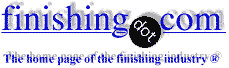
-----
Powder Coating has roughness/bumps under it
Q. Hello Bob Utech, may I ask you a question?
Currently, I am working at a powder coating company, and I have a difficult problem that cannot be solved in that my glossy flat powder coating surface is sandy on the surface after drying at a thickness of about 30-50µm. Can the cause be sand particles caused by the crusher? Thank you so much
- Bien Hoa Vièt Nam
April 22, 2024
A. Hi Nhat,
Bob hasn't been back for a long time but there are other readers who should be able to help you. A picture emailed to mooney@finishing.com would surely be helpful. What 'crusher' are you referring to?
Luck & Regards,
Ted Mooney, P.E. RET
Striving to live Aloha
(Ted can offer longterm or instant help)
finishing.com - Pine Beach, New Jersey
⇩ Related postings, oldest first ⇩
Q. I am involved in a paint line project in which we are trying to increase our FPY.
We have several substrates that we powder coat through a Wagner Paint Booth- the majority of which is galvanized steel tubing.
Our supplier is Allied from the Chicago area.
One of our biggest defects is what we term 'roughness'.
I describe this as a line of bumps under the cured powder coat. Location can be in a straight line on the part and sometimes in little clumps.
We have people hand sanding parts as they are hung on the conveyor line prior to wash.
We cannot seem to solve this issue as it seems to be intermittent.
I would appreciate your thoughts.
Engineer - Minnesota
July 22, 2009
for Shops & Engineers

avail from eBay, AbeBooks, or Amazon

avail from eBay, AbeBooks, or Amazon
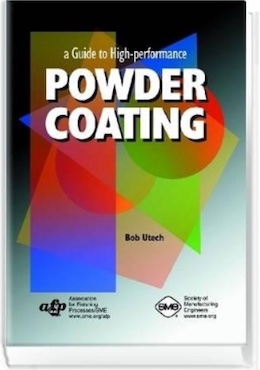
avail from eBay, AbeBooks, or Amazon
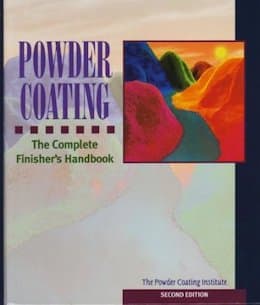
avail from eBay, AbeBooks, or Amazon
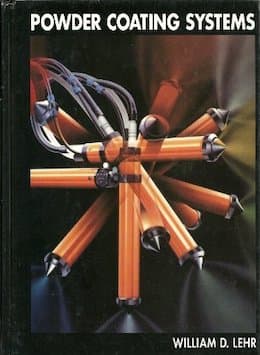
avail from eBay, AbeBooks, or Amazon
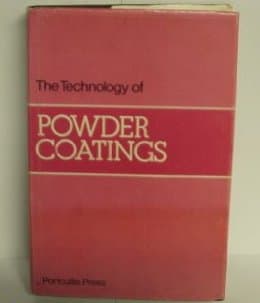
avail from AbeBooks, or Amazon
avail from AbeBooks, or Amazon
(as an Amazon Associate & eBay Partner, we earn from qualifying purchases)
A. Hi Matt, I have used this particular company's product in the past and when the pipe came in, it had a light coating of clear on it. Initially I was very leary that the powdercoat would not stick to it. The coating is a proprietary seal used to help promote product longevity. I made extensive tests on this coating and found it did hold up to all my tests including salt fog, UV and destructive tests. You cannot order their product without it as they coat all their pipe in this solution. It gets dunked in the solution and ultimately there can be areas that are not cosmetically pleasing. They use a triple coat in-line galvanize system during the coating process which provides the protection needed along with this proprietary submersion. I'm not sure if this is what your problem is, but may be possibly. Bob
![]() Bob Utech Benson, Minnesota |
![]() Ed. note: Bob is the author of: "High Performance powder Coating" on eBay or AbeBooks or Amazon [affil link] |
![]() |
A. Galvanizing isn't a very smooth finish and to get a good smooth finish with powdercoating over galv, it's necessary to smooth the galv first. There are several ways: ![]() Geoff Crowley Crithwood Ltd. Westfield, Scotland, UK ![]() A. It might help if you knew what the bumps are made of. Dissect one with a razor blade (it's already a reject) and go from there. It might surprise you at how easy this problem could be solved at this point. A little information goes a long way. ![]() Sheldon Taylor supply chain electronics Wake Forest, North Carolina A. I offer two explanations for the roughness... the first being the most likely. Birmingham, United Kingdom Q. Are you suggesting that an inconsistent "clear coat" on the tube could cause our roughness? How specifically would this cause the defect? - Plymouth, Minnesota, USA |
A. WOW where did that primer come from? It wasn't there in your first post and we can't blame anyone for answers to correct a one coat powder defect. Anyway, this puts a whole different approach to your problem. Let us establish that there are NO apparent defects in the primer coat (You don't mention any) then we would suggest that the film weight of the primer could be around 4 mils (please check this out). If so as the application of powder is self limiting it therefore follows that if certain areas of the primer are higher in film weight (4 + mils) then you must lower the Kv (40-50) of the equipment when applying your second coat otherwise the defects you mention could/will occur. I would suggest you lower the Kv for the second coat anyway.
Terry HicklingBirmingham, United Kingdom
A. Inconsistent "clear coat" on the tube can certainly cause roughness or at least inconsistent cosmetics! Specifically this "clear coat" causes the defect to telegraph through to the very top layer or surface.
When you add another layer of powder, you can readily see that your defect gets worse. This is also a reason to sand when re-coating. It helps to eliminate telegraphing if there are imperfections on the surface.
Remember that your tubing is produced by different employees in different shifts. This is presuming you are using this particular clear coat product. You can tell by lightly sanding the surface and looking for the "clear" coating material to be abraded away from the tube.
What have your suppliers told you about this problem? They should be of assistance to you.
![]() Bob Utech Benson, Minnesota |
![]() Ed. note: Bob is the author of: "High Performance powder Coating" on eBay or AbeBooks or Amazon [affil link] |
Q, A, or Comment on THIS thread -or- Start a NEW Thread