it is better and how to call out the spec. in my part drawing.
Your prompt reply will be highly appreciated.
Regards
Design Engineer - San Jose, California
A. Zinc phosphate is frequently used on both steel and aluminum. A slightly different makeup for aluminum.
My guess, based on your description of glue failure on both parts is that your IPA cleaning step is just spreading a contaminant around the part, rather than removing it. To be effective, it needs new cloth and new solution for each part.
- Navarre, Florida
July 30, 2009
by J. D. Minford
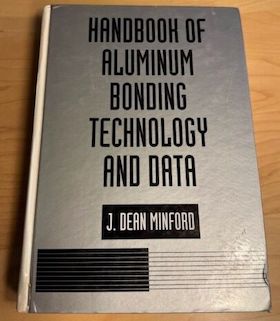
on eBay or Amazon
or AbeBooks
(affil link)
A. Ed,
The first problem you have is that you have sealed your anodising. epoxy adhesive
⇦ on
eBay
or
Amazon [affil link] s need something to "grab onto" to bond. If you seal the coating you reduce the places that the adhesive can bond to. Did you use an adhesive primer or adhesion promoter? I would recommend this as the primer will have a better key to the anodising.
Phosphoric acid anodising is generally regarded as the ideal surface for bonding. This is because the anodising produces "finger like" protrusions from the anodising surface, increasing the surface area and improving the mechanical key for the adhesive.
aerospace - Yeovil, Somerset, UK
August 3, 2009
Q, A, or Comment on THIS thread -or- Start a NEW Thread