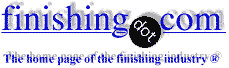
-----
Corrosion of 17-7PH Despite Passivation
July 22, 2009
Q. I have a material 17-7PH with evident traces of corrosion. The parts have been passivated as per AMS2700 II and after a SEM analysis these are the results:
1. Intergranular Oxidation under external layer for 60 micron.
2. Presence of decarburated external layer with 290 HV instead of 441 HV in the core.
3. Strong presence of CL and NA on the rusted surface (salt?) with presence of K and S.
I understood that the corrosion probably comes from salt but do you have an idea why the passivation (applied correctly) has not protect the parts?
Potential Root Causes?
Thanks a lot for your support.
student - Italy
A. Some thoughts. The material was not hardened in a controlled atmosphere or vacuum furnace, so it has changed the outer layer of the material--which I think probably has contributed to the corrosion because of the different metallurgy. Definitely, the part was not rinsed with high quality water, preferably with DI. Tap has proven to not be good enough. The parts should be blown dry rather than just letting the water evaporate as it leaves "stuff" that is sites for the corrosion process.
James Watts- Navarre, Florida
July 27, 2009
Passivated parts Per ASTM A967 show signs of rust
Q. We have some SS 17-7 PH CRES ANNEALED ASTM A693 parts that were passivated to ASTM A967 showing signs of rust. Our passivator cannot give us a reason of why they are showing signs of rust. Some of the parts are 2 years old. Can someone let me know how long the passivation should hold up and what can be causing this problem. We received parts back from our customer but they show no signs of rust. They are packaged in the original boxes we shipped in. It seems that once our customer's customer assembles them and puts them in the cargo planes is when the rust is showing up.
Lisa WheelerQC Manager - Santa Fe Springs California USA
October 10, 2016
A. Lisa,
Passivation removes iron from the surface, enabling a good chromium oxide layer to form. What happens after that depends entirely on what environment the stainless experiences. In a cool, dry place, even mild steel won't rust. Down at the beach, most grades of stainless will start corroding within a year.
All A967 requires is the parts to pass one of the listed tests. If you require something more than that, you might want to specify to your supplier that you require parts that pass, for instance, the salt spray test for X number of hours where X is much larger than the "2" in A967.
In the specific situation you mention, I might ask how soon after installation is the rust appearing, what cleaners or other processes are they using, are these planes in service in marine environments. It's very possible that the end user is doing something unwise to the parts that is allowing corrosion to occur.
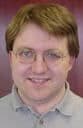
Ray Kremer
Stellar Solutions, Inc.

McHenry, Illinois
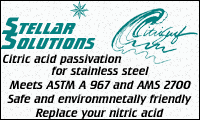
October 25, 2016
Q, A, or Comment on THIS thread -or- Start a NEW Thread