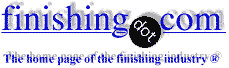
-----
Prevention of "splinter" formation on C360 brass during 240 grit belting.
June 26, 2009
I'm the Finishing Manager at a plumbing products manufacturer. We apply a variety of decorative finishes to brass substrates and encounter the formation of brass "splinters" on the surface after 180 or 240 grit aluminum oxide belting. These defects are small (perhaps 100 - 200 microns long) but after nickel plating they become large enough to catch lint particles and after clear lacquering they appear as "dirt under the lacquer" (see image).
The clear lacquer magnifies the particle size due to the lens effect. The defects appear on sheet metal, castings and forgings but the severity seems to have a correlation to the source of the brass. The slivers could possibly be removed through the use of an etch process before plating but I'd rather correct the root cause as opposed to adding additional processes. My question is can these defects be prevented by changing the belting operation (different abrasive type, faster or slower belt speed etc.), or is the problem related more to the quality of the brass material?
John KosturaCaptive shop employee - Santa Ana, California, USA
First of two simultaneous responses --
240 grit is pretty rough, and I'm not surprised that you get splinters. If you can use a finer grit, that would help. Also try being less aggressive, remove material more slowly. Reduce belt pressure and possibly speed.
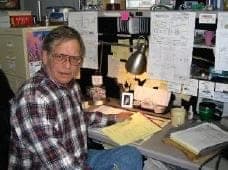
Jeffrey Holmes, CEF
Spartanburg, South Carolina
June 30, 2009
Second of two simultaneous responses --
My GUESS is that the small lead particles in the leaded 360 brass are what's giving you the slivers. If so, changing to another brass alloy without lead or similar free machining additive would eliminate the problem. If my company had the problem, I'd use our SEM to substantiate this guess. There are a lot of commercial laboratories with scanning electron microscopes in the Southern California area, so it wouldn't be difficult for you either.
If that isn't the cause, I can't think of anything else obvious.
Good luck!

Lee Gearhart
metallurgist - E. Aurora, New York
July 1, 2009
Q, A, or Comment on THIS thread -or- Start a NEW Thread