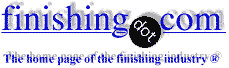
-----
Salt spray comparison of solid brass vs. brass plating
Q. Is there some sort of reference or guide to estimate the salt spray test result of brass, compared to brass-plated steel?
Leo Dizon- Chino, California
June 18, 2009
June 19, 2009
A. Hi, Leo. Brass plated steel will develop red rust when the brass plating (and underlying plating, if any) is permeated, and presumably the appearance of red rust is what would define failure. How many hours this will take will depend on the thicknesses of the plating layers, but it usually won't be too many. Usually, but not always, there will be nickel plating under the brass plating, and the nickel must also fail before rust will appear.
Solid brass can never rust, although it can certainly corrode, so what constitutes test failure for you? Both solid brass and brass plating are often lacquered to prevent tarnish. Maybe you define failure as the beginning of tarnish?
Please try to tell us your situation. There are so many unknowns here that it difficult to figure out what kind of information will be helpful to you. But also remember that salt spray is a QA tool used to keep the process under control. It is meaningless to compare the salt spray hours of one finish to the salt spray hours for another since it usually says nothing about their real-life functionality. Thanks.
Regards,
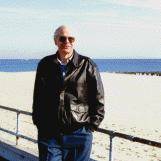
Ted Mooney, P.E.
Striving to live Aloha
(Ted can offer longterm or instant help)
finishing.com - Pine Beach, New Jersey
Salt spray test for CRCA, brass and copper as a base material
2007Q. We have a barrel plating shop. We are in plating line since 10 years. We want to know SALT SPRAY TEST REPORT for the following items:
BASE MATERIAL -- PLATING STD. -- SALT SPRAY HOURS
CRCA -- Acid Copper, 5-6 Micron ?
EN-1A -- Acid Copper, 5-6 Micron ?
ETP -- COPPER TIN, 5-6 Micron ?
BRASS -- Copper 2 Micron, Tin 6 Micron ?
BRASS -- Copper 3 Micron, Nickel 5 Micron ?
We want to know under this condition how many hours it will withstand. Kindly suggest us standard for the same.
Plating Shop Owner - Pune, Maharashtra, India
A. Hello, Dhananjay, welcome. Some plating specs will define failure and tell you how many hours of salt spray they must resist before that failure. But I'm personally not aware of "standard" salt spray hours for any of these finishes. Sorry. You have been in the plating line for 10 years now, which represents a good depth of experience. Probably you have some test results that you can run up the flagpole for discussion? Please try hard to personalize it so we can get some dialog going here for you. The readers volunteer their time on propositions that interest them; unfortunately, abstract and flash-card style questions tend to not interest anybody, so I don't know if you'll get help here with your questions as they stand. Thanks!
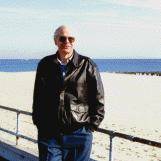
Ted Mooney, P.E.
Striving to live Aloha
(Ted can offer longterm or instant help)
finishing.com - Pine Beach, New Jersey
2007
Need 48 hours salt spray resistance from brass plating on nickel plating on steel
Q. I have to achieve 48 Hours of Salt spray test on the Brass plating. The Base Material is Ferrous, on the material is Nickel Plating of 3 microns, followed by Brass Plating of 1 micron and Clear type Passivation and Top coat.
Manimaran A- Bangalore, India
April 1, 2014
A. Hi Manimaran. I think it will all depend on the topcoat. 3 microns of nickel isn't much, and 1 micron of brass may provide color but isn't even worth mentioning in terms of corrosion resistance, but a good clearcoat can probably do 48 hours on its own :-)
Regards,
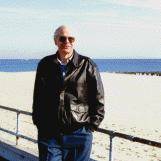
Ted Mooney, P.E.
Striving to live Aloha
(Ted can offer longterm or instant help)
finishing.com - Pine Beach, New Jersey
May 2014
Accelerated Corrosion Testing for Brass
Q. What tests are recommended for accelerated corrosion testing of Brass components?
For steels we use both salt spray and mostly humidity chamber tests but am not too sure how applicable they are for brass.
Also, would patina/de-zincification/red tarnish be the determining factor as corrosion? Can anyone also be kind enough to let us understand how the corrosion phenomenon works and under what conditions/factors?
Thanks in advance.
- ahmedabad, India
May 7, 2014
A. Hi Abishek ,
Which plating (+ under coat) on brass you want to know accelerated corrosion testing?
Regards,
Process Engineer - Tumkur , Karnataka , INDIA.
May 16, 2014
Hi Surya,
We are not using plating ... Our whole component is Brass.
- Ahmedabad,Gujarat, India
May 22, 2014
on eBay or Amazon
or AbeBooks
(affil link)
A. Try next book:
Corrosion Tests and Standards, by R.Baboian/Ed./, Baltimore 2005.
Hope it helps and good luck!
- Zagreb,Croatia
May 23, 2014
Q. I have same question already raised by Abhishek.
How can we conduct corrosion test of brass components? Is salt spray test applicable to check corrosion resistance life of Brass components?
Thanks,
- Nagpur, Maharashtra, India
November 28, 2015
December 2015
Hi Jeet.
Can you tell us whether the question is addressed in the reference that Goran steered us to? Thanks!
Some photos of some brass fittings after 96-hours of salt spray can be seen at this reference.
Another good reference is https://www.copper.org/applications/rodbar/alloy360/corrosion_tests.html
But ... a fundamental misunderstanding seems to be running through this thread. You need to define for yourself what constitutes failure! The slightest tarnish of a concert piano hinge or a saxophone might be deemed failure, whereas a brass pipe fitting may not have "failed" after 75 years as long as it doesn't leak, and a ship's bell or a military belt buckle might be expected to be polished to remove tarnish every single morning. Also there are thousands of different brass compositions; there is no abstract, general, way for others to tell you what should constitute 'failure' in your unspecified 'brass component'.
After defining acceptable real life and what constitutes failure in real life, you define a process that delivers that acceptable real life (blasting, buffing, tarnish preventers, clearcoat, etc.) ... then you may try to determine how many accelerated corrosion hours that process can deliver before some cut-off point, and then might use that accelerated test as an early warning system against losing control of that process. Good luck!
Regards,
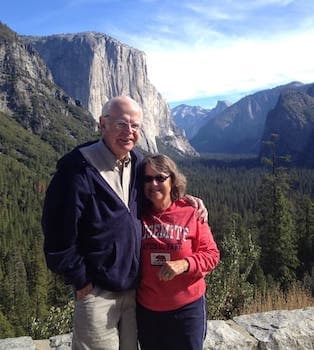
Ted Mooney, P.E. RET
Striving to live Aloha
(Ted can offer longterm or instant help)
finishing.com - Pine Beach, New Jersey
Q, A, or Comment on THIS thread -or- Start a NEW Thread